警告——使用本标准的人员应有正规实验室工作的实践经验。本标准并未指出所有可能的安全问题。使用者有责任采取适当的安全和健康措施,并保证符合国家有关法规规定的条件。
1、范 围
本标准规定了火焰原子吸收光谱法测定铁矿石中铝含量。
本标准适用于天然铁矿石、铁精矿和烧结矿,包括烧结产品中铝含量的测定。测定范围(质量分数):0.1%~5.0%.
2、规范性引用文件
下列文件中条款通过本标准的引用而成为本标准的条款。凡是注日期的引用文件,其随后所有的修改单(不包括勘误的内容)或修订版均不适用于本标准,然而,鼓励根据本标准达成协议的各方研究是否可使用这些文件的最新版本。凡是注日期的引用文件,其最新版本适用于标准。
GB/T6682 分析实验室用水规范和试验方法(neq ISO3697:1987)
GB/T6730.1 铁矿石化学分析方法,分析用预干燥试样的制备(idt ISO7764:1985)
GB/T10322.1 铁矿石取样的制样方法(idt ISO3082:1998)
GB/T12806 实验室玻璃仪器单标线容量瓶(eqv ISO1042:1983)
GB/T12808 实验室玻璃仪器单标线吸量管(eqv ISO648:1977)
3、原 理
用盐酸和少量的硝酸溶解试样,蒸发至二氧化硅脱水,溶解盐类,并过滤。灼烧残渣,用氢氟酸和硫酸蒸发除去二氧化硅,再用碳酸钠熔融,冷却后,将盐类溶解在滤液中。在原子吸收光谱上用氧化亚氮-乙炔火焰,于波长396.2nm处,测量溶液的吸光度。将测得的试液铝的吸光度与铝交准溶液的吸光度相比较,求得铝含量。
4、试剂和材料
分析中除另有说明外,仅使用认可的分析纯试剂和蒸留水或与其纯度相当的水,符合GB/T6682的规定。
4.1碳酸钠(Na2CO3),无水。
4.2盐酸(ρ1.19g/mL).
4.3硝酸(ρ1.4g/mL).
4.4氢氟酸(ρ1.13g/mL)。
4.5硫酸(ρ1.84g/mL)。
4.6盐酸(1+9),以盐酸(4.2)稀释。
4.7硫酸(1+1),以硫酸(4.5)稀释。
4.8铁基溶液:称取10g高纯铁[最小纯度(质量分数)99.9%,铝含量(质量分数)小于0.002%]溶解在50mL盐酸(4.2)中,逐滴加入硝酸(4.3)进行氧化。蒸发至浆状,加入20mL盐酸(4.2),用水稀释至200mL。在水中溶解17g碳酸钠(4.1),并加入到铁基溶液中。将混和溶液移入1000mL容量瓶中,用水稀释至刻度,混匀。
4.9铝标准溶液(0.5mg/mL):将0.5000g高纯铝[最小纯度(质量分数)99.9%]溶解于25mL盐酸(4.2)中,冷却后,移入1000mL容量瓶中,用水稀释至刻度,混匀。
5、仪 器
常用实验室仪器,包括单刻度容量瓶和单刻度移液管,分别符合GB/T12806和GB/T12808的规定。
5.1铂坩埚,30mL。
5.2高温炉,温度能保持在1100℃。
5.3原子吸收光谱仪,配有氧化亚氮-乙炔燃烧器,铝空习阴极灯。
在仪器最佳工作条件下,原子吸收光谱仪应达到下列指标:
a)最低灵敏度:铝校准溶液最高浓度的吸光度不小于0.3。
b)工作曲线的线性:用同样的方法测定时,工作曲线顶部20%与底部20%浓度范围的斜率值(给示为吸光度的变化)之比不应小于0.7。
c)最低稳定性:最高浓度校准溶液与零浓度校准溶液,经多次重复测定,吸光度的标准偏差与最高浓度校准溶液吸光度平均值之比应分别小于1.5%和0.5%。
注1:推荐使用纸带式记录仪或数据显示器来评价a)、b)、c)规范和下面所的测量。
注2:每台仪器的参数可能不同,下列参数可作为参考。
——铝空心阴极灯电流,10mA
——波长,396.2nm
——氧化亚氮流量,13.8L/min
——乙炔流量,6.6L/min
对上述气体流量不合适的系统,给出的气体流量比率仍可能是一个有用的参数。
6、取样和制样
6.1实验室试样
按照GB/T10322.1进行取制样。般试样粒度应小于100μm。如试样中化合水或易氧化物含量高时,其粒度应小于160μm。
6.2预干燥试样的制备
充分混匀实验室试样,缩分法取样。按照GB/T6730.1在105℃±2℃下干燥试样。
7、分析步骤
警告:为避免氧化亚氮-乙炔点火、熄火可能引起的爆炸性伤害,必须按照仪器说明书要求操作仪器。
按照附录A,对同一预干燥试样,至少独立测定两次。
注:“独立”是指再次及后续任何一次测定结果不受前面测定结果的影响。本分析方法中,此条件意味着同一操作者在不同的时间或不同操作者进行重复测定,包括采用适当的再校准。
7.2试料量
称取1.00g预干燥试样(6.2),精确至0.0002g。
注:称量试料应尽量快,以免试料再吸湿。
7.3空白试验和验证试验
7.3.1空白试验:随同试料分析做空白试验。
7.3.2验证试验:随同试料分析同类型标准样品做验证试验。
7.4测定
7.4.1试料的分解
将试料(7.2)置于250mL烧杯中,用少量水湿润,加入25mL盐酸(4.2),盖上表面皿,缓慢加热。升高温度,在近沸点下溶解,加入2mL硝酸(4.3),煮沸几分钟,稍微移开表面皿,在105℃~110℃的电热板上加热30min,将溶液蒸发近干。加入5mL盐酸()4.2,溶液盐类,加入50mL水后,加热煮沸。以水洗涤表面皿和烧杯壁,用含纸浆的中速滤纸过滤溶液,滤液放入250mL的烧杯中。用带橡皮头的玻璃棒擦烧杯,将粘附在烧杯壁上的颗粒物洗到滤纸上,用盐酸(4.6)洗涤3次,再用热水洗至滤纸上无三氯化铁的黄色为止。将滤纸和沉淀物移入铂坩埚,滤液蒸发至约100mL,保留。
7.4.2残渣处理
在500℃~800℃,灼烧残渣和滤纸,冷却,滴入几滴水湿润一下,加入3滴~4滴硫酸(4.7)和10mL氢氟酸(4.4),慢慢蒸发,除去硅。在700℃下灼烧残渣,向坩埚中加入1g碳酸钠(4.1),盖上坩埚盖,在高温炉(5.2)中熔融,直至融清。
注1:如果加入1g碳酸钠,试料熔融有困难,可加2g碳酸网段。这时,铁基溶液(4.8)制备也应用两倍量的碳酸钠和盐酸。
注2:一般高温炉熔融约在1100℃下15min.
7.4.3试验溶液的制备
将冷却的熔融物移入(7.4.1)保留的滤液中,溶解盐类,洗出坩埚和盖。
注:如果溶液混浊,表明有大量水解钛存在,在转入200mL容量瓶前,应过滤。
将溶液转入200mL容量瓶中,用水稀释至刻度,混匀。如果试样铝含量(质量分数)在0.1%~2.5%之间,此溶液可直接在原子吸收光谱仪上测定。如果试样铝含量(质量分数)在2.5%以上,从容量瓶中分取20.00mL试液到另一200mL容量瓶中,加入55mL铁基溶液(4.8),4.5mL盐酸(4.2),再用水稀释至刻度,混匀。此溶液为稀释的试液。
注:对于灵敏度较高的仪器,少的试液量可能更好。这种情况,铁基溶液(4.8)和盐酸(4.2)用量应调整。
空白试液也分取20.00mL至200mL容量瓶中,加入55mL铁基溶液(4.8)和4.5mL盐酸(4.2),以水稀释至刻度,混匀。
注:试液和空白试液一起测定,稀释的试液和稀释的空白试液一起测定。
7.4.4铝校准 溶液的制备
在6个200mL容量瓶中分别定量加入0mL、2.00mL、5.00mL、10.00mL、20.00mL、50.00mL铝标准溶液(4.9),稀释至约100mL,分别加入6mL盐酸(4.2)和60mL铁基溶液(4.8),然后以水稀释至200mL刻度,混匀。
7.4.5测量
按照仪器操作说明书,固定燃烧器,点燃火焰,于波长396.2nm处用铝含量最高浓度的校准溶液(7.4.4),调节气体流量和燃烧头,以得到最大吸光度,然后用水调零,按照浓度递增的顺序测量校准溶液和试液的吸光度。两次读数之间喷入水调零。
以铝校准溶液的吸光度扣除零含量铝校准溶液的吸光度,得到的净吸光度值 为纵坐标,铝含量为横坐标绘制工作曲线。在工作曲线上根据试液的吸光度扣除空白试液的吸光度得到净吸光度,求得试液铝含量。
8、结果计算
按式(1)计算试样中铝含量(质量分数)ω(A1),其数值以%表示:

式中 CA1——最终试液中的铝含量,μg/mL;
m——200mL最终试液中所含试料的质量,g.
8.2分析结果的一般处理
8.2.1重复性和允许差
本分析方法的皮革[密度由下列回归方程表示:
Rd=0.0290X+0.0230 ………………………………………(2)
P=0.0541X+0.0703 ………………………………………(3)
σd=0.0102X+0.0081 ………………………………………(4)
σL=0.0177x+0.241…………………………………………(5)
式中 X——预干燥试样的铝含量,以质量分数表示,计算如下:
——实验室内,按公式(2)和(4)计算,其为两次重复测定结果的算术平均值;
——实验室间,按公式(3)和(5)计算,其为两个实验室最终结果(8.2.5)的算术平均值。
σd——实验室内重复测定的标准偏差;
σL——实验室间的标准偏差;
Rd——实验室内重复测定的允许差(重复性);
P——实验室间的允许差。
8.2.2分析结果的确定
按照附录A中步骤,根据公式(1)计算独立重复测量结果,与重复测定允许差(Rd)进行比较,来确定分析结果。
8.2.3实验室间精密
实验室间精密度用以评价两个实验报告的最终结果之间的一致性。两个实验室按照8.2.2中规定的相同步骤报告结果,计算:

式中 μ1——实验室1报告的最终结果;
μ2——实验室2报告的最终结果;
μ3——最终结果的平均值。
如果︱μ1~μ2︱≤P(见8.2.1),最终结果是一致的。
8.2.4分析值的验收
分析值的验收使用认证准样品进行验证。步骤与以上所述相同。确认精密度后,实验室最终结果与标准值Ac比较。如:
a)︱μc~Ac︱≤C,测量值与标准值之间无显著差异。
b)︱μc~Ac︱>C,测量值与标准值、之间有显著差异。
式中 μc——标准样品的测量值;
Ac——标准样品的标准值;
C——该值取决于所使用标准样品的种类。
对通过实验室间确定的标准样品:
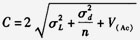
式中V(Ac)是标准值Ac的方差。
对仅有一个实验室确定的标准样品:

注:除非已确证该标准值没有偏差,否则不应采用此类标准样品。
8.2.5最终结果的计算
试样的最终结果是可能接受分析值的算术平均值,也可按附录A中的规定进行操作的,计算到小数点后第4位,并按下列方法修约到小数点后第2位;
a)当小数的第3位数小于5,舍去此数,第2位数字不变。
b)当小数的第3位数字是5,而第4位数字不0,或当小数的第3位数字比5大,第2位数字进1.
c)当小数的第3位数字是5,而第4位数字是0,舍去5,第2位数字是0、2、4、6、8时,保持不变,如果第2位数字是1、3、5、7、9,则进1.
8.3氧化物换算系数
氧化物公式如下:ω(Al2O3)[%]=1.8895ω(Al)[%]
9、试验报告
试验报告应包括下列信息:
a)测试实验室名称和地址;
b)试验报告发布日期;
c)本标准的编号;
d)试样本身必要的详细说明;
e)分析结果;
f)标准样品名称和结果;
g)测定过程中存在的任何异常特性和在本标准中没有规定的可能对试样或标准样品的分析结果产生影响的任何操作。
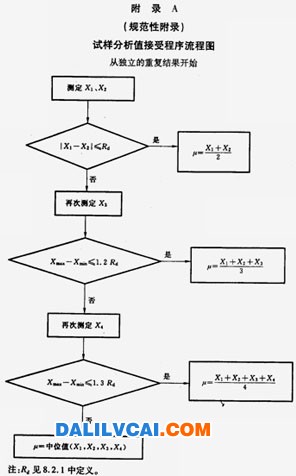
附录B
(资料性附录)
重复性和允许差公式推导
在8.2.1中的回归方程是于1971年~1973年,由12个国家38个实验室对6个铁矿石样品进行国际共同分析试验结果统计得到的。
附录C中给出了精密度数据的处理图。
用于试验的试样列于表B.1中。
表B.1 试样的铝含量
试样
|
铝含量(质量分数)/%
|
Canadian ore
Sweden-7ore
CSRore (Krivoi Rog)
Phillippine iron sand
Minette ore
72-8ore
|
0.18
0.28
0.89
1.47
2.13
4.14
|
注1:国际试验报告和结果的分析统计可在ISO/TTC102/SC2或ISO/TC102秘书处得到。
注2:统计分析按照ISO5725:1986,精密度测试方法——实验室内重复性和再现性测定标准方法的原理进行。
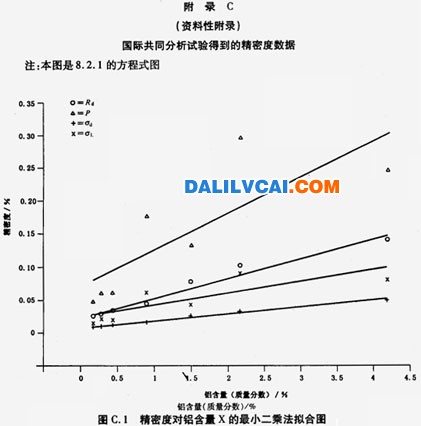