摘要:本文介绍了薄壁铝合金型材挤压工艺过程的计算机模拟及优化技术的发展与实际应用。使用QForm软件挤压模块,可以模拟由于材料流动不均匀,铝合金在挤出后可能会发生的扭转和弯曲现象。还可以精确计算材料流动的其它方面,例如空心型材焊合线的位置等。软件对于型材挤压有专门的操作界面,能快速导入几何模型,自动生成有限元模型,还可以自动识别工作带且把他们参数化,易于修改调整。通过工作带编辑器对工作带区域进行修改和优化,可以得到均匀一致的挤出速度和规则形状的型材。另外通过模拟技术还可以分析模具设备的应力和变形。
简介
QForm挤压模块是由QuantorForm公司为分析铝型材挤压工艺而专门设计开发,它是基于QForm3D的金属成型分析基本模块。这个专门的挤压模块在稳态阶段使用拉格朗日-欧拉混合模型[1,2]。此模型假定在模拟之前金属已经充满模腔进入准稳态,也即当材料流经模具时网格时可以不用重新划分,只需要计算节点的流动速度即可。型材的挤出速度很快,但是由于型材挤出的速度不一致可能会发生弯曲,扭转或变形。使用模拟的方法可以预测这些变形并找到方法控制使变形最小。这对于模拟结果及和实际相比较从而在一定范围内优化模具的工艺参数是非常有意义的。世界上很多企业有很多工业案例对模拟结果进行了验证,其中包括了载荷,材料流动流线,型材温度和模具变形等结果。同时国际挤压模拟测试大会上对模拟软件精度也有比较综合的分析。下面是一些计算结果分析。 (2007年会议在意大利[3] ,2009年德国会议[4] 2011年意大利会议[5]).
一 型材挤压数学模型的简要介绍
从模型上的一个节点来看挤压过程中最重要的阶段是准稳态阶段,这是产品形状和属性的形成阶段。在准稳态阶段,一些参数比如温度和载荷取决于模具内坯料长度的减少和坯料与模具的热交换。一般来说型材挤压模拟需要的数据为:
CAD软件生成的模具几何模型
坯料的属性(流动应力和热物性参数)
坯料与模具之间表面的接触条件(摩擦,热交换系数,和模具温度)
工艺参数(坯料的初始温度,挤压速度和挤压力)
在QForm中挤压工艺过程模拟是在一个叫做模拟域的范围内进行。模拟域是模具组合体包括到工作带出口的整个区域。对于实心型材来说模具组合体一般包括导流板,模具,模垫和模座。空心型材来说,模具组合体包括导流板、模套、模具、模垫和模座。
空心和实心型材两种情况下模具组合体最终与挤压筒装配在一起。因此坯料会接触挤压筒和挤压模具。模座等装置和材料没有直接接触,不包含在模拟域内,仅在模拟模具应力和型材弯曲的时候考虑。
在2011年,意大利的博洛尼亚市举行的国际挤压标准件测试大会上,我们用QForm-Extrusion分析了相应的实验模型。工艺及参数细节内容可以详见[5]。工艺为两个简单空心型材同时挤出,其中两个型材壁厚不同,焊合室设计也有不同。型材形状和模具网格生成步骤见图1.
在2011年,意大利的博洛尼亚市举行的国际挤压标准件测试大会上,我们用QForm-Extrusion分析了相应的实验模型。工艺及参数细节内容可以详见[5]。工艺为两个简单空心型材同时挤出,其中两个型材壁厚不同,焊合室设计也有不同。型材形状和模具网格生成步骤见图1.
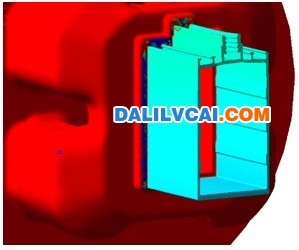
(a)
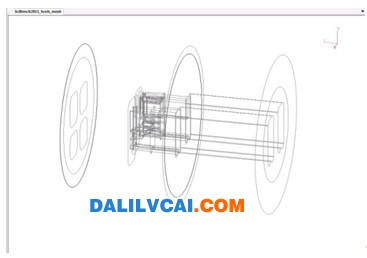
(b)
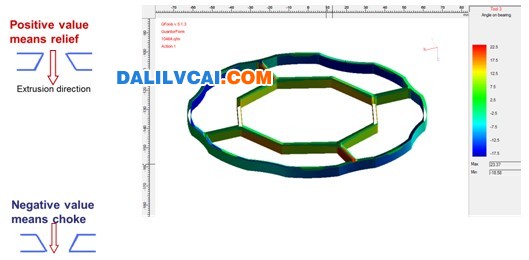
(c)
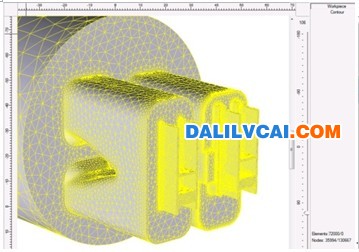
(d)

(e)
图1 测试用空心型材图(a) ;几何模型导入到QForm-Extrusion中(b);生成网格 (c);
模拟域与生成的网格(d);用于模拟的整个模具组合体网格 (e)
内部网格使用四面体网格,为了保证得到精确的结果有限元网格的大小非常严格。网格不够致密或网格大小梯度变化过快都可能造成计算不收敛,从而引起模拟质量变差。这在工作带入口变形最剧烈的位置处尤为严格。在QForm-Extrusion中可以自动完成这种网格优化,这为精确模拟挤压工艺过程提供了先决条件。
模拟域与生成的网格(d);用于模拟的整个模具组合体网格 (e)
为了精确模拟挤压工艺过程中的材料流动,我们要考虑坯料与模具组合体之间的实际摩擦和热交换。大量实验和理论研究表面,在模具与坯料表面上的摩擦力可以认为是粘性摩擦力和表面粗糙引起的变形力。因此摩擦力方程一般表示如下:
T = Ta + Td (1)
在这里,T 是总摩擦力,Ta是粘性摩擦力,Td是表面粗糙的引起的变形力
粘性摩擦力部分是由于不同体的表面分子力引起,取决于材料的物理性质。变形力是使粗糙表面变形,取决于表面的粗糙度,材料的流动应力和接触压力和滑动速度。接触压力比较高的情况下,变形力Td是主要的,而当接触压力低的情况下,粘性摩擦力影响更大。
在实际情况下,对于不同的接触压力,我们需要定义不同的摩擦机理[6]。特别是对于铝合金挤压,我们可以很清楚的区分不同摩擦类型的区域。第一个区域包括挤压筒的内表面,分流孔和焊合室。这些地方接触压力很大,变形摩擦因素最大。由于粘性摩擦的影响,总的摩擦力可以大于剪切流动应力。这也意味着金属在模具内表面为粘性接触,材料内部发生强烈的剪切变形产生滑动。
第二个区域是工作带区域,使用QForm-Extrusion模块在数据准备向导中的工作带编辑器中可以看到,显示为如图2的参数化表格形式。我们把这个区域的三个区依次使用不同的摩擦模型:
1.粘性区域,变形很大位于工作带的入口处,当工作带为阻碍角时,这个区域可能延长。
2.滑动区域,变形减小。
3.材料脱离模具区域,有很小的接触应力。

(a) (b)
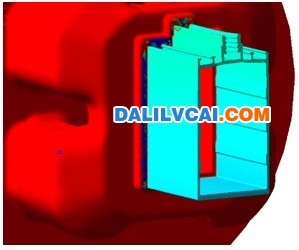
(c)
图2 接触区域参数化显示在工作带编辑器中(a);工作带草图(b);
QForm-Extrusion模块计算型材挤出结果(c)
QForm-Extrusion模块计算型材挤出结果(c)
这些区域的相对尺寸取决于多个参数,可能对着型材的周围是变化的。工作带分割成多个区域,S. Abtahi [7]用实验验证了他们之间的联系。因此对于型材周围的每一个点来说下面的参数都可能影响区域的长度:
有效的的阻碍角
实际的型材厚度
型材的流动速度
有效的阻碍角是阻碍角的代数和,因为它是在模具和工作带表面倾角上加工与工具变形有关。型材厚度与模具变形有关。因此为了得到材料流动的精确结果,我们要考虑有效阻碍角和实际型材厚度的影响。只有与模具变形进行耦合计算,才能得到材料流动问题的结果。QForm-Extrusion中摩擦模型包括模具组合体弹性变形对有效角度和型材厚度的影响[6]。
对这样复杂的模型无法精确表达,因此认为是一种半经验算法。首先,模拟材料流动求解模具变形问题。然后计算有效的阻碍角和工作带周围每一个点的实际型材厚度和重新计算材料流动。在所有区域上对于工作带上每一个点我们都要计算速度,接触压力和流动应力决定的摩擦力。
二 材料流动计算和模型验证
上面描述的数学模型已经经过了实验室和实际工业案例的验证。最近的一个实验测试是在2011年ICEB大会上,我们可以在[8]中看到。组织方展示的数据和实验结果可以参照文献[5]。型材的轮廓和模具见图1,现在我们讨论材料流动预测的结果。
从模拟结果我们可以看到型材1比型材2的流动速度快(见图3a和b)。同时模拟结果显示对于不同的焊合室和模具其它部分的设计,型材1(左边型材)有向下弯曲的趋势,而型材2比1要直。当会议上实验数据公开后,材料流动结果显示了与模拟相同的趋势。型材的前端见图3中的c和d。另外我们观察到在型材相对速度,挤出载荷,型材温度和模具变形方面实验结果与QForm-Extrusion模块计算的结果也是非常一致,可以参照[5]和[8]。
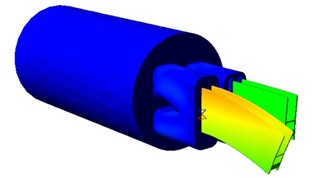
(a)
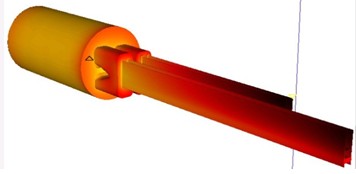
(b)
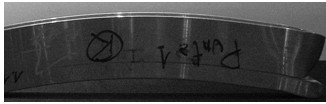
(c)
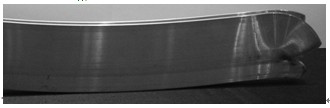
(d)
图3 铝型材流动预测
铝型材自由流动时速度分布和变形显示(a);铝型材被牵引时的计算结果(b);
铝型材1向下弯曲的照片(c);铝型材2挤出时的照片(d)
铝型材1向下弯曲的照片(c);铝型材2挤出时的照片(d)
三 耦合模具计算和工业应用
QForm-Extrusion模块目前有多个用户使用,对于多种复杂和不同挤压比的实心和空心的型材都进行了大量的工业验证。从中发现模拟最复杂的薄壁件时,考虑模具组合体特别是工作带位置的模芯和模套的弹性变形是非常重要的。也就是说材料流动和模具变形应该耦合起来进行分析。下面是不耦合和耦合变形的型材流动结果显示(见图4)
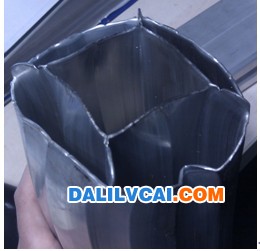
(a)
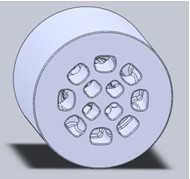
(b)
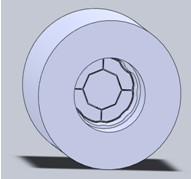
(c)
图4 实际型材前端形状(a);导流板(b);下模(c)
型材挤压耦合模拟分析时,我们认为模具组合体可能包含如下的部分(图5)
型材挤压耦合模拟分析时,我们认为模具组合体可能包含如下的部分(图5)
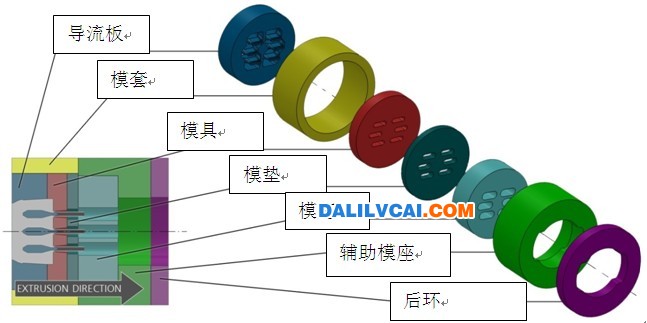
图5 典型模具组合体组件
上面的模具组合体包含了除挤压筒外的所有部件,而挤压筒采用在坯料侧面施加边界条件的方法添加。图6显示了用于耦合计算双管型材流动的挤压域与模具组合体。
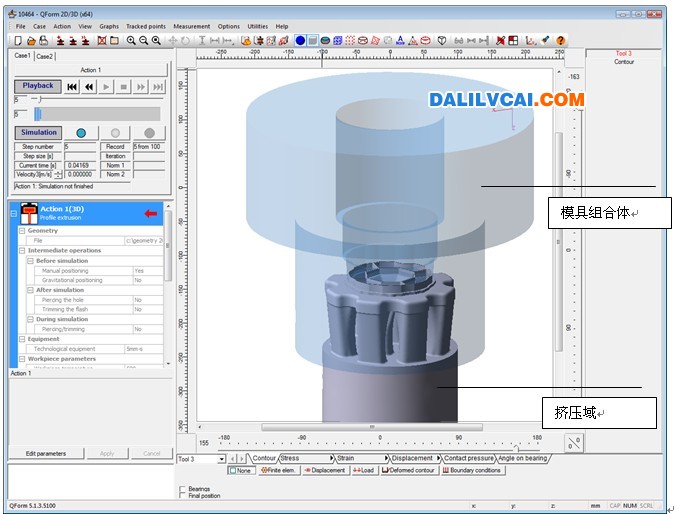
图6 用于耦合计算双管型材流动的挤压域与模具组合体
在实际挤压过程中我们不能准确型材轮廓的速度分布。因此结果对比的方式只能是比较实际和模拟的型材前端的形状。型材前端的形状清晰的显示了型材不同位置的速度分布。这些工业研究有很多目标:
对把工业系统中的几何模型转化为模拟需要的数据的方法进行测试和改进。
评估模拟的准确性。
分析测试结果开发更好的数学模型和软件程序。
测试结果显示考虑耦合分析模具组合体的变形对于塑性材料流动非常重要。第一次计算是认为模具是刚体的情况下,模拟材料流动。结果显示在双管型材的中间部分流动速度小于外部管(图7a)。
对于相同的模型,在考虑模具弹性变形的时候,材料流动结果显示了完全相反的结果(见图7b),内部管的流动速度要大于外部管,并且形状与实际形状(图7c)相一致。
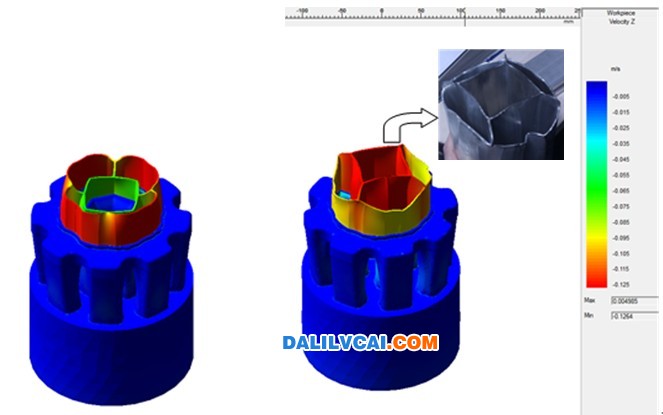
(a) (b) (c)
图7 在考虑模具为刚体的情况下,双管型材尖端形状模拟结果(a);
耦合分析模具变形的情况下,模拟结果(b);实际的挤出形状(c)
图7中的结果证明了对于精确分析材料流动来讲需要耦合模拟模具变形的假设。这种方法也为在挤压过程中预测型材偏离角度和偏离集合尺寸。
耦合分析模具变形的情况下,模拟结果(b);实际的挤出形状(c)
图7中的结果证明了对于精确分析材料流动来讲需要耦合模拟模具变形的假设。这种方法也为在挤压过程中预测型材偏离角度和偏离集合尺寸。
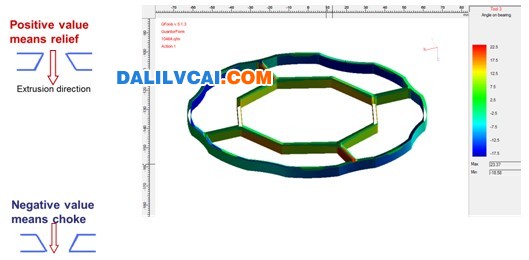
图8 工作带的倾斜方向取决于模具的弹性变形
工作带倾角的变化可以解释模拟结果与实际相一致。图8显示了工作带开始是直的,可能变为促流角或者阻碍角明显的影响材料的流动。很明显模具工作带倾角为阻碍角的材料流动速度明显要慢于模具为刚性的情况。相反地,倾角为促流角时材料流动要更快。这些就引起了如图7的材料的流动变化。
四 预测挤压的焊合情况
除了型材形状,还有其他一些因素与材料流动有关。实际型材挤压中我们要避免三种缺陷:表面质量、产品的组织性能,空心型材焊合线位置不合适或新旧材料的焊合过度延伸过长。通过下面的案例说明,所有这些现象都可以准确模拟和修正或者至少减少缺陷。
QForm-Extrusion模块可以跟踪材料流动的过程,从挤压筒内到导流孔到最终型材。这就可以有效地找到材料流动路径包括从坯料表面到产品和焊合线位置。首先,我们用2011年意大利公开测试案例来说明上面提到的软件功能。测试的组织者提供了两种型材通过截面腐蚀找到纵向焊合线的位置。截面图显示在图9c和d。由于导流槽内的材料流动不一样,造成焊合线位置不一致,很明显型材2的焊合线位置在空心中线下方,而型材1的焊合线位置在空心底部。
在模拟软件中追踪材料流经导流槽的过程,在图9b中用不同的颜色高亮显示,然后显示这些材料的焊合后型材截面的分布结果。通过模拟与实际相对比,我们发现模拟可以精确预测焊合线的位置。在型材2中接近轴线,在型材1中接近空心的底部。
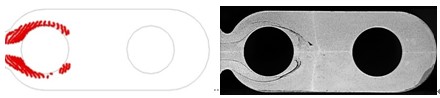
(a) (b) (c) (d)
图9 焊合线位置模拟结果(a);在导流槽内的轮廓标记(b);
比较型材1的焊合线位置(c);比较型材2的焊合线位置(d)
比较型材1的焊合线位置(c);比较型材2的焊合线位置(d)
对于型材来说焊合线位置是很重要的。同时由于型材的形状复杂多样,用经验又很难预测焊合线的位置。焊合线位置不合适有可能引起结构损坏。为了精确预测复杂工业型材焊合线的位置,进行了很多的实验验证。下图10是其中之一。从下面的对比分析我们可以很清楚的看到模拟结果非常准确,我们可以在模具设计阶段避免由于焊合线位置不合适引起的问题。

(a)
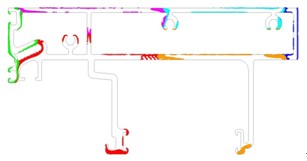
(b)
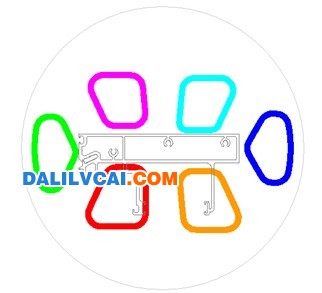
(c)
图10 实验(a);模拟结果(b);导流槽的形状轮廓(c)
在连续挤出工艺中会遇到材料横向焊合的问题,在焊合线的位置可能包含一些氧化物或其它杂质造成焊合线位置材料的机械性能较差。因此这部分材料一般都从最终产品中丢弃。在工业实际中经常很难找到他们的位置且要花费很多时间进行微观组织分析。
对于横向焊缝的精确度可以通过瑞典SAPA公司的工业案例来验证,为了显示型材中横向焊缝的分布,指定一个结合面。这个面开始分隔开新旧材料。图11显示了新旧材料在挤压过程中的流动。
对于横向焊缝的精确度可以通过瑞典SAPA公司的工业案例来验证,为了显示型材中横向焊缝的分布,指定一个结合面。这个面开始分隔开新旧材料。图11显示了新旧材料在挤压过程中的流动。
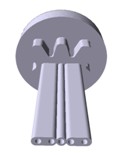
(a)
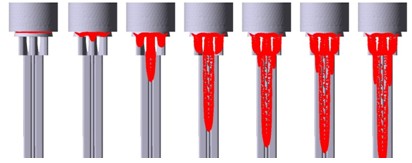
(b)
图11 铝型材轮廓总体视图(a);新旧铝材料的流动(b).
图12显示了关于焊合面的更多分析,其中包括模拟结果和实验结果。截面显示新材料在挤压过程中如何扩展。比较发现模拟结果与实际非常一致。
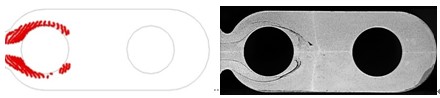
(a)
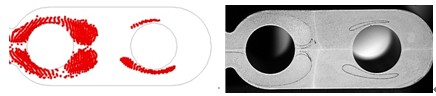
(b)
图12 新材料显示使用红色轮廓标记,左边为模拟结果,右边为腐蚀截面的照片(a、b).
五 结论
1.QForm-Extrusion型材挤压模块提供了拉格朗日-欧拉混合方法,在模拟域中对模拟网格进行特殊的优化。
2.铝型材挤压模型需要考虑更多复杂的摩擦规则包括粘性摩擦等。
3.软件对于材料流动,实际型材形状和其它工艺参数的模拟结果与实际大量实验对比,得到了很好的一致性。
4.材料流动的精确预测还可以分析型材的纵向焊合线和横向的焊缝,对于实际产品质量来说这是非常重要的,需要在模具设计阶段完成优化。
5.数值模拟软件对于薄壁型材的工业应用和研究都是一个理想的工具。