强化溶出新技术有:(1)管道化溶出;(2)单管预热-高压釜溶出;(3)管道化加热-停留罐溶出。
一、管道化溶出
管道化溶出就是“溶出过程在管道中进行,且热量通过管壁传给矿浆”的溶出。有单流法和多流法两种。德国采用单流法,匈牙利采用多流法。
1980年RA-6管道化溶出装置在Nab厂投产,采用图1所示的工艺流程。LWT表示原矿浆-溶出矿浆热交换管,外管Φ368mm,内装4根Φ100mm管,共长160mm。BWT(1~8)是溶出矿浆经八级自蒸发产生的二次蒸汽与原矿浆进行交换的管,有200×10=2000m。BWT(1~6)的外管直径为400mm,BWT(7~8)的则为508mm,内装4根Φ100mm管。E(1~8)为八级溶出矿浆自蒸发器,E(1~6)的规格为Φ2200mm×Φ4500mm,E(7)Φ2600mm×Φ4500mm,E(8)Φ2200mm×Φ4500mm。K(0~7)为八级冷凝水自蒸发器,K(0~3)的规格为Φ1000mm×Φ1400mm,K(4~6)Φ1400mm×Φ1800mm,K(7)Φ3300mm×5000mm。
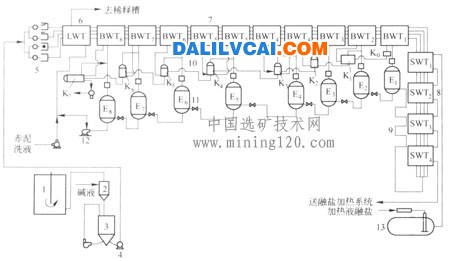
图1 RA-6管道化溶出流程
1-矿水槽;2、3-混合槽;4-泵;5-高压泵;6、8-管式加热器;
9-保温反应器;10-冷凝水自蒸发器;11-矿浆自蒸发器;12-泵;13-融盐槽
原矿浆经LWT管加热到90℃,在BWT管中加热到220℃,再往SWT管中加热到280℃,经反应器充分溶出后,到八级自蒸发和LWT换热系统降温后排出。RA-6管道化溶出装置还配有检测、控制和数据处理系统。管道化溶出技术在德国用于处理三水铝石型和一水软铝石型铝土矿。获得较好的经济指标。
1984年11~12月在Nab用RA-6装置对我国山西孝义一水硬铝石型铝土矿进行了工业试验。矿石成分(%):Al2O366.7,SiO212.27,Fe2O32.08,TiO22.74,CaO0.68,灼碱14.4。矿物组成(%):一水硬铝石68.2,高岭石24.9,针铁矿2.3锐钛矿2.6,金红石0.4,方解石0.7。工业生产用碱液为种分母液Na2Ok。浓度152.3g/L,苛性比2.76。要得到90%以上的氧化铝溶出率及1.50以下的溶出苛性比,就必须按以下要求操作:温度为280℃,时间为10min,添加CaO6%。原郑州铝厂于1990年购入Nab的RA-6型管道化溶出装置,用于处理铝硅比7.58的铝土矿。在原有保温反应管后串联Φ1200mm×Φ1200mm的6个停留罐,矿浆流量300m3/h,使氧化铝溶出率从69%提高到80%,每生产1t氧化铝的脱硅、溶出、蒸发的热耗由19GJ降至10.3GJ。
与RA-6管道化溶出过程不同,匈牙利采用多流管道化溶出装置,即碱液和预脱硅的矿浆分别用高压泵送入管式反应器中,先用高温矿浆产生的二次蒸汽加热至215℃,再用新蒸汽加热至溶出温度(240~260℃)。已加热的矿浆和碱液在混合管中合流充分溶出,之后进入多级自蒸发系统降温,排出反应器后进入稀释槽。匈牙利用这套装置处理一水软铝石型铝土矿(成分(%):Al2O350、SiO26.67、Fe2O322.8),氧化铝的溶出率为85%。所用的技术条件为:溶出温度248℃,矿浆流量120m3/h,Na2Ok浓度为200g/L,溶出液苛性比为1.44。匈牙利的多流管道化液出装置的主要问题是碱液结疤,后来也改为单流法。
二、单管预热-高压釜溶出
广西平果铝业公司从法国引起了单管预热-高压釜溶出技术,溶出系统流程如图2所示。固体含量300g/L的矿浆在Φ8000mm×Φ8000mm的矿浆槽加热至100℃,用高压橡胶隔膜泵送入五级长2400m的单管预热器(外管Φ336mm,内管Φ253mm),用后五级自蒸发器产生的蒸汽加热矿浆至155℃。随后进入中温脱硅器分段保温(同时也加热)停留20min脱硅,即到5台Φ2.8m×16m的加热高压釜,用前五级自蒸发器产生的蒸汽加热矿浆至200℃。再进入6台Φ2.8m×Φ16m的反应高压釜,用6MPa的新蒸汽加热矿浆至260℃。然后在3台Φ2.8m×Φ16m的终端高压釜中,保温反应45~60min。溶出矿浆经十级自蒸发降温到130℃以下,经缓冲现槽进入稀释槽稀释。加热高压釜和反应高压釜都配有机械搅拌及加热管束,终端高压釜只有机械搅拌装置。
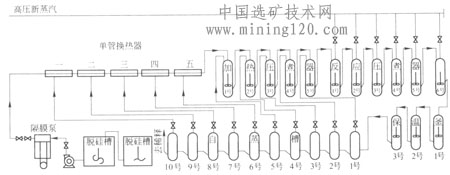
图2 广西平果铝业公司从法国引进的单管预热-高压釜溶出流程图
单管预热-高压釜溶出装置用于处理一水硬铝石型铝土矿,矿浆流量为450m3/h,设计年产氧化铝33万t。广西平果铝业公司用该设备于1998年生产38万t氧化铝。溶出液的αk为1.50,蒸发母液的Na2Ok浓度为230g/L,氧化铝的相对溶出率达91%。工业生产表明溶出效果好,存在的问题是磨损严重,需要定期频繁停产检修。
三、管道化加热-停留罐溶出
管道化加热时矿浆在管道内高速流动,雷诺系数Re达到105,处于高度湍流状态,传热系数达8000kJ/(m2·h·℃),比列管式热交换器高5倍,所需热交换面积减少。然而,对于一水硬铝石型铝土矿,即便溶出温度达310℃,若没有充足的停留时间,氧化铝的溶出率是很低的,管道化溶出的停出时间要延长,管道就会长得难以经济摆布。为此提出了管道化加热-停留罐溶出强化技术。
1988年广西平果铝业公司的铝土矿进行管道化加热-停留罐溶出的结果为:碱液浓度为Na2Ok230g/L,石灰添加量为7%~10%,管式反应器预热时间为10~12min,停留罐溶出时间为40min,氧化铝的相对溶出率达92%,溶出液的αk为1.50。管道化加热-停留罐溶出技术对我国其他矿的试验也收到良好效果。