1 引言
蒸发器翅片是空调散热器的重要零件(如图1所示),材料为0.115mm厚的铝箔,年产量达数亿件,因此必须采用高速级进模生产。
我公司原采用引进意大利GBS高速冲模生产蒸发器翅片。为降低成本,公司决定自行设计制造KF25G空调蒸发器翅片模。此翅片模工作时要求60列同时送出,工作频率180~200次/min,出片稳定率要求大于95%,关键易损件寿命大于3000万次。
2 工艺难点分析
蒸发器翅片级进模共7个子模,14个工序,43个工位,兼容了多步拉伸、切口、压型、冲孔翻边、卷边、冲槽、切断等多种功能。设计制造难点主要体现在以下4个方面:
(1)精度高。制件材料厚度0.115mm,单边冲裁间隙小于0.004mm,模块定位精度0.003mm,整体制造精度IT4~IT5。
(2)冲次高。工作冲次高达180~200次/min,对牵引装置、顶料、卸料及活动部件的灵敏度、运动灵活度等都有十分严格的要求,以保证高速冲压下动作的可靠性。
(3)互换性。所有工作部分的模块、弹性销、凸、凹模等主要配件要求能够互换。
(4)尺寸大。除去模具首尾的进料装置、出料装置、吹风装置等,仅模具核心本体部分尺寸就达1790mm X 1100mm X 287mm。
(1)总体结构。KF25G蒸发器翅片模相对于国外进口模具的一项重要改进,就是能够与冷凝器翅片模以及KF25W/E蒸发器翅片模通用安装,改变了原GBS进口模具1台冲床、一副模架只能适应一种产品的现状,极大方便了生产需要。改进的关键在于总体设计时应综合考虑3种模具的步距、子模布局、机床配套位置等因素,利用CAD的优势,可方便地调整布局,进行各种方案的比较。实践证明,实现3类模具的通用安装,完全可行。
蒸发器翅片模结构如图2所示,其工作过程为:成卷铝箔进进料机构送入子模1,经4步拉伸完成翻边孔预成形,子模2切口、压形完成散热百叶窗冲压,子模3完成冲预孔、翻边、卷边,子模4完成冲三角孔,再送入子模5进行纵向60列冲槽分离,子模6为步进牵引机构,最后进入子模7横向切断,完成整个冲制过程。
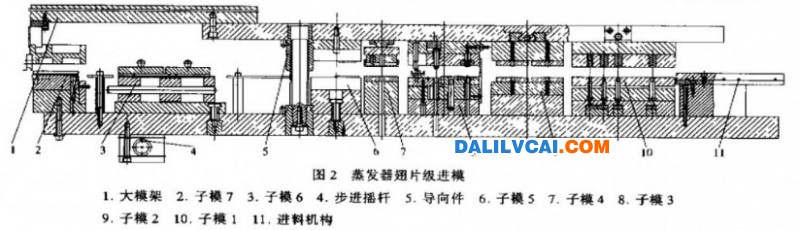
(2)子模1拉伸工序。因国产铝箔与进口铝箔性能上存在一定的差异,原GBS进口模具不能适用于国产铝箔,冲压时大面积拉裂。经试验,关键在于拉伸次数太少,改为4步拉伸后完全可以适应国产铝箔的拉伸。4步拉伸工序如图3所示,第1、2步之间的空步是出于模具结构上的考虑,图中各项尺寸均经多次计算与试验得出,其中内外拉伸圆角很重要,各圆角尺寸处理不当极易产生拉裂。子模1设计成4步拉伸,必须将其它子模的步距分布进行相应调整,原则上应保证冲床上的原漏料位、步进摇杆等附件位置不改变。
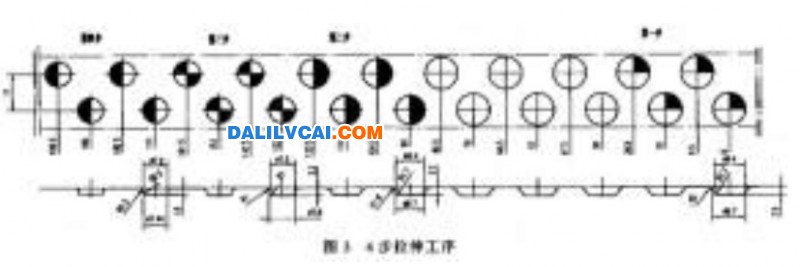
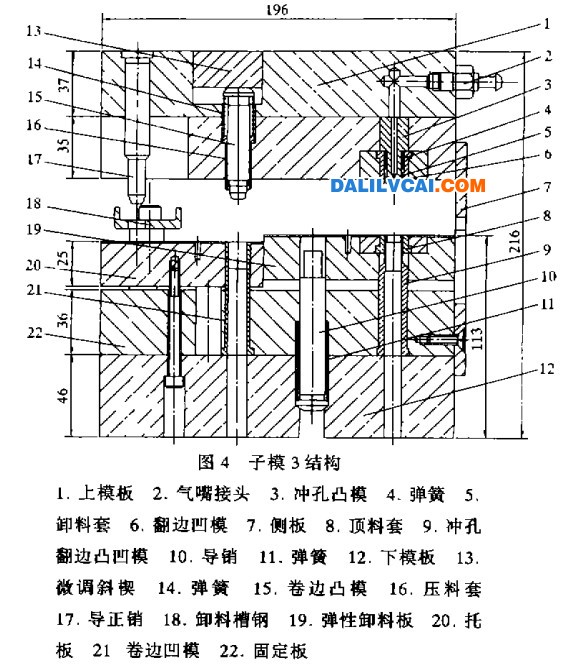
(4)子模6为步进机构。采用弹性指状销拉料结构,其中滑动底板采用的材料应具有一定的强度,采用轻质进口硬铝合金板ZL102。
(5)子模5冲槽工序。子模5在使用中最突出的问题是冲槽凸模的调整,应调整频繁,必须便于操作。设计中采用了可调整式压条结构,每个冲槽凸模均有一条独立的压条来调整,保证了以最少的停机时间调整冲槽凸模。
4 主要零部件制造工艺
翅片模加工制造大量地采用了数控加工,编程数据量庞大。因此,一体化的CAD/CAM系统是必需的技术手段。以下就加工中的几个难点作一简介。
(1) 大模架的加工。大模架的精度是保证整副翅片模精度的基础。重点是下模板,外形尺寸为1790mm X 1100mm X 63mm,材料为45钢,上、下平面平行度要求小于0.02mm,高精度定位孔36个,位置度允许误差小于0.005mm,导柱安装孔位置度误差小于0.002mm。大模板加工主要工序全部采用龙门加工中心加工,共分2道粗加工和3道精加工完成。工序之间全部穿插人工时效处理,消除内部应力。导柱孔位置度已超过机床能达到的精度,工艺上采用了上、下模板合镗的方式,以保证导向精度。
(2)切口模块。切口模块为子模2中的重要零件,共60件,切口间距1.3mm,每件模块切口28条,刃口精度0.002mm,定位孔位置误差小于0.003mm,孔径误差小于0.003mm,淬火硬度58~62HRC,材料采用奥地利产K190钢。模块粗加工后,进行真空热处理。以光学曲线磨分2道工序加工刃口,用电火花电蚀漏料台阶,用高精度穆尔坐标磨加工定位孔,最后用光学投影仪、三坐标测量机检测精度。
(3)冲槽凸模。上下冲槽凸模为子模5的重要零件,共117件。凸模厚度误差小于0.002mm,其加工工艺的关键在于热处理后的精磨工序,先在普通平磨上精磨至0.01~0.015mm余量时,转至PFG精密小平磨上精密修磨,再用三坐标测量机检验。
(4)上下固定板。子模5上的冲槽凸模上下固定板,包括117条方形装夹槽,槽宽精度允许误差小于0.002mm,采用慢走丝切割加工。考虑到以上加工精度靠设备精度难以保证,设计时必须考虑其工艺性,采用上、下固定板在同一基准下合在一起同时线切割,这是此件加工的关键。
(5)子模5的上模座。此上模座为翅片模中工艺性最差的零件,材料45钢,调质处理23~28HRC,定位孔位置允许误差小于0.002mm,模座上有59条6.5mm X 12mm(深)的开槽口。其加工的关键在于调质后的各道粗加工之间均要进行人工时效处理,严格控制内应力,保证精加工后不能变形。特别是开口槽,加工后使应力分布状态变得十分复杂,解决的办法只能是从粗加工开始就控制内部应力,最后用高精度数控设备加工定位孔。
叙述了空调蒸发器翅片级进模的设计要点,并对加工过程中的难点进行了分析,介绍了解决的途径和对策。
模具装配完成后,上机试模实测调整各项技术指标是最后关键的工序。经调试,KF25G翅片模各项指标如下:工作冲次大于192次/min,闭合高度与GBS原模之差0.042mm,步距38+/-0.08mm,出片稳定率大于98%,双桥完好率100%,各项技术指标均达到设计要求。