铝电解槽,无论是新建系列的还是大修的,在投入生产运行前,都必须进行焙烧,然后启动。对于电解生产来说,大型预焙铝电解槽的焙烧启动是一个极其重要的环节,它不仅关系到电解槽能否顺利投产,而且影响正常生产、技术经济指标及槽寿命,历来为国内外各厂家所重视。随着大型预焙铝电解槽的发展,其自身的工艺也随之研究开发,不断创新并加以应用。特别是大型槽的焙烧启动工艺,对于新系列的电解槽更为重要,也是铝行业不断研究的热点之
一。近年来,随着大型预焙阳极电解槽在我国的迅猛发展,各铝电解厂家纷纷对电解槽焙烧启动的方法进行积极探索。本文通过剖析生产现场焙烧启动技术发现存在的问题,并在此基础上提出改进措施。我公司230kA电解槽自2004年投产以来,通过对焦粒焙烧启动的技术的不断摸索和完善,使得电解槽槽龄平均达到了1 800天左右,1 78台电解槽焙烧启动过程没有出现脱极、早期破损和漏炉停槽现象,应用效果较好。
一。近年来,随着大型预焙阳极电解槽在我国的迅猛发展,各铝电解厂家纷纷对电解槽焙烧启动的方法进行积极探索。本文通过剖析生产现场焙烧启动技术发现存在的问题,并在此基础上提出改进措施。我公司230kA电解槽自2004年投产以来,通过对焦粒焙烧启动的技术的不断摸索和完善,使得电解槽槽龄平均达到了1 800天左右,1 78台电解槽焙烧启动过程没有出现脱极、早期破损和漏炉停槽现象,应用效果较好。
一、焙烧启动技术要点
(一)铺焦粒
为了使阳极底掌与石墨粉煅后焦混合料有良好的接触以保证电流分布均匀,提高焙烧质量,选择煅后焦颗粒2~4毫米颗粒比例占80%左右,以增加与阳极炭块的接触面积,千万不要小看这第一步,因为焦粒粒度直接决定送电后的焙烧效果和阳极电流分布情况。铺设焦粒前,将电解槽阴极炭块表面彻底吹扫干净后,下降大母线使之标尺刻度放置在3 50刻度,焦粒铺设和阳极的安装自A8、B8开始连续铺设,至Al、Bl结束。使用专用刮板尺将阳极下焦粒刮平,厚度2厘米左右,每一块阳极下焦粒厚度不能出现大的差异,否则会出现局部温度不均匀的现象,影响到焙烧效果。单台电解槽铺设焦粒总量在450千克左右。
(二)选极、挂极
我公司双阳极要求挂极必须确保阳极底掌与焦粒接触面积达到98%。压实率达到95%以上。安装阳极前,应检查阳极炭块有无质量缺陷,铝导杆是否垂直,磷铁环是否饱满、松动,有无夹渣和裂纹,阳极底掌是否平整。然后将合格的阳极炭块组用天车吊起,对准阳极卡具位置,指定专人用手扶住铝导杆,使其紧靠阳极母线,平稳地放在焦粒层上。检查阳极四周和四角是否压在焦粒上,不允许出现悬空和接触不良的现象。由专人用手旋紧小盒卡具螺栓,接好软连接装置。操作重点是要首先保证阳极底掌与焦粒充分接触,同时阳极导杆应尽可能与水平大母线形成面接触,以减少拧紧卡具后阳极的位移,从而减少阳极导电不均的程度,可以防止局部阳极电流过大而出现的钢爪发红、脱落等异常现象。
(三)安装软连接
采用软连接的优点是可以保证阳极与焦粒始终良好的接触,能够避免因电流不均造成的局部过热现象。还能吸收焙烧过程中相关部位热变形的影响。安装前软连接与阳极导杆及阳极大母线接触各部位应当清扫、打磨干净,各部位螺栓必须紧固,以防止接触不良发生打火现象。大屯铝业公司230kA预焙阳极电解槽采用软连接器如图1。
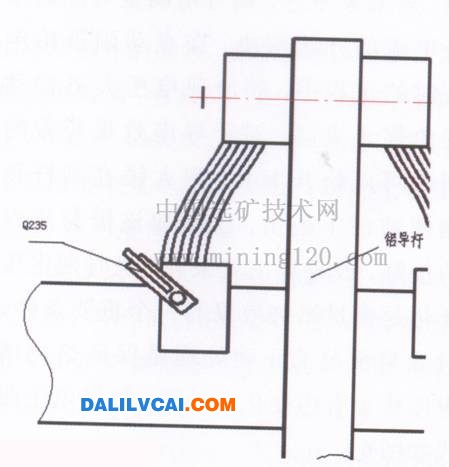
图1 软连接器
全槽阳极挂完后安装软连接,小盒夹具可由专人用手稍微带紧,而不必使用工器具,让其呈自由升降状态。
(四)装炉
焦粒铺设、挂极完毕后,各极间缝隙用牛皮纸填充,防止钙和碱进入阳极中间。在阳极四周的槽膛处紧贴阳极底掌至人造伸腿之间铺2~3厘米冰晶石,然后在“人造伸腿”上均匀铺1.5吨氟化钙。此后在氟化钙上再装入一层厚约10厘米冰晶石,再在其上装纯碱1.2吨。再盖冰晶石至满槽,要求阳极组上表面以上15厘米,但不能盖住钢爪。加入槽内的冰晶石,要求阳极上表面较高,边部稍低,中缝填冰晶石以加强保温。
(五)分流片安装与拆除
选择分流片作为分流器,分流片为钢制从阳极钢梁焊接在对应的阴极钢棒头。应当说明的是,分流器的分流量不是固定不变的,在通电初期槽电压较高,分流器本身温度低,电阻率低因而分流较多。随着焙烧的进行,槽温升高,槽体电阻下降分流器温度升高,其电阻率亦升高,此时焙烧槽的电流会自动提升。江苏大屯铝业有限公司分流片形状如图2所示,两头采用钢板,中间为软钢带。这样就能保证了分流片的强度,分流量的大小经过计算初期为50%~60%左右。

图2 分流片示意图
当通电12小时后,可陆续拆除分流片,如电压低于3.0伏,一般可按先角部后中间的顺序,从Al、Bl、A8、B8处先行拆除。当时间超过24小时,且槽电压低于2.7伏时可陆续拆除其它分流片。拆除分流片时,每次的槽电压升高值不得超过1.0伏。若超过此范围应停止拆卸,并检查阳极电流分布,待电压稳定后再继续卸。分流片全部拆除后,槽电压不得超过4.0伏。温度偏低,电流较小的阳极优先拆除分流片。拆除分流片的片数和增加分流片视情况决定。拆除分流片后,应抓紧时机做好调整工作,使两极电流分布调整到最佳状态,使电解槽安全平稳地进入伞电流焙烧阶段。
1、紧阳极卡具和拆除软连接
2、启动前槽内电解质和电解质温度要求
(八)启动电解槽
(六)通电焙烧
完成短路口操作并检查确认无误后,通知整流所通电。送电过程中,如冲击电压超过5伏,则应放慢升电流速度,当升满全电流时,冲击电压不得超过5.5伏。如图3所示。
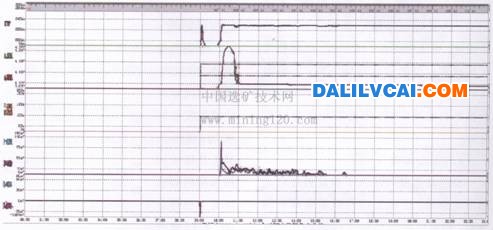
图3 电解槽送电历史曲线
(七)启槽准备
1、紧阳极卡具和拆除软连接
全电流送电120小时后,槽电压降至2.2~2.3伏,安排专人上紧小盒卡具两次,防止漏拧或未拧紧,并经常检查电压上升情况,发现问题及时进行调整。拧紧卡具会造成阳极底掌面产生一定的位移,引发局部阳极底掌与导电介质接触不良,引起阳极导电均匀程度变差。因而为了尽量使整个焙烧过程电流分布均匀,拧紧卡具的时间应在启动前的2~4小时内进行,而且是分次进行拧紧,尽量减少阳极移动量,提高焙烧质量。如果过早地拧紧卡具,阳极受热应力的作用要向上隆起,如果阳极不能向上自由移动,那么只有挤压上部机构变形或向阴极内衬薄弱位置传递,势必会造成阴极早期破损。拧紧卡具后,便可拆除软连接,实际拆除软连接后,槽电压一般上升值不大于0.3伏。
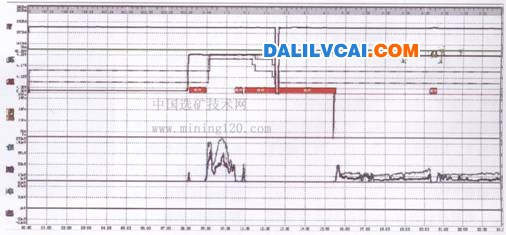
图4 电解槽启动历史曲线
2、启动前槽内电解质和电解质温度要求
测量电解槽的中缝电解质高度达到30厘米以上,温度高于850℃,槽四周局部开始熔化,烟道及出铝端温度在700℃以上。并再次检查供料装置、槽控机是否良好,槽控机上和短路口用遮挡物保护,槽上软管及接头用石棉布进行保护,防止高温烘烤。
(八)启动电解槽
1、干法启动
前20台槽采用干法启动,后续槽视情况可采用湿法启动。
随着物料的溶化,当中缝电解质高度达到30厘米以上时,可将电压提升到10~12伏,待物料全部熔化,电解质高度达到40厘米,槽温在970℃时,用大钩清理阳极底掌,及时捞出炭渣。手动AEB,待氧化铝溶解后再加入1.2吨的碳酸钠,电压保持在7伏左右。用参数变更单通知上位机开通自动下料,下料间隔设定为200秒,开通效应报警并取消极距控制和浓度控制。安排取电解质试样分析。
(九)灌铝
(注:前半期电解槽灌铝用的铝水可采用加铝锭的方式,随后电解槽可从前期启动槽内抽取。)
二、焙烧启动过程中异常情况处理及监控
(一)焙烧期间
2、湿法启动
将活动溜槽和注入平台放到待启动槽的出铝端。出铝工在得到灌电解质指令后,用真空抬包从预先选定的几个电解槽中抽取高温电解质。天车将电解质吊到待启动槽旁,边灌电解质边抬阳极,电压保持在9伏左右。灌完电解质后,再视槽内电解质高度,决定是否继续添加冰晶石或混合料进行熔化。当物料全部熔化,电解质高度达到40厘米、槽温达到980℃以上时,用大钩清理阳极底掌,及时捞出炭渣。以下同干法启动程序。
(九)灌铝
电解槽启动后,尽量在24小时以后灌铝,特殊情况可根据槽电压、槽温和电解质情况在启动12小时后可灌铝。否则,电解槽长时间在高温状态下有可能发生“含炭”、电压摆等现象,如图5所示。
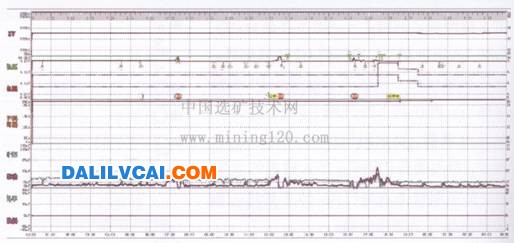
图5 灌铝历史曲线
24小时后分两次灌入12吨左右铝水,将活动溜槽平台放到灌铝槽子的出铝端,天车将抬包吊到指定位置,出铝工通过溜槽将铝水灌入槽内,与此同时,有专人在槽控机旁抬阳极,边灌边抬阳极。灌铝前槽沿板上铺设氧化铝粉,以防止飞溅铝水,灌铝时应注意用溜槽缓慢注入,避免铝水流到钢爪上。灌铝结束,电压保持持在5.3~5.5伏。待槽子四周围的电解质表面结壳后,加足极上保温料,整好形。盖好槽盖板,整理现场。次日早取铝试样送化验室分析。灌铝后第三天可考虑出铝作业,出铝量按铝水平情况确定。
(注:前半期电解槽灌铝用的铝水可采用加铝锭的方式,随后电解槽可从前期启动槽内抽取。)
二、焙烧启动过程中异常情况处理及监控
(一)焙烧期间
如因电流分布不均而导致阳极钢爪过热、发红时,可扒开相应极上保温料,用专制风管对住过热发红处吹风,或用铁制工具搭接到相邻槽的阳极钢梁上进行分流。如15分钟后效果仍不明显,可松开夹具,对该组阳极实施断电,一小时后再恢复送电(注意:采取断电措施的阳极组数不能超过3组)。如因铁环熔化而导致阳极脱落,可先将导杆取出,留在槽内的碳块待启动后再捞出。如因局部温度过高而导致该处物料熔化速度加快,特别是中缝和极缝处的保温料塌陷,出现火孔时,应及时添加物料封住火孔,以减少热损失和防止阳极氧化,提高能量效率既可局部降温又可加快物料熔化。如个别阴极钢棒因电流集中而过热时,可用风管吹风降温,若效果不好,则可用调整对应的阳极电流的办法解决。在点动阳极抬电压时的过程中,如出现电压大幅摆动现象停止点动。对于导电效果较差的阳极可以松开卡具,用大锤在到杆顶端使劲往下敲击,以增加该极与焦粒的接触,改善导电效果。焙烧时期电压变化是衡量焙烧效果的一个重要条件,对异常情况的正确处理是保证焙烧槽电压稳定有序变化的关键,焙烧电压曲线如图6。
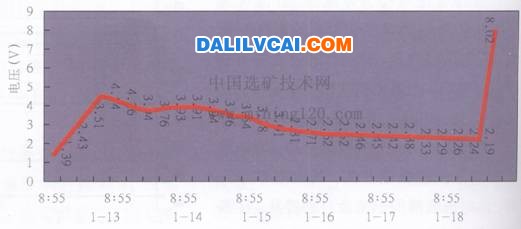
图6 焙烧历史曲线
(二)启动期间
启动期间如发现槽壳侧部的温度达到350℃以上应及时吹风降温。如果发现个别阴极钢棒温度过高,应及时吹风冷却,若温度继续升高,甚至出现钢棒发红现象时,可采取摘出阳极组的办法,但每台槽的阳极摘出量不得超过3组,做好用水冷却钢棒的准备,必要时用水冷却。为避免电解质“含炭”,启动时槽温应控制在980℃~1000℃,若出现“含炭”苗头,应果断地取加冰晶石降温或倒换电解质措施,尽力避免“含炭”。
灌铝后如出现渗铝现象,应当即吹风降温,若吹风后仍继续渗铝,应在边部加入镁砂和氧化铝混合料,然后用天车或碓子将混合料砸实,并及时汇报。如发生漏炉事故,应积极采取措施,用镁砂等堵漏,如仍不能解决问题应及时降阳极,将电压降至最低点,与此同时立即汇报现场指挥与整流所联系,将电流降至80KA以下,以最快速度完成短路操作,尽量将损失降至最低程度。
(三)测量监控
焙烧槽电压记录,升至全电流时,记录下当时的冲击电压。第一次记录后,每4小时记录槽压和时间,并据此做出电压曲线。焙烧槽温度测量和记录(预埋电热偶的槽测量)测试位置在预埋9根热电偶套管处。通电30分钟后进行第一次测量。第一次测量后,每4小时测量一次,并据此做出温度曲线。
阳极电流分布的测量和记录:通电30分钟后进行第一次测量,此后每1小时测定一次,特殊情况可加大频次。对于电流分布过高、过低处要重点标出并汇报,对分布异常的不仅要处理,而且要将处理结果和处理时间记录下来。
阳极钢爪温度的测量:升全电流一小时后测量一次,以后每小时测量一次,以后可根据现场情况决定是否需要测量。
阴极钢棒和槽壳温度的测量:焙烧期间每l小时测量一次,启动后3天内每8小时测量一次。
阳极上下串动记录:焙烧期间每天测量记录一次。
表1 电压保持和温度控制参考值表
启动时间
|
8h
|
16h
|
24h
|
36h
|
48h
|
72h
|
96h
|
120h
|
第6天
|
第7天
|
第二周
|
第三周
|
第四周
|
第五周
|
电压(V)
|
7.5
|
6.5
|
6.5
|
5.0
|
4.6
|
4.5
|
4.5
|
4.4
|
4.3
|
4.3
|
4.25
|
4.25
|
4.25
|
4.20
|
6.5
|
6.0
|
5.0
|
4.8
|
4.5
|
4.4
|
|||||||||
温度
|
980
|
970~980
|
960~970
|
表2 启动后分子比参考值表

三、后期管理
电解槽后期管理非常重要,对电解槽以后的平稳高效有着决定性的影响,对后期管理主要特点包括高温、高分子比、高电解质水平、低铝水平等管理思路,目的就是在这一时期要形成规整的炉膛。我公司后期管理主要内容如下。
1、电解槽启动后期的管理
2、效应系数和NB间隔
效应系数:启动后5天内2次/槽·天,15天内1.0次/槽·天,15~30天内0.5~1.0次/槽·天,此后视电解槽运行情况可逐渐转入正常情况。
NB间隔:启动一周内2.5~3分钟,一周后设定为2~2.5分钟。以后视情况转入正常。
3、分子比管理
4、铝水、电解质水平保持
铝水平:启动一个月内按15~17厘米保持,一个月后按18~20厘米保持。
电解质水平:启动一个月内按23~26厘米保持,一个月后按20~22厘米保持。
四、总结评价
通过对对230KA电解槽焙烧启动特点的分析,我们不难发现只要掌握住了技术要点并且持之以恒严格管理,那么在实践上就能取得较好的效果。我公司1 78台电解槽在焙烧启动过程中没有出现过一次脱极和早期破损现象,也证明了措施的可行性、科学性。总体说主要有以下几点:
(一)电解槽的焙烧启动工作是电解槽生产的开端,要以科学理论和技术为依据,在实践生产中与时俱进,以延长电解槽正常高效为目的,不断优化工艺。
(二)从电解槽焙烧启动操作工艺的各个环节看,它还是一项系统的管理工程,必须加强技术和管理方面的培训,以适应生产的需要。
(三)掌握住焦粒焙烧启动特点和方法,可以使得电解槽的阴阳极电流分布更加均匀,升温速度更加合理,槽温分布均匀,避免了局部过热的现象,扎固糊焦化良好,可望获得较长的槽寿命,降低吨铝生产生本。
(四)采用焦粒焙烧启动技术,简便实用,成本低廉,易于操作。但是230KA预焙阳极电解槽采用双阳极结构,由于铺焦粒和阳极组装的质量问题,常会造成铝导杆导电比较均匀而两块阳极电流分布不均的情况,这是双阳极电解槽致命的缺点,应该引起足够的重视。
(五)在电解槽启动后的一年中,后期管理非常重要,应严格避免技术条件的大起大落,有了这一年的平稳运行期后,电解槽的运行将会非常稳定,不仅高效低耗,减小劳动强度,也有利于延长电解槽寿命。