拜耳法生产中经常用到苛性比、硅量指数、循环效率、晶种系数等概念。拜耳法就是用碱溶出铝土矿中的氧化铝。工业上把溶液中以NaAlO2和NaOH形式存在的Na2O叫做苛性碱(记作Na2Ok),以Na2CO3形式存在的Na2O叫做碳酸碱(记作Na2Oc),以Na2CO4形式存在的Na2O叫做硫酸碱(记作Na2O),所有形态的碱的总和称做全碱(记作Na2Ot)。
苛性比就是铝酸钠溶液中的Na2Ok与Al2O3的摩尔比,记作αko。美国习惯用铝酸钠溶液中的Al2O3与Na2Ok的质量比表示,符号A/N。
硅量指数指铝酸钠溶液中的Al2O3与SiO2含量的比,符号A/S。
循环效率指铝酸钠溶液中的1t Na2O在一次拜耳法循环中产出的Al2O3的量(t),用E表示。它表明碱的利用率的高低。
晶种系数(种子比)指添加晶种氢氧化铝中的Al2O3数量与分解原液中的Al2O3数量之比。
η=(1-αa/αm)×100%
式中 αa,αm-分别表示分解精液和分解母液的苛性比值。
拜耳法生产包括四个过程:(1)用αk=3.4的分解母液溶出铝土矿中的氧化铝,使溶出液的αk=1.6~1.5;(2)稀释溶出液,洗涤分离出精制铝酸溶液(精液);(3)精液加晶种分解;(4)分解母液蒸发浓缩至苛性碱的浓度达到溶出要求(230~280g/L)。拜耳法生产氧化铝的工艺流程如图1所示。
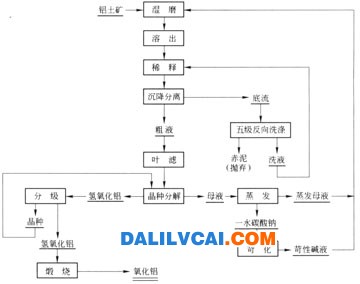
在这四个过程中,铝土矿的溶出是拜耳法的关键工序。铝土矿中的三水铝石在140℃就很快地溶入苛性碱液,一水软铝石在180℃也就很快地溶入苛性碱液,而一水硬铝石在240℃以上才较快地溶入苛性碱液,刚玉根本就不溶。为了使苛性碱溶液的温度达到溶出所需温度,就要用压力釜给苛性碱液加热。溶出氧化铝的浆液的温度和压力都很高,需要取出其所含的能量,采用自蒸法产出二次蒸汽来预热进入高压釜前的浆液,同时降低了溶出液的温度和压力,流出高压釜进入敞开容器洗涤、分离出铝酸钠精液。现代生产都是把一系列预热器、高压釜和自蒸发器串联为溶出器组织进行连续作业。浆液靠高压泵打入夺力釜,对于一水硬铝石需达到3.33MPa/cm2以上的压力。所以把高压溶出车间比喻为氧化铝生产过程的心脏。
拜耳法溶出时,为了减少结疤结瘤通常要进行脱硅,有在的原矿浆槽中于90℃以下的低温脱硅和在150℃下进行的中温脱硅,后者的脱硅效果较好,溶出液的硅量指数也较高。拜耳法溶液中Al2O3和SiO2浓度变化如图2所示。

拜耳法要求铝土矿中的Al2O3含量达55%以上,A/S越大越好。A/S从11降至7,生产成本将增加14.5%。我国的铝土矿大多为A/S=5~7(占所有矿的59.3%),拜耳法不能经济地处理。对这部分铝土矿就要用碱石灰烧结法来处理。
由均化堆场送来的铝土矿、石灰烧制工序送来的石灰,送入磨头仓。铝土矿、石灰和蒸发来的循环母液按一定配比进入由棒、球二段磨和水力旋流器组成的磨矿分级系统。水力旋流器溢流为合格原矿浆进入原矿浆槽。原矿浆经单套管预热器送入预脱硅槽经8小时预脱硅后补入适当的循环碱液,达到正常碱配比由GEHO隔膜泵送入压煮溶出多套管预热系统。
矿浆经GEHO隔膜泵送入四套管预热器,在压煮器内加热至250~260℃进行1小时溶出,溶出后矿浆经十一级自蒸发器闪蒸降温,溶出矿浆用赤泥洗液稀释。
稀释矿浆在常压脱硅槽进行4小时的常压脱硅。脱硅后的稀释矿浆在沉降槽内进行液固分离,底流进入洗涤沉降槽和深锥沉降槽组成的赤泥洗涤系统进行四次赤泥反向洗涤。制备好的絮凝剂经计量后分别加入分离和洗涤沉降槽,热水加入末次洗涤槽。末次洗涤槽底流经泵送到赤泥堆场进行堆存,一次洗涤沉降槽溢流送至压煮溶出稀释槽。
分离沉降槽溢流经泵送粗液槽,再用粗液泵送往立式叶滤机喂料槽,在槽中加入定量的石灰乳作为助滤剂。含助滤剂的粗液用泵送到立式叶滤机进行控制过滤,滤饼送分离洗涤沉降槽,精液送板式热交换器。
精液经三级板式热交换器与分解母液和冷却水进行热交换冷却到设定温度。降温后的精液与种子过滤滤饼(晶种)在晶种槽内混合,然后用晶种泵送至分解系列的首槽(1#或2#槽),经连续分解后从15#(或16#)槽顶用立式液下泵抽取分解浆液去进行旋流分级,分级前加入部分过滤母液稀释,分级溢流进15#(或16#)分解槽,底流再用部分母液冲稀后自压至产品过滤。分解末槽(14#或15#)的分解浆液从槽上部出料自流至立盘种子过滤机,滤饼用精液冲入晶种槽,滤液入锥形母液槽。
经分级底流的氢氧化铝浆液经饲料泵送入平盘过滤机进行成品过滤并用蒸发送来的热水进行洗涤。洗涤合格后的氢氧化铝送焙烧炉进行焙烧,生产出合格氧化铝。分离母液送种子过滤的锥形母液槽或分解槽末槽,氢氧化铝洗液送赤泥沉降一次洗涤系统或分解锥形母液槽,溢流槽浆液经泵送到分解末槽。母液槽内的分解母液部分送氢氧化铝分级用于稀释水旋器进料和底流,其余经板式热交换器与精液进行热交换后送蒸发原液槽。
蒸发原液除少部分不经蒸发直接送母液调配槽外,其余绝大部分在蒸发器组内进行蒸发浓缩后送调配。蒸发原液首先经Ⅰ闪蒸后分别进入Ⅳ效和Ⅴ效,其中经Ⅳ效-Ⅲ效-Ⅱ效-Ⅰ效-Ⅱ闪-强制效的形式进行浓缩作业。盐沉降槽溢流送到强碱槽(化清液),部分送各化学清洗用碱点和分解化学清洗槽,大部分返回与蒸发器Ⅴ效出料混合,通过出料泵送到母液槽;底流用过滤机进行过滤分离,滤液进盐沉降槽溢流槽,然后进强碱液槽。
生产过程中消耗的碱,用液体烧碱或者片碱补充。卸下的液碱或者片碱,先送补碱槽,再到母液调配槽与蒸发母液、部分不经蒸发的原液及苛化稀液调配成符合浓度要求的循环母液

