为了响应国家节能减排号召,进一步降低公司生产成本,保持设备安全、优质、经 济运行。针对我公司A5、A6两台时效炉在运行中存在温升曲线差、电耗和天然气消耗过大等问题,对时效炉能耗高的具体原因进行分析并进行节能降耗改造意义重大。时效炉能耗高的原因有很多,本文通过对我公司时效炉能耗高的主要原因进行分析,对时效炉在升温和保温阶段,循环风机的最佳转速控制进行深入研究,通过修改PLC程序和变频器参数,合理控制风机转速,达到节约能耗目的。
1、铝型材时效炉用途及结构简介。
1.1、设备用途。
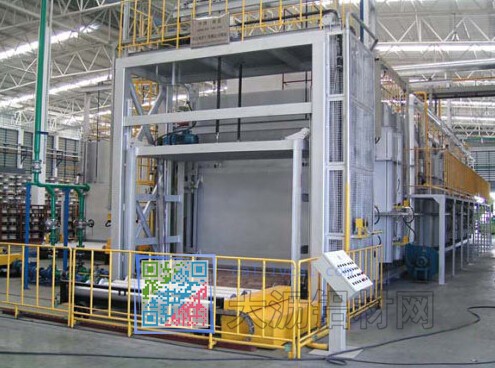
铝合金时效炉主要用于铝合金型材的时效处理。通过时效处理,可以使铝合金强度和硬度大幅度提高,同时可以减少铝合金材料的应力集中、变形等问题。
1.2、时效炉结构简介。 我公司时效炉主要由保温炉体、炉门装置、加热系统、热风循环系统、台车装置及电气控制系统等部分组成。 加热系统采用1台瑞典百通BG600燃气燃烧机,燃料为压缩天然气。为确保炉温均匀性,炉体顶部设75KW离心式循环风机1台,并合理配置炉内热风循环导流系统,使炉内气流分配均匀,炉内温差小,又保证了加热速度与加热质量。炉体采用内外两层钢板焊接而成的全金属形结构,中间均匀填充硅酸铝耐火纤维保温,降低炉壁温升。炉门采用电动式升降炉门,炉门压紧采用气动联杆式四点平衡压紧机构。台车牵引机构采用链条式。
1.3、温控系统 由触摸屏、S7-200PLC、四支热电偶、8通道无纸温度记录仪组成。升温温度、保温温度、升温时间、保温时间可分别在触摸屏上进行设置。 温度控制采用级联控制方式,即由4支温度热电偶采集的时效炉内温度信号送入PLC的闭环控制模块经冷端补偿,线性化处理,与触摸屏给定值一起经运算,其结果与炉温度热电偶采集的温度信号,再经PLC运算处理后,输出给燃气燃烧机,从而控制火焰大小,达到温度自动调节的目的。同时通过PLC程序控制模拟量输出模块,输出DC0-10V模拟量至变频器,变频器输出相应的频率来控制循环风机的转速,以改变炉内空气的对流速度,使炉内空气温度达到均匀化,完成铝型材时效的目的。
2、兴发铝业技改前时效炉设备的现状:
兴发铝业挤压车间A5、A6时效炉均由某公司制造,加热系统均采用1台BG600天然气燃烧机,目前我公司主要时效的型材为6061和6082,升温时间一般设定为1小时左右,保温时间一般设定为6.5-7.5小时。每台时效炉主要用电设备为75KW三相异步通风机1台,采用PLC+变频器自动控制风机的转速,厂家设计的风机转速控制程序为在风机换向时程序输出的频率为52.9HZ,不换向时输出频率为57.02HZ。平均每吨铝材时效耗电量为36KWh/吨。 天然气平均耗气量为10.3 m3 /吨。 我们通过多次温度在线测量(参考7.4项升温曲线图),发现在升温阶段各部位温差较大,在保温阶段曲线不够平直,证明该时效炉温度控制效果不理想。
3、时效炉能耗高的一般原因分析
由时效炉的结构可以看出,时效炉的能源消耗主要包括由于加热所产生的天然气消耗和75KW循环风机产生的电能消耗。
导致能耗高的可能原因分析如下:
3.1、时效炉炉体保温效果差。 当炉体保温效果差时,会使炉内热空气通过热传导辐射到炉周围空气中,这势必会造成升温速度慢,不能满足时效炉时效前期快速升温的要求,同时会造成燃烧机频繁启动、加热时间延长,造成不必要的天然气浪费。 3.2、炉门关闭不严。 炉门关闭不严同样会造成炉内能量的泄漏,增大天然气消耗。
3.3、燃烧机燃烧效率低。 燃烧机燃烧时,天然气和助燃风混合比例不合适,是造成燃烧机效率低的主要原因。天然气比例过小时燃烧机容易熄火,天然气比例大时,天然气燃烧不充分,未燃烧的天然气会通过排烟系统排出炉外,这样就会造成天然气的白白浪费,同时升温效果差。所以天然气和助燃风混合比例调整合适是减少天然气消耗的主要方法。燃烧机火焰长度一般以刚好出烧嘴口为宜,火焰形状为“毛笔”形,火焰根部应从枪口喷出,不能“脱火”,火焰颜色分里外两层,中间为淡蓝色,外层为淡红色,火焰应强劲有力。
3.4、天然气质量差、热值低。 天然气各组成成分主要包括辛烷、三甲基戊烷、甲苯、甲烷、已烷、丁烷等30多种成分。其中也包括二氧化碳、气态水、空气及一些惰性气体。天然气质量差会使天然气发热量降低,直接造成天然气能耗的增加。
3.5、排烟系统没有经过二次利用,直接排出炉外。 对烟气进行二次利用可以有效提高能量利用率,减少能源消耗。
3.6、一次装炉量过小、两次装炉时间间隔太长,时效炉整体利用率低。 时效炉装炉量过低时应适当缩短保温时间,保温时间的选择应根据铝型材的壁厚和装料的紧密程度来确定。这样既可以满足时效工艺,也可以有效降低天然气及电能的消耗。两次装炉间隔时间过长时,炉内温度已降低很多,开始时效时炉壁就会吸收一些热量以达到热平衡,造成天然气能耗的增加。
3.7、循环风机转速设置不合理。 我公司时效炉循环风机的功率为75KW ,采用变频器控制。我们知道电机的输出功率和转速的三次方成正比,即P∝n3。在满足工艺的前提下,如果电机转速设置过高就会造成电能的不必要浪费。因此,合理设置风机转速是减少电能损耗的有效措施。 时效炉能耗高的原因很多,各单位应根据时效炉的具体情况进行分析,采取有效措施,在满足时效工艺的前提下,尽可能降低天然气和电能消耗。
4、时效过程中风机转速不合理的后果
铝材时效过程一般分为升温和保温两个阶段,保温时间比升温时间一般要长。在升温阶
段,为了满足快速升温的要求,风机转速较高,以加快热空气对流速度,满足铝型材从常温升到180度左右温度,当然不同型号的铝型材升温温度有所不同。在保温阶段,随着时间的延长,铝型材各部分已充分被加热,炉内热空气温度和铝型材温度已基本达到热平衡,这时热空气的对流速度已不需要太快,否则,不合理的风机转速使热空气对流速度迅速增大,炉内温度迅速上升在短时间内超出保温温度,多余的热量会通过烟道排除炉外,这样不仅造成天然气的浪费而且风机转速高会造成风机电能消耗大,最终造成时效成本增高。所以对大功率时效炉风机转速的合理设置意义重大。
5、本次技改主要研究内容和实施步骤。
5.1、对我公司时效炉能耗高的主要原因进行客观分析。
5.2、通过对时效炉铝型材时效工艺的研究,理论确定升温和保温阶段风机运行的最佳转速,达到减少天然气和电能的不必要损耗。 5.3、对厂家PLC程序中关于风机控制子程序进行分析,确定程序的不合理之处。
5.4、修改PLC风机控制程序和变频器参数,并根据对时效炉温升曲线多次在线测量和时效后样品抗拉强度测定,计算并调整风机转速控制程序。 5.5、技改后,观察时效用电单耗和天然气单耗,得出节能降耗结果。
6、我公司时效炉能耗高的主要原因及解决方案
通过对第三项所列时效炉能耗高的主要原因进行对照,结合我公司时效炉的具体情况进行分析、查找,我公司时效炉能耗高的主要原因及解决方案论述如下:
6.1、两次时效间隔时间过长,时效炉连续利用率低。 针对此问题,我们主要通过合理安排时效炉开炉时间,尽量保证铝材时效量,尽可能缩短两炉之间间隔时间,保持时效炉运行的连续性。
6.2、在时效过程中循环风机转速设置不合理。 从技改前时效炉温升曲线图可以看出,在保温阶段,风机转速持续在50HZ以上显然不合理。这样高的转速不仅增大了电能消耗而且温升曲线在保温段波动较大,同时也增大了燃气消耗。 由n=60f/P*(1-s)可知,电机的转速与频率成正比,通过改变风机电机的运行频率即改变了电机的转速。 通过第四项的分析,结合我公司铝型材时效的具体情况,经过反复试验,以TT板为例,我们将风机频率控制分为三个阶段,在升温阶段通过PLC模拟量输出模块将变频器的频率控制在50HZ,进入保温段后的2小时30分内的频率控制在45.03HZ,其余时间设定为40HZ。修改程序后,完全能够满足时效工艺要求。同时由于变频器输出频率比技改前降低,所以风机消耗电功率也随之降低。 当然,由于每个厂家时效炉结构及工艺要求的不同,对时效过程中风机转速的控制不能一概而论,应结合时效铝型材的具体牌号、升温和保温时间等因素通过实验手段进行确定。
7、技改后时效效果及经济效益分析
通过对铝型材时效炉时效工艺和设备现状的研究、分析,找出能耗高的主要原因, 理论确定升温和保温阶段风机运行的最佳转速,在不改变设备现状的前提下,通过修改PLC程序,既充分满足时效工艺及时效效果而且有效降低了铝型材时效过程中天然气和电能的消耗,达到良好的节能效果。
7.1、时效炉技改前后的天然气和用电单耗对比。 我公司在技改前,铝材时效用电单耗为36KWh/T。技改后,铝型材时效电单耗为25.8KWh/T ,技改后平均每吨电单耗下降10KWh左右。 技改前,时效炉天然气平均单耗约为10.3m3 /T。技改后,时效炉天然气平均单耗为10.6 m3/T,技改后天然气平均单耗下降了0.7 m3 /T。
7.2、技改费用: 由于本次技改是通过对时效过程中控制程序和变频器的修改并通过测温来达到节能效果,所以本次技改无直接费用。