模具的工作条件是非常恶劣的,在高温、高压下承受剧烈的摩擦、磨损作用,根据现场生产统计数据显示模具的主要失效形式有三种:
(1)摩擦、磨损失效占65%,
(2)疲劳裂纹失效占18%,
(3)塑性变形塌陷失效占15%。
失效模具的判定依据为挤出制品不能达到产品标准要求且无法再修复,模具使用寿命一般用有效通料量来描述。
2 模具使用寿命的影响因素
2.1 合同品种与模具设计
(1)挤压系数与型材结构复杂程度。型材 截面积和结构复杂程度不同时模具使用寿命也不同。挤压系数Κ一般>7,当Κ=8~40使用寿命较长,Κ>70则难以挤压,使用寿命较短,品种的结构对模具寿命有重要影响,结构愈复杂,局部刚性不够,产生流速不均,并造成局部应力集中。流速不均,容易堵模和闷车或形成扭拧波浪,故结构复杂的模具有效寿命要短些,而结构对称、壁厚均匀、宽厚比相对较小者则寿命较长。
(2)壁厚和公差范围。从生产实际情况看,型材壁厚∆=1.3~1.4mm时使用寿命都较长,∆≤1mm时使用寿命大幅度降低。壁厚公差范围愈大,则使用次数愈多,使用寿命愈长;公差范围愈小,短期内易超过公差范围,造成过早磨损而报废。
(3)模具结构设计,型材的理论重心通常放在模子中心。当平面模中悬臂较大时,实际上把前支模和模子设计成整体结构,大大提高悬臂强度,降低了悬臂塑性变形和疲劳断裂倾向,在多数厂家都有成功应用。模孔距挤压筒边缘太小时,挤压筒内壁氧化物、夹渣易进入模孔而擦伤工作带,一般讲要大于15mm。模具设计时要充分处理好应力集中 的情况,结构原因造成的应力集中部位很可能是模具冷、热疲劳裂纹过早发生的部位。平面模尖角和分流模下模的工艺圆角R=0.3~0.5mm,分流桥断面形状尽量做成滴水 状,滴水状既可避免应力集中,又有利于金属流动,必要时要对空刀部位尺寸进行强度校核计算,其处理也尽可能呈梯形。
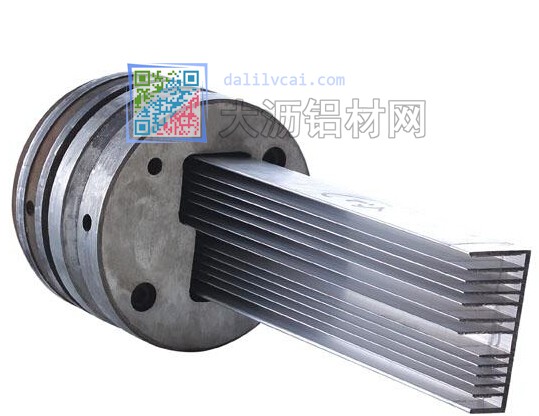
2.2 模具制造
(1)模具加工工艺的选择。
加工工艺主要 指毛坯锻造、电加工、标准装配、工作带加工和热处理。现场统计数据表明,锻造的毛坯比未锻造的寿命要提高30%。整体切割能改善工作带的表面质量,石墨电极比紫铜电极更能提高工作带和空刀的精度(二者综合,可使一次上机合格率提高20%)。用真空炉进行热处理,硬度均匀和变形小。大多数平面模都是前支模、模子、垫子三件进行装配,分流模本身是上下装配的结构。模子装配精度达不到要求,会使制品形位尺寸稳定性差,且经修理后又易发生变化。大多数模具都采用标准定位销定位,以减少位置误差,再配以紧固螺钉进行紧固定位,来解决装配精度问题。
(2)工序质量。
工序质量是对设计质量的保证,模具使用分析表明,产生波浪、弯曲、扭拧、扩并口等制品缺陷的60%是与工序质量有关,应对每道工序建立工序卡片,以便进行工序质量检验,尽量减少累积误差。
2.3 挤压工艺
(1)挤压锭坯尺寸。在挤压系数已定的条件下,挤压锭坯尺寸的选择是否合理与模具有效通料量有关。一般来讲,型材生产是按定尺组织生产和销售,应以定尺数量最多、几何废料最少确定锭坯尺寸。
(2)挤压温度。挤压温度由模具加热温度、挤压筒定温和锭坯加热温度来决定,锭坯加热温度过低则易闷车,而引起压力升高,使模具局部出现微量塑性变形,或在应力集中部位产生微裂纹,锭坯加热温度过高会使金属软化,而粘附于工作带表面甚至堵模(严重时模具在高压下崩塌)。
(3)挤压速度。
挤压时是放热反应,速度太快,摩擦加剧使磨损加速,也易堵模或制品表面粗糙,速度过慢使生产率下降,在保证质量的前提下应尽可能提高挤压速度。
2.4 挤压锭坯
合金成分的控制尤为重要,以6063为例,Mg2Si是控制型材力学性能的关键因素,一般情况下Mg2Si含量在0.65%~0.75%就可保证,应控制好Mg∶Si,我厂根据现场优化控制,取Mg∶Si=1.55~1.70。一般厂家要求铸锭晶粒度达一级标准,以增强塑性和减少各向异性,铸锭中若气孔多、组织疏松,有中心裂纹时,气体突然释放有时会形成“放炮”现象,使模具局部工作带突然减载又加载,形成巨大冲击载荷,对模具十分有害。
氧化物夹渣处于锭坯表面时会使工作带加剧磨损而早期失效。锭坯均匀化对提高模具寿命很有好处,在550~570℃保温8h后强制冷却,挤压时突破压力可降低10%左右,挤压速度可提高10%~20%,但是,多数厂家目前并未进均匀化处理。
2.5 模具的管理与正确使用
(1)模具的正确使用。包括严格的加热制度,正确的装配方式和合理的挤压根数,一般模具在420~450℃下保温2h都无问题,但若加热时间超过8h,会使氮化层硬度降低。模具使用时必须有合适的配套措施(如模支承、模垫、支承环等)。模具一次挤压次数的确定是为了保护模具,一般在80~150根为宜。
(2)碱洗。碱洗模具,首先为析氢反应,其次才为模具钢的腐蚀反应,一般地讲,不会发生后者的情况。不过,若NaOH浓度和温度过高时,两种情况都能发生,氢气可能导致氢脆腐蚀开裂,碱洗后应将Al(OH)3清理干净,以免热烧结形成硬块而影响工作带或制品。
(3)氮化。模具氮化可使寿命提高2.5倍以上(不氮化时,寿命为2~3t