1 前言
本文将重点介绍重力和低压铸造涂料的开发和应用.
自从重力铸造和低压铸造法问世,人们就认识到金属型涂料的重要意义.选择和有控制地应用最佳的金属型涂料,或将涂料进行合理的组合,如同金属型设计、金属的处理及浇注系统一样,对生产精美的铸件起着重要的作用.
2 涂料的功能和特性金属型涂料的基本作用有:
•保护金属模具,延长模具寿命;
•利于铸件脱模,防止粘结和氧化物堆积;
•控制由铸造合金向金属模具传递的热流.
•改善铸件表面光洁度.
由于生产质量优良的铸件需要控制铸造合金充填金属型腔和在金属型腔内凝固的全过程,因此金属型涂层的最重要的功能无疑是使金属型具有绝热层并控制热流由铸造合金向金属型腔内的传递.
涂料的绝热性主要取决于三个关键因素:
(1)涂料成分;
(2)涂层厚度;
(3)涂层孔隙度.
2 . 1 涂料成分金属型涂料目前主要是以水为载体,加入高温粘结剂和耐火填料.绝热涂料含有绝热矿物混合料,涂料中的填料在铝合金的正常温度下应有足够的耐火度,保证其不发生化学变化,基本上只是物理作用.金属型铸造者在选择用于所生产的具体铸件的涂料或涂料成分时,需要考虑的最关键的涂料性能是:导热率、粒度、润滑性,以保证铸件易于脱型和表面光洁,并保证涂层有较高的绝热性以防止铸件浇不足.目前配制绝热涂料的主要成分是氧化铝、滑石粉、云母、硅藻土和氧化钛,这些矿物质均具有很高的绝热性.
2 . 2 涂层的厚度
图1为我们所生产的绝热涂料涂层厚度与其绝热性的关系曲线,该图表明,300μm厚度的涂层,其绝热重力和低压铸造涂料的开发和应用性并不比200μm的涂层提高很多,且由于超过300μm的涂层极易与金属型分离而剥落,故涂层的最佳厚度应为150~250μm .
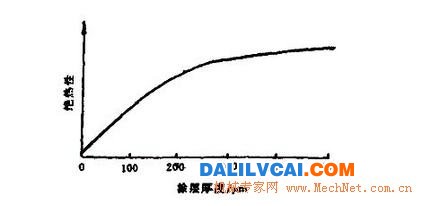
图1 涂层厚度与绝热性的关系曲线
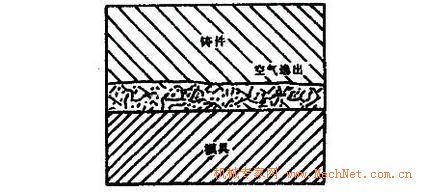
图2 DYCOTE 34涂料颗粒形貌示意图
2 . 3 涂层的孔隙度
涂层孔隙度的形成主要取决于与金属型型腔表面接触的载体水的蒸发速度,即取决于涂覆方法和涂覆条件.一般在铸型温度为170~200℃时进行涂覆常能获得最佳的结果.现在大多数铸造厂涂料的使用还是采用在生产现场人工搅拌,然后倒出一部分稀释使用,由于人为因素很多,常常导致涂料成分比例失调,有时也导致粘结剂的比例失调,使金属型保温性能不均匀和涂层脱落.国外许多厂目前已在生产现场设立中心搅拌站,涂料在中心搅拌站内稀释并一直保持搅拌状态,这样保证其成分均匀一致,从而使涂层在模型上的沉积均匀一致.
在较高的金属型温度进行涂覆时,由于涂料的载体水与高温金属之间反应强烈,通常能获得很大的孔隙度,这时涂层的绝热性自然很好,但涂层对铸型的附着力及寿命均很低,这是因为过高的金属温度会引起强烈"回弹",使涂层难以粘附到金属型型腔表面上的缘故.
相反,型温较低时虽然涂层寿命较高,但这种涂层致密,绝热性很差,而且过低的金属型涂覆温度会形成涂层"堆积",当金属型加热到工作温度时就会产生涂层开裂和起皮的缺陷.3 涂料的开发和应用
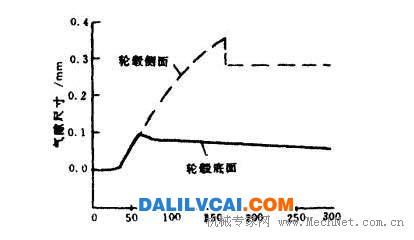
图3 空气间隙瞬间变化曲线
DYCOTE 140是一种润滑的、中高级绝热涂料,极其通用,常用于小型或中等截面的铸模,如活塞件,小型的汽车轮毂、摩托车轮毂等,该种涂料涂层经久耐用并具有抗剥落性.
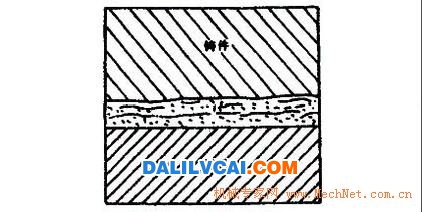
图4 DYCOTE 39涂层层叠板形形貌示意图
DYCOTE 39可提供最高水平的光滑晶亮的铸件表面,由于DYCOTE 39中大量的耐热充填物如层叠的板形(见图4),使涂料与金属液的接触面积增大,从而使铸件的表面光泽非常好.但这种耐热的板形形貌不能夹入大量的空气,所以其绝热性比类角形形貌的DY - COTE 34要低,有时候,在需要绝热的位置,要考虑与DYCOTE 34配套使用.
这三种涂料按其绝热性排列为DYCOTE 34,DY - 7 5 1COTE 140,DYCOTE 39依次递减,而铸件表面光洁度则依次递增.
3 . 2 润滑/导热涂料产品贸易名称为DYCOTE 11 .以半胶体石墨为基,用于帮助铸件脱型,同时,DY - COTE 11也适用于重力铸造的活动部分,如模芯,滑杆等处的润滑和模具接合面的润滑.
3 . 3 半绝热涂料
产品贸易名称为DYCOTE 36 .该种涂料具有良好的脱型性能和适中的绝热性能.
3 . 4 涂料性能综述表
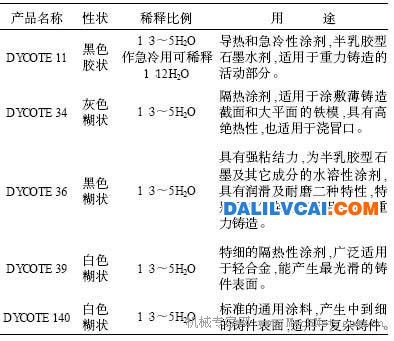
4、涂料的施涂
4 . 1 模具准备
新金属型施涂前必须进行彻底的清理,除去所有的润滑油脂和锈斑,已经使用过的金属型必须将原有的涂层彻底清除掉。
目前清理金属型的方法主要是钢丝刷清除型面污垢,喷砂喷丸清理和湿化学无损清洗法(本公司生产湿化学清洗脱膜剂ANISCOL 100)。清理后的模具均匀地加热到300~350℃,加热方法通常采用将煤气燃烧嘴适当地分布在金属型内侧及四周,但用这种方法加热金属型难免会使整个金属表面产生温度差。现在,许多铸造厂已在专用的预热炉中预热金属型模,以保证整个金属型具有极其均匀和平滑的温度场。
4 . 2 涂料的混合和稀释打开桶盖,将涂料再彻底重混一次,倒出要求量,按要求的稀释倍数进行稀释,持续混合一段时间直到其均匀。
4 . 3 施涂待模具温度降到180℃左右,在模具的不同位置按性能要求选用适当的模具涂料,操作应迅速而仔细,从几个不同的角度喷入,保持喷枪移动以减少模具表面的盲区。涂料最好是薄薄的喷3~4层而不是厚的1~2层,喷枪离模型距离为200~350 mm ,喷枪压力设定不大于200 kPa ,喷涂技术好会使铸件的表面质量出现惊人的提高。涂层厚度控制在150~250μm ,现国外许多铸造厂已采用磁性笔型仪来测量涂层的厚度,并把它作为一种在线控制的手段。喷涂过程中金属型的温度对涂层的工作性能影响很大,因此越来越多的铸造厂用光测高温计或计算机外形的热电偶测量金属型的温度,只有控制好各工艺参数,才能生产出完善的铸件。
5 结束语
金属型铸造时,涂层的厚薄、组分和配比均影响合金充型和定向凝固的能力,所以涂料的选择和施涂成为金属型铸造法生产优质铸件的首要环节。我们相信,随着铸件质量要求的日益提高,将导致更广泛地采用过程控制技术,并推动涂料不断地改进和发展。
功 能
1、ZD涂料起隔热,均衡温度,免除因金属液的冲击与腐蚀性从而达到保护摸具和延长摸具使用 寿命可长达1/3以上; 2、防止铸件产品因局部冷却过快而造成的开裂和白口铁形成; 3、吸附时间长达7天之久,透气性好,每次脱模可用乙炔烟熏处理来代替脱模剂的使用,浇注一个铸件烟熏一次即可;
优 势
1、与磷酸盐涂料相比它特有的物理性能决定了它的优势; 2、透气好; 3、保温隔热效果明显,熔点在1650℃以上; 4、喷吐后附着力强且不宜剥落,通常一周后才需修补,ZD涂料不需要象其它涂料一样每次开摸要喷涂,省却每天因喷补 涂料而拆装摸具的繁琐工作; 5、相对而言价格便宜,大大降低了因使用醇基涂料或进口涂料所带来昂贵的生产铸造成本; 6、大大提高生产效益。