摘要: 汽车轻量化技术的发展,使轮毂的制造技术水平得到了很大提高,同时也向其提出更高的质量要求。对低压铸造 A356 铝合金轮毂弯曲疲劳试验产生的两类不同特征的裂纹进行了 SEM 观察,对比了两类疲劳裂纹的特点,分析了其起因,以及显微组织和铸造缺陷对低压铸造 A356 铝合金轮毂疲劳性能的影响。在此基础上,提出了改善铝合金轮毂疲劳性能的措施。
关键词: 铝合金;轮毂;疲劳性能;铸造因素
Influencing Factors of Fatigue Life of
Low Pressure Die Casting A356 Alloy Wheel
WU Han—qi 1 , LI 5huang-shou 2 , JIN xin—yan 2 , LV Shuo 1
(1.Dicastal Wheel Mfg Co.,Ltd , Qinhuangdao 066003 , Hebei . China ;
2 .Tsinghua University , Beijing 100084 . China)
Abstract : With rapid developments of fight weight fabrication technologies of automobile , the level of manufacturing technology and equipment of automobile wheel is improved g greatly , and much higher quality requirements are put forward.In this paper , two different kinds of bending fatigue cracks of A356 alloy wheel have been investigated . their characteristics are compared , forming reason is analysed , as well as the effects of foundry technology and defects on the fatigue life of wheel. On the basis of above, measures to increase the fatigue life are suggested.
Key words : A356 alloy ; automobile wheel ; fatigue life ; influencing factors
铝合金轮毂以其独特的优点在轿车上应用日益广泛 [1] 。轮毅是汽车行驶安全方面的重要部件之一,在行驶过程中承受垂直载荷、横向载荷,驱动、制动扭矩,旋转的轮毂承受周期变化的弯曲扭矩和径向应力,因此,铝合金轮毂的疲劳性能是衡量其质量的重要指标之一。汽车行业在铝轮毂需求量激增的同时,对铝合金轮毂性能的要求也更为严格,特别是高档轿车对铝合金轮毂的疲劳性能提出更高的要求。目前国内外研究人员对 A356 合金的疲劳性能进行了大量的研究,但是大多只针对合金材料本身。研究 A356 材料的铝合金轮毂的疲劳性能,分析影响 A356 铝合金轮毂疲劳性能的因素,对增强轿车用铝轮毂的安全性意义重大。本研究中对低压铸造 A356 铝合金轮毂弯曲疲劳裂纹进行观察,对影响 A356 铝合金轮毂疲劳性能的因素进行分析。在此基础上提出了改善铝合金轮毂的疲劳性能的措施。
1 试验材料和方法
试验用轮毂材质为 A356 铸造铝合金,采用 AI-5Ti-1B 中间合金进行细化处理,采用 Al- 10Sr 中间合金进行变质处理。低压铸造成形后进行 T6 热处理、机加工及表面涂装保护。图 l 为A356 铝合金轮毂 T6 处理后的显微组织,主要由α -Al 基体、 Al-Si 共晶组织以及少量富铁相颗粒组成。
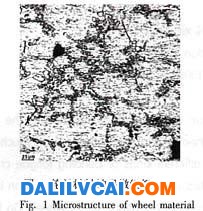
在弯曲疲劳试验机上进行弯曲疲劳试验,如图 2 所示。轮毂端面固定,轴端施加载荷 F , F可绕轴旋转,力臂为 L ,从而对轮毂施加周期变化的弯曲扭矩 M=F × L 。同一型号的轮毂在弯曲疲劳试验中产生疲劳裂纹。对存在裂纹的外表面、横截面和局部的断面进行光学显微镜和扫描电子显微镜观察。其中,对侧面进行抛光处理,光学显微镜下观察的样品使用 kellers 试剂腐蚀。

2 试验结果及分析
2 . 1 裂纹形貌
在扫描电镜下分别观察样品表面裂纹和垂直于裂纹的横截面的形貌,可以将裂纹归纳为两类:A 类为贯穿铸件壁的大裂纹, B 类为在铸件表面随机分布的细碎裂纹,如图 3 所示。产生 A 类裂纹的循环次数比产生 B 类裂纹的循环次数约低一个数量级。
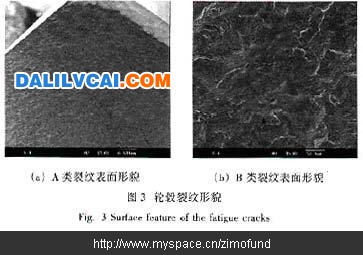
图 4 为 A 类裂纹横断面的形貌,观察到尺寸较大的气孔与缩孔,这些孔洞类缺陷是材料的薄弱环节。一方面,它们容易成为裂纹源,图 4c 气孔缺陷中可以明显观察到有新的裂纹生成,裂纹方向基本上沿着缺陷的纵向,这是由于缺陷引起的应力集中所致;另一方面,缺陷处产生微裂纹之后,主裂纹扩展会选择这些路径传播,同这些微裂纹汇合,裂纹传播速度加快。
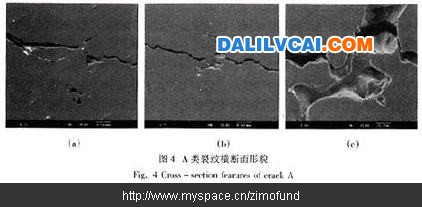
图5 为 B 类裂纹横断面的形貌,同 A 类相比,裂纹尺寸较小,未发现大尺寸的气孔及缩孔。图 5a、 b 中,裂纹沿着共晶硅与铝基体的界面传播,这是铝硅合金裂纹萌生和传播的主要形式之一。此外,有部分裂纹沿着富铁相界面传播(图 6a )或者裂纹垂直于富铁相传播 ( 图 6b) 。
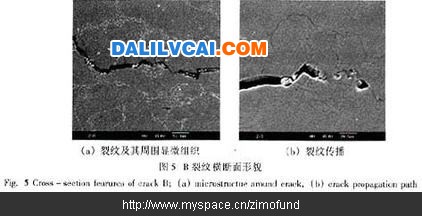
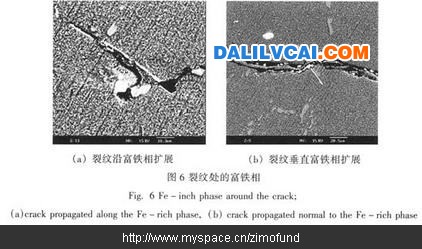
2 轮毂疲劳性能影响因素分析
影响铝合金轮毂疲劳的因素包括轮毂的结构特点、组织特点和服役条件等。结合对疲劳裂纹的观察,从低压铸造 A356 铝台金轮毂的铸造缺陷及显微组织特点两方面分析对铝合金轮毂疲劳性能影响。
2 .2. 1 铸造缺陷对 A356 铝合金轮毂疲劳性能的影响
目前铝合金轮毂最主要的成形方法是低压铸造,缩孔、缩松、气孔和夹杂等缺陷影响着铝铸件的质量 [2] 。对于一定结构的轮毂,铸造缺陷是疲劳寿命最主要的影响因素。气孔和夹杂不但缩短了疲劳裂纹的传播时间,更重要的是缩短了裂纹的产生时间。
有研究表明 [3] 缩孔形状和分布复杂,最大直径大于 0.2 mm 时,疲劳裂纹产生的时间很短,对疲劳寿命有显著的影响。减小收缩缺陷的尺寸将提高铸件的疲劳寿命,不过并非能够无限制的提高疲劳寿命 , 当试样表面连续滑移带开始起作用后,减小收缩缺陷的尺寸时疲劳寿命将不再提高 [4] 。 ,
气孔和夹杂的尺寸及位置不同对轮毅疲劳寿命的影响程度也不同。离自由表面近的缺陷同铸件内部的缺陷相比,前者对疲劳寿命的有害影响更大 [5] , 一个较小的、单个的、离表面很近的气孔可能产生很大的影响。自由表面的缺陷同内部相比,其应力强度因子可提高55% [6] 。
对比 A 、 B 两类裂纹可以看出, A 类裂纹周围存在较大尺寸的气孔,因此它产生一条裂纹后迅速扩展;而 B 类裂纹比较短小,各段裂纹的扩展速度较慢,且没有合并成一条大裂纹,可知 B类裂纹的疲劳寿命要高于 A 类裂纹。气孔与氧化夹杂相比,前者对疲劳的有害影响更大。
因此,要提高 A356 铝合金轮毂的疲劳性能,首先应该考虑降低气孔、缩孔、夹杂等铸造缺陷的数量和尺寸。
2 .2. 2 显微组织对 A356 铝合金轮毂疲劳性能的影响
缺陷存在临界尺寸,当小于该尺寸时,裂纹会从滑移带、共晶颗粒等位置产生。随着铸造质量的改进及铸造缺陷尺寸的减小,显微组织对疲劳寿命的影响日益引起关注。铸件的晶粒粗细、基体屈服强度、共晶硅相的形貌与分布以及富铁相等脆性相的存在都影响到 A356 铝台金轮毂的疲劳寿命。
对于少无缺陷的 A356 铝合金而言,共晶硅相形貌对疲劳裂纹的萌生和扩展显得很重要。本试验用轮毂材质经过 Sr 变质处理,共晶硅呈细小的纤维状, T6 热处理进一步优化了硅相的形状及分布。 A 类裂纹主要由缺陷造成,因此硅相的影响不明显,而在 B 类裂纹 ( 图 5) 中可明显观察到裂纹沿硅相与基体的界面传播的现象。由于硅相与铝基体界面强度低,因此在交变载荷作用下,部分硅相同基体首先分离,形成微裂纹并进一步长大成为裂纹源.或者成为主裂纹的传播路径。在本试验中也观察到了共晶硅断裂的现象引起的失效形式,但这种失效形式出现的较少。
根据 Lee 等人的研究 [7-8] 结果,对于 Sr 变质的铝硅合金,硅相尺寸 1.5 ~ 2.5 μ m ,硅相与基体的分离是主要的失效形式;对未变质的铝硅合金,硅相尺寸 3~9 μ m ,其主要失效形式为硅相的断裂;在硅相尺寸 2.5 — 5.5 μ m 时,是两种失效模式的混和模式。从能量的角度来看,含有球状共晶硅与含有片状共晶硅的铝硅合金相比,前者形成裂纹所需的能量约为后者的 4 倍[9] 。文献 [10] 分析了应力强度因子变化 Δ K 的大小对也失效形式的影响,认为在低 Δ K 时裂纹主要沿硅相与基体的界面传播,只有少量的硅相断裂;随着 Δ K 的增加,硅相断裂增加,当 Δ K~ Δ Kc 时,裂纹前沿附近的失效形式以硅相断裂为主。
A356 合金中发现了一些针状富铁相 ( 图 6) ,能谱成分分析结果表明该相为脆性 ß — Al5FeSi 相。文献 [11] 分析了富铁相对疲劳裂纹扩展行为的影响。针状富铁相同裂纹扩展途径存在两种关系:一种是裂纹扩展方向同针状富铁相接近平行,由于该相同铝基体之间的结合力相对较弱,因此在交变载荷下,该相同基体脱落形成空隙,从而加速裂纹沿基体和富铁相的界面扩展;另一种是裂纹扩展方向与针状富铁相接近垂直,富铁相容易发生断裂.从而促进裂纹的扩展。严格控制合金中杂质铁的含量对提高 A356 合金疲劳性能具有一定的作用。
细化晶粒能增加晶界,加大滑移的阻力,有助于降低裂纹的扩展速度。此外,还能够提高屈服强度,减少材料的局部塑性变形以及位错的塞积,从而降低裂纹的传播速度并减少材料中微裂纹的萌生。
因此,在少或无缺陷、显微组织起决定作用的 A356 铝合金疲劳裂纹萌生与扩展的材料中,通过细化、变质、热处理等手段获得细小晶粒及细小而呈球形的共晶硅颗粒能进一步提高疲劳性能。
2 . 3 提高 A356 铝合金轮毂疲劳性能的措施
综上所述,影响 A356 铝合金轮毂疲劳性能的首要因素是铸造缺陷,包括气孔、缩孔和夹杂等,因此,要提高 A356 铝合金轮毂疲劳性能,首先要从减少铸造缺陷人手。 (1) 对铝合金熔体进行充分的除气,保证氢含量在规定的范围内,从而有效地减少气孔的产生。 (2) 采用优化的铸造工艺参数,实现合理的模具温度分布,可以减少缩孔缩松缺陷,提高铸件的致密度。 (3) 采用热等静压工艺能够有效的减少铸件中的气孔,得到致密的铸件 [12] 。 (4) 对 A : 356 铝合金熔体进行充分的细化和变质,获得细小的晶粒和球形的共晶硅颗粒,消除片状共晶硅对材料疲劳的不良影响。 (5) 严格控制合金中杂质铁的含量,消除富铁脆性相的不利影响。 (6)A356 铝合金对热处理的组织同样敏感,合理的热处理条件,能够固溶强化合金和优化共晶硅的形状和分布,从而提高A356 铝合金的疲劳性能。
3 结 论
(1) 轮毂疲劳试验中形成两类裂纹,一类为贯穿铸件壁的大裂纹,另一类为在铸件表面随机分布的细碎裂纹。产生大类裂纹的循环次数比产生细碎裂纹的循环次数约低一个数量级。
(2) 大裂纹主要由缩孔、缩松、气孔和夹杂等铸造缺陷引起,细碎裂纹的形成与铸件的晶粒粗细、基体屈服强度、共晶硅相的形貌与分布以及富铁相等脆性相的存在有关。
(3) 减少铸造铝合金轮毂缺陷,细化晶粒,合理的热处理工艺,改善共晶硅的形貌与分布,控制杂质铁含量、减少富铁脆性相等方法均有助于改善铝合金轮毂的疲劳性能。