关键词:天然气熔铝炉;蜂窝体;蓄热式燃烧;设计模型;计算公式
1 前言
熔铝炉是铝加工过程的主要熔炼设备,其作用是熔化铝料,使其质量均匀并达到一定化学成分要求,为铸造及其他加工过程提供合格的铝液。熔铝炉的能耗约占铝加工厂总能耗的40%以上[1]。因此,提高熔铝炉的燃烧技术水平对降低铝加工能耗、提高企业经济效益及实现国家的节能减排战略均具有重大意义。
目前,熔铝炉基本都采用陶瓷球蓄热式燃烧系统,虽然节能效果良好,但是体积大、效率低,还有继续优化的必要。
蜂窝体是近年来广为采用的蓄热材料,如图1所示。
蜂窝状蓄热体多采用堇青石质或莫来石质做原料[2]。目前广泛使用的蜂窝蓄热体的尺寸多为 150×150mm,蜂窝单元间距为 1~3mm,壁厚 0.5~1.0mm,比表面积大(为小球的2~4倍),蓄热放热快,有效流通面积大(球的2倍),阻力损失小(球的1/2),是远优于蓄热球的新型蓄热材料。
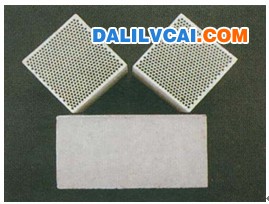
图1 蜂窝体蓄热材料
目前,蜂窝体做为蓄热材料用于天然气熔铝炉还鲜见报道。文献[3]建立了蜂窝体蓄热室流动与换热过程的三维非稳态数学模型,运用计算流体力学(CFD)软件对陶瓷蜂窝体的工作过程进行了数值模拟,得到了加热期末尾时刻与冷却期末尾时刻蜂窝体内气体的速度、温度、密度和压力分布及一个换向周期内气体出口温度、蜂窝体纵向温度和气体纵向温度的瞬时变化关系。但是计算方法非常复杂,难以被工程设计人员采用。因此,本文致力于首先建立适用于熔铝炉的蜂窝体蓄热室模型,然后给出简洁的经验计算公式,以便为工程设计人员提供理论指导。
2 蜂窝体蓄热室设计计算
以最常见的18吨天然气熔铝炉为研究对象。该炉由炉体、两个蜂窝体蓄热室、燃料烧嘴组成。燃料以天然气为例,相关的原始数据及有关参数如下所示:
烧嘴能力:250m3/h,烧嘴前天然气温度:20℃,烧嘴前空气温度:900℃,炉膛温度:1200℃,排烟温度:150度。
蜂窝体蓄热室设计根据逆流换热器的计算方法,以烟气和空气在周期内的平均温度为特性温度,求取综合热交换系数,设计蓄热室的大小。详细步骤如下:
(1)一个换向周期内预热空气所需要的热量Qk的计算:
预热空气量(可近似按12倍燃气量计算):
Vk = 250×12 = 3000 Nm3/h = 3879 kg/h
设进入蓄热室空气温度为t1k=20度,排出蓄热室烟气温度为t2k=800度
分别查出t1k= 20℃和 t2k=800℃时空气的比热容:
c1k=1.005kJ/(kg?℃),c2k=1.156kJ/(kg?℃)
换向时间选为:Zk=40s=0.011h
则每周期内预热空气需要的热量为:
Qk = Vk×(c2×t2k-c1×t1k)×Zk
= 3879×(1.156×800-1.005×20)×0.011
= 38603 kJ
= 3879×(1.156×800-1.005×20)×0.011
= 38603 kJ
(2)蓄热室温度效率e的计算
进入蓄热室烟气量(可近似按1.1倍预热空气量计算):
Vy = 3000×1.1= 3300 Nm3/h = 4267 kg/h
设进入蓄热室烟气温度为t2y=1000度,排出蓄热室烟气温度为t1y=200度,分别查出t1y= 200℃和 t2y=1000℃时烟气的比热容:
c1y=1.29kJ/(kg?℃),c2y=1.1kJ/(kg?℃)
烟气换向时间:Zy =40s=0.011h,则每周期内冷却烟气需要的热量为:
Qy = Vy×(c2y×t2y-c1y×t1y)×Zy
= 4267×(1.29×1000-1.1×200)×0.011
= 50222kJ
= 4267×(1.29×1000-1.1×200)×0.011
= 50222kJ
蓄热室温度效率:
e=Qk/Qy=38603÷50222=77%,满足要求。
(3)对数平均温差 Δt的计算[4]
流动方式为逆流方式,则修正系数Φ=1,蓄热室的对数平均温差为:
Δt1 = 1000 – 900 =100度

= 70W/(m2?K)
= 94.6W/(m2?K)
Δt2 = 200 – 200 =180度
Δt = (Δt2-Δt1)÷ln(Δt2Δt1/)=136度
(4)计算蓄热室内空气和烟气速度
假设空气/烟气从方孔周期性流过,流体与四周陶瓷蓄热壁连续换热。假设流体流过蓄热体时在各小孔的流速分布均匀。由于蜂窝陶瓷蓄热体孔径和壁厚较小,孔分布较均匀,且切换周期较短,故忽略内部径向热阻,壁内部径向温差视为均匀。
本设计选用的蜂窝体为150×150×150mm,孔为3×3mm,蜂窝体的尺寸得有效截面积(即孔隙率)为:
a=(3×3)÷(3.8×3.8) = 0.623
空气的定性温度取:(20+800)/2=410 ℃
烟气的定性温度取:(1000+200)/2=600 ℃
在蓄热室内每层放16个蜂窝体,因此蓄热室的截面积为600×600mm2 ,即为0.6×0.6m2。那么可得:
蓄热室内空截面空气流速:Uk1 = 3000÷3600÷0.6÷0.6 = 2.31 Nm/s
蓄热室内空截面烟气流速:Uy1 = 1.1×Uk1 = 2.55 Nm/s
蓄热室内空气流速:Uk2 = Uk1÷? = 2.31÷0.623 = 3.71 Nm/s
蓄热室内烟气流速:Uy2 = 1.1×Uy1 = 4.1 Nm/s
在定性温度下空气速度为:Wk = 3.71×(1+410/273)= 9.3 m/s
在定性温度下烟气速度为:Wy = 4.1×(1+600/273)= 13.1 m/s
(5)计算蓄热室传热系数K
空气对流换热系数为[5]:

= 70W/(m2?K)
烟气对流换热系数为[6]:

此外,为进一步深入计算,引入以下参数,
蜂窝体壁厚S=0.4mm=0.0004m
陶瓷的导热系数:λx=2.83w/(m.K)
切换时间,Zk=Zy=40s=0.011h
带入蓄热室综合传热系数的计算公式[7]:(考虑到辐射换热量很小,可以近似认为ak=akd,ay=ayd
得出:K = 40.2 W/m2.k
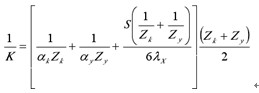
(6)蓄热室尺寸计算
蓄热室单位时间传热量为:
q = Qk÷Zk = 38603÷40 = 965kw
蓄热室的传热表面积为:
F = q÷(k×Δt)= 177m2
蜂窝体的壁厚为0.8mm,尺寸为3×3mm2,
其比表面积为:
S0=(4×3)÷3.8÷3.8×1000= 831 m2/m3
一个蓄热室的蓄热体体积V为:
V = 177÷831 = 0.213m3
蓄热室的水平截面积为即为0.6×0.6m2。那么蓄热室高度为:
L=0.213÷0.6÷0.6=0.592m
取高度为600mm,共四层蜂窝体。
即选用蜂窝体砖4×4×4 = 64块。
(7)蓄热室的阻力计算
根据埃根方程计算蓄热室压力损失[8]:

对于此蓄热室,高度L=0.6m;
比表面积s0 = 831 m2/m3;
孔隙率a= (3×3)÷(3.8×3.8) = 0.623
式中U0为蓄热室空气的空床速度,
= 2.31×(1+410/273)= 5.8 m/s
μ 、ρ 为气体定性温度 410℃下的物性参数,μ=3.31×10-5 Pa?s
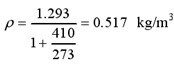
以上参数带入埃根方程后得到蓄热室阻力损失为: 4272Pa,保守取5000Pa。
3 实际应用效果
我公司于2013年采用蜂窝体蓄热式燃烧技术对一台18吨熔铝炉进行了节能改造(采用本文的设计方法),验收结果如下:
表1 验收数据表
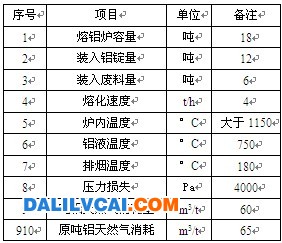
由表1不难看出,改造后,节能效果显著。吨铝天然气消耗由原来的65m3,下降到60m3,下降达到8%。目前,天然气价格为4.5元/m3,吨铝可节省天然气费用22元;按18吨熔铝炉年产铝棒1.5万吨计算,每年可节省天然气费用33万元。改造费用大约16万元,投资回收只有6个月左右,完全可以大力推广。
5 结论
本文对18吨天然气熔铝炉蜂窝体蓄热室的设计进行了详细阐述,给出了相应的计算公式,并通过实际改造工程的节能检测效果验证了计算方法的准确性。根据上文的论述,不难得出以下结论:
(1)蜂窝体蓄热式燃烧技术在18吨天然气熔铝炉上的改造是非常成功的。
(2)可节省8%的天然气燃料,按年产15000 t铝计算,每年可节省天然气费用33万元。
(3)该技术投资回收期短,值得在同行业中大力推广。