摘要:简单介绍了铝型材挤压成形的特点,对目前用于铝型材挤压仿真的
FEM 、FVM 技术进行了详细地对比,对国内外铝型材挤压仿真技术的应用情况进
行了介绍和分析; 最后对专用铝型材挤压成形仿真软件 HyperXtrude 的功能和应
用情况进行了介绍。
关键词:铝型材挤压;仿真;HyperXtrude
1 引言
铝型材产品由于具有重量轻、强度高、导电导热性好、外形美观、密封性好
等优点,被广泛应用于建筑、车辆、船舶、飞机、通讯等各个领域,特别是建筑
门窗和幕墙,其发展速度远远高于其他金属材料,在金属产品中的消费量仅次于
钢铁[1]
。
挤压成形是铝型材生产的主导技术和核心环节, 挤压模具是铝型材挤压成形
的关键装备。在铝型材挤压过程中,模具结构不良容易导致型材扭拧、波浪、弯
曲以及裂纹等缺陷问题。 目前铝型材挤压模具的设计还停留在依靠工程类比和设
计经验阶段,所设计的模具必须经过反复的试模和修模来调整工艺参数,有的模
具试模次数达到 10 次以上,这严重影响了企业的模具开发周期和生产效率,影
响模具质量和模具寿命,增加了经济成本和时间成本,因此改进传统的模具设计
方法已经成为铝型材及其模具厂家的当务之急。
大量的文献资料显示, 以有限元方法为代表的仿真技术正在成为优化铝型材
模具的重要和必要的途径。铝型材挤压过程是一个处在大变形、高温、高压、复
杂摩擦条件下的非线性成形过程, 采用物理实验和现有的测量仪器与手段基本上
无法了解其中的成形机理和变形规律, 而运用仿真技术可以实时跟踪铝型材挤压
金属的流动行为,仿真成形过程,揭示金属的真实流动规律和各种物理场量的分
布、变化情况,研究各种因素对金属变形行为的作用和影响,预测实际挤压过程
中可能出现的缺陷,及早优化模具结构设计、调整挤出工艺参数和有针对性的指
明技术解决方案,等等。因此,基于仿真技术的铝型材挤压成形及模具优化技术
得到越来越广泛和深人的研究和应用。
本论文对铝型材挤压成形特点、挤压成形仿真关键技术、国内外的研究应用
现状等进行了详细的论述,最后对专用铝型材挤压成形仿真软件HyperXtrude 的
功能和应用情况进行了介绍。
2 铝型材挤压成形特点
铝型材挤压成形工艺过程可以看作是一种特殊的、复杂的流体运动过程,属
于三维流动、非线性、大变形问题。在挤压成形过程中,会不断的产生新的自由
表面、产生新的热量,发生温度传递、大变形、复杂几何形体变化等各种交叉藕
合现象;整个挤压过程可以分为非稳态开始、稳态成形、非稳态结束三个阶段,
在非稳态的挤压变形阶段,弹性变形由于远远小于金属的塑性变形而可以被忽
略;但是在稳态变形阶段,塑性变形不再剧烈的条件下,则必须考虑弹性变形的
影响,因此,其材料本构模型也非常复杂;同时,在高温状态下材料的粘度性能
不符合常粘度定律,材料的应变速率及温度对变形的影响不可忽视。
模具是铝型材挤压成形的重要装备,是决定铝型材产品质量的先决条件之
一。铝型材挤压导流模的形状和尺寸、分流腔的数量和分布、焊合室的形状和深
度、定径带的长度、模具表面的光洁度等都会影响铝合金在成形中的流动状态,
进而影响型材挤出的质量。铝型材制品尺寸越大、形状越复杂,其变形的不均匀
性就越显著,截面卜各部分的金属在挤出模孔时的速度差异就越大,就越容易造
成型材的扭拧、波浪、弯曲及裂纹等缺陷[1]
。
3 铝型材挤压仿真技术
目前,铝型材挤压仿真所采用的技术主要有两种,第一种是基于 Lagrange
格式的有限元方法(Finite Element Method , FEM ) ,第二种是基于 Euler
格式的有限体积法(Finite Volume Method , FVM )[2~3]
。
3.1 有限元方法(FEM)
FEM 的基本思想是将材料的整个求解域离散为一系列相互连接的单元体(如
三角形、四边形或六面体等单元),通过求解各单元和节点在每一加载步上的物
理场量,来描述材料在成形过程中的变形情况。有限元方法必须满足的基本方程
包括平衡方程、几何方程、本构方程、屈服准则、体积不可压缩条件、力和速度
边界条件。
用有限元方法进行铝型材挤压成形仿真的优点是, 在计算过程中节点的位置
随着成形的进行而不断发生变化,单元的形状也随之发生变形,因而,节点与单
元瞬态的物理场量可以很好地描述成形体的变形情况。 这种方法不仅能很好处理
复杂边界问题,而且能跟踪材料变形节点,记忆材料变形的历史,非常适合分析
瞬态成形问题。
用有限元方法方法进行铝型材挤压成形仿真的缺点是, 计算过程中网格会经
常发生畸变,导致体积损失过大,甚至出现网格无法生成的情况,必须对畸变后
的网格进行重新划分,而这种方式既浪费计算时间,又降低了计算的精度,变形
程度大时甚至无法进行下去。
因此,有限元方法主要用于一些形状相对简单的铝型材挤压成形仿真,对于
复杂的铝型材,特别是具有薄壁、空心、复杂断面、高精度等特征的幕墙、门窗、
散热器、壁板等复杂铝型材,基本上没有办法进行仿真。
3.2 有限体积方法(FVM )
FVM 数值模拟的基本思想是将材料流动所要经历的空间用 Euler 网格 (如六
面体网格)进行离散,Euler 网格的单元和中心格点在空间固定不动,材料只是
从一个单元流到另一个单元,并且材料的质量、动量和能量也随之从一个单元流
到另一个单元,材料的变形行为则通过均布在材料中的大量质点来表述。使用
FVM 方法必须满足质量守恒、动量守恒、能量守恒、本构关系、状态方程和热平
衡方程等控制方程。
用有限体积法进行铝型材挤压成形仿真的优点是, Euler 网格不随材料一起
运动,因此网格在成形过程中不会发生畸变,求解过程中不需要进行网格重划;
且采用直接积分和显式求解方法,不需要迭代求解平衡方程,因此能处理各种复
杂程度的大变形问题,且计算时间相对较短。
用有限体积法进行铝型材挤压成形仿真的缺点是,在划分网格单元时,划分
范围必须包括材料所有可能流过的区域,而且网格需要划分得很细,因此采用有
限体积方法需要占用大量计算机内存,特别是对于具有薄壁、空心、复杂断面等
特征的铝型材需要占用更多的内存,因此这种方法对计算机硬件系统的要求极
高。而且,在有限元体积方法中,由于有限体积网格和中心格点在成形过程中固
定在空间不动,因此,它不能反映金属成形过程中材料的整个流动情况,它只适
合分析边界条件不变化的稳态问题, 不适合分析具有自由表面问题和依赖变形历
史等特征的瞬态成形问题。
3.3 两种方法的比较与应用
目前,两种有限元方法在铝型材挤压成形仿真中都得到了应用,其中,基于
Lagrange 格式的有限元方法主要用于仿真坯料从挤压开始时刻到挤出模具时刻
的非稳态阶段,获得挤压型材头部的变形情况以及挤压缺陷等情况;Euler 格式
主要应用于稳态分析,即假设型材已经挤出模具,分析挤出型材的速度场、温度
场以及应力应变等。
4 国内外铝型材挤压成形仿真技术应用现状
国内外科研工作者在铝型材挤压仿真技术的研究和应用方面开展了很多工
作。
T.Chanda 等[4~7]
基于刚粘塑性成形理论,使用基于 FEM 的 DEFORM 系统研究
了简单实心铝合金模具挤压过程中挤压比和挤压速度对坯料温度变化的影响、 挤
压载荷的变化情况、以及挤压速度和型材温度的关系等;Zhi Peng 等[8~9]
使用基
于 FEM 的 FORGE3 系统研究了多孔实心棒材挤压时模孔对材料出口流动速度、温度差异、变形力等的影响,分析了模具设计、挤压工艺参数对产品质量(型材形
状、表面质量和微观组织)等的影响;
J.Lof
[10~11]
分别针对简单薄壁空心筒形件和异形件,使用基于 ALE 描述
DiekA 代码研究了模具工作带内的材料行为、摩擦系数、工作带长度情况,研究
了模具工作带内的弹性变形的影响。
Chris Harris等[12~13]
使用DEFORM 系统研究了简单形状的铝型材件挤压成形
中的新旧棒材交接处的瞬态焊合现象进行了模拟, 导流模尺寸参数对金属流动的
影响规律;
在国内,周飞等[14~16]
人对有限体积方法进行了深人研究,提出了将有限元方
法和有限体积方法相结合的复合方法,以及有限体积分步求解方法,并用于简单
薄壁门窗型材模具的挤压成形仿真;
吴向红等人[17~19]
采用基于FVM 的Superforge系统对大口径铝管的平面分流
模挤压过程进行了数值模拟,分析了挤压过程中各个阶段的应力、应变的分布情
况以及金属的流动规律, 为大型铝型材挤压模具结构的设计和工艺参数的优化提
供了依据;对长方形空心铝型材管挤压过程进行了数值模拟和模具结构优化;研
究了挤压速度和摩擦状态对铝型材挤压过程中的模具受力、 挤压件分度分布变化
以及材料流动速度的影响情况和影响规律。
于沪平等[20]
采用 DEFORM 系统对平面分流模的挤压变形过程进行了二维模
拟, 得出了挤压过程中铝合金的应力、 应变、 温度以及流动速度等的分布和变化;
陈泽中等人[21~23]
应用 Superforge 系统研究了复杂铝型材挤压成形过程,将
有限体积技术应用于宽展挤压模具的设计中, 获得了与实际金属流出速度相符的
模拟结果;建立了基于正交试验、人工神经网络、遗传算法的优化模型,对大型
实心铝型材挤压过程进行了模拟和优化, 获得了最优的铝型材挤压工艺和模具参
数(模具工作带长度、导流模的宽度和深度、模具预热温度、坯料预热温度、挤
压速度)。
总结国内外的研究现状发现, 目前的铝型材模具挤压仿真技术的发展和应用
情况具有以下特点:
1)目前国内用于铝型材挤压成形仿真的有限元系统主要有 DEFORM , MARC ,
ANSYS ,这些系统都是基于 Lagrange 格式的,DEFORM 是专业针对锻造成形开发
的,ANSYS 和 MARC 是通用的综合性分析软件;基于 FEM 的铝型材模具挤压成形
主要是针对简单、小型的铝型材件,由于受到网格畸变和有限元程序网格重划功
能的限制,对大型、复杂、薄壁的铝型材模具的挤压成形仿真结果不理想,甚至
无法实现;
2)于 FVM 的铝型材模具挤压成形仿真可以模拟一些复杂、大型、薄壁的铝
型材的挤压成形过程,但目前所用的有限体积仿真系统主要是 Superforge,该
系统基于 Euler 述,只能对瞬态成形阶段进行模拟,得不到填充、焊合等非瞬态阶段的变形和变形情况;且该软件是专业针对锻造成形开发的,无法正确描述铝
型材成形过程中的分流、焊合等流体问题。虽然周飞等人将其他有限元分析系统
与 SuperForge 相结合,先用有限元仿真系统分析瞬态过程以后,再利用
Superforge 分析稳态过程,获得了一些理想结果,但是有限元分析结束以后必
须进行三角形网格分解,同时将各物理场量传递到 FVM 仿真系统,这种不同仿
真系统之间的数据传递算法和精度仍然是值得探究的问题。
5 HyperXtrude 软件介绍
如上所述,基于 Lagrange 格式和基于 Euler 格式的软件系统各有利弊,且
利弊互补。为了发挥这两种方法各自的优势,出现了一种集成系统,也称
Arbitrary Lagrange - Euler ( ALE )方法,这种系统将材料速度和网格速度
分开定义,空间网格可以设置成运动的,也可以设置成固定的,通过选择网格的
运动形式就可以任意(arbitrary)指定是使用肠瞥朋罗描述还是 Euler,描述
来求解挤压成形问题。
HyperXtrude 系统就是基于 ALE 描述的一款商用软件系统。它是
HyperWorks 产品家族中的一员,也是由美国 Altair 公司开发的一个专用的铝型
材模具挤压仿真求解器。该软件通过与前处理模块 HyperMesh 和后处理模块
Hyperview 结合,能够实现对各种复杂程度的实心模和空心模的挤压成形仿真,
求解挤压过程中材料流动和热传递的规律;能与优化模块 HyperStudy 结合,实
现模具工作带长度优化;该软件针对铝型材模具挤压成形的特点,提供了很多智
能化的操作处理方式,比如广泛的数据接口,挤压筒、工件和模具的自动定义,
支持常见的挤压型材材料本构关系,方便的边界条件设置,数据结果的多种显示
形式等等。
HyperXtrude 系统所具有的功能包括:
l )铝型材挤压变形仿真:可以仿真各种实心模和空心模的型材挤压变形过
程,获得挤压过程中金属应力、应变、温度、流体速度等物理量的分布和变化情
况;
2 )铝型材挤出的变形分析:能获得挤出型材的变形情况;
3 )模具变形分析:分析计算模具的变形和模具内的应力分布情况;
4 )温度场仿真分析:能够定义坯料、模具和周围环境之间的热交换,计算
得到坯料内的热传导、挤压筒和模具周围热传递、挤压温升和挤压速度的关系。
5 )摩擦仿真:支持定义工件和模具之间、坯料和模腔之间的库仑摩擦模型
或塑性剪切摩擦模型。
6 )棒料接口跟踪分析,可以预测料尾长度;能够跟踪挤压过程中坯料表面
并预测表皮杂质进人挤压型材的时间。 7 )工作带长度优化模块,能以获得均匀的工作带型材流出速度为目标,优
化工作带长度。
该软件基于 ALE 描述,用户可以根据需要选择是对稳态阶段还是非稳态阶
段进行分析。
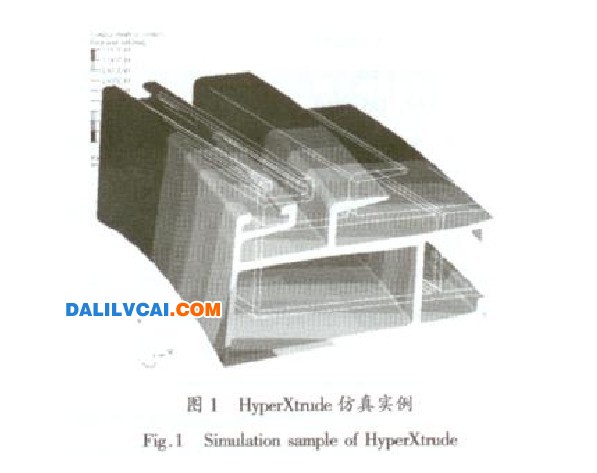
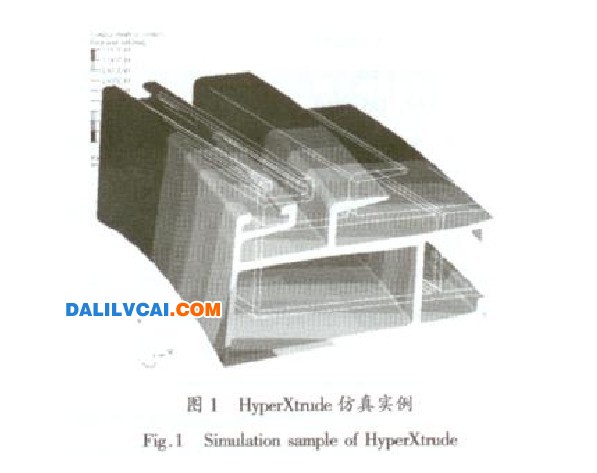
以下是运用 HyperXtrude 系统仿真分析得到的某空心铝型材的型材变形趋
势和程度,仿真结果显示,型材变形很厉害。
6 结论
铝型材产品不断向着复杂、大型、高精、高强度等方向发展,模具设计的难
度越来越大, 利用仿真技术取代传统的经验开模和反复试模是未来铝型材生产的
必要趋势。 加快铝型材挤压仿真应用研究及其关键技术的深人研究是目前铝型材
挤压及其模具企业急需突破的核心技术,有待科研工作者结合实际,开展更广泛
和更深入的调查研究。
利用仿真软件实现铝型材挤压成形仿真技术的研究PDF高清版下载:
http://bbs.dalilvcai.com/Aluminum%20extrusion/thread-3316-1-1.html
利用仿真软件实现铝型材挤压成形仿真技术的研究PDF高清版下载:
http://bbs.dalilvcai.com/Aluminum%20extrusion/thread-3316-1-1.html