一、冰晶石-氧化铝电解的工艺
现在全世界的铝都是电解冰晶石-氧化铝融盐生产的。生产流程如图1所示。
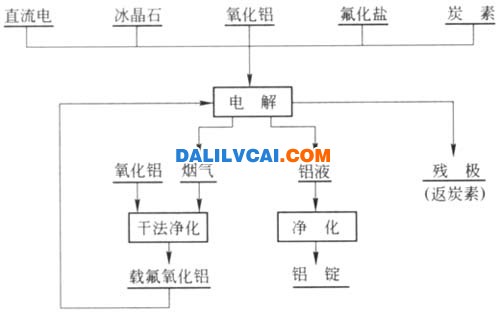
图1 现代铝电解工业生产流程图
电解铝的核心是电解槽,现代铝电解按电解槽的不同分为两大类两种形式,即连续式和不连续式预焙电解槽,上插棒和侧插棒自焙电解槽。
(一)不连续式预焙电解槽
不连续式预焙电解槽简称预焙槽,现代铝生产大多用这种槽。因为这种槽结构简单节约材料,有利于阳极气体的收集,能够大型化。大型预焙电解槽的电流强度已达320kA,电流效率达到92%,各项指标均较好。最近,法国开发成功500kA的超大型预焙阳极电解槽。预焙槽的结构主要为:阴极装置、阳极装置和导电母线系统三大部分。
阴极装置由钢制槽壳、阴极炭块组和保温材料砌体三部分组成。槽壳为钢板焊制的敞开式六面体,分为有底和无底槽壳,并有背撑式和摇篮式之分。目前大都采用有底槽壳,槽壳四周和底用工字钢加固。阴极炭块组包括阴极炭块和钢棒,钢棒镶嵌在阴极炭块的燕尾槽内,也是用高磷生铁浇铸,使铁棒与阴极炭块联在一起。阴极石墨炭块具有质地均匀,导电、导热性好等优点。保温砌体由耐火砖、保温砖砌筑。在槽壳中自下而上一般有两层石棉板,铺一层氧化铝粉,砌三层硅藻土保温砖、两层黏土砖,捣固一层炭糊,砌阴极炭块,阴极炭块间的立缝用炭糊填充。由槽壁内衬和槽底炭块围成的空间称为槽膛,一般深500~600mm。槽膛四周下部用炭糊捣固成斜坡,称为人工伸腿,以帮助铝液收缩于阳极投影区内。阴极装置中的阴极炭块部分能经得住融盐侵蚀的时间称为电解槽寿命,我国电解槽的寿命为1300d,国外分1800d。
阳极装置由阳极母线大梁、阳极炭块组和阳极升降机构组成。预焙槽有多个预制炭块组,每组包括3块预制阳极炭块。炭块、钢爪、铝导电杆组成阳极。钢爪用高磷生铁浇铸在炭碗中,与炭块紧密地粘接,铝导电杆采用渗铝块挂在大梁上。阳极母线大梁由铸铝制成,承担着整个阳极的质量,并将电流通过阳极输入电解槽。由升降装置带动上下移动来调整阳极的位置。预制阳极炭块组数由电解槽的电流强度、阳极电流密度及炭块尺寸来决定。加料可从边部或中部进行,根据加料多少和加料时间长短分为间隙加料和点式加料。
导电母线系统包括阳极母线、阴极母线、立柱母线和槽间连接母线,由大面积铸造铝板制作。导电母线系统最重要的是母线配置和母线经济电流密度的选择,前者取决于控制电解槽的磁场分布的要求,后者则由电能消耗和基建投资的优化结果所决定。母线配置有纵向和横向两种方式。现代大型电解槽采用横向配置,采用多端进电方式。
(二)连续式预焙电解槽
连续式预焙电解槽的特点是采用一种特制的炭糊将预制阳极块粘在即将耗尽的阳极上,炭糊在电解过程的高温下焦化,将新旧炭块结为一体。电流从侧部导入。它的优点是无残极,消除季换极时引起的电流分布不均匀;缺点是接缝处电阻大,阳极结构复杂,热损失大,经济指标低于不连续式预焙电解槽。
(三)侧插自焙电解槽
侧插自焙电解槽采用定向槽内添加阳极糊,阳极糊在电解过程的高温下焙烧成阳极锥体。电流从侧部插入的钢棒导入,通过阳极锥体到电解质。
侧插槽的阳极装置由阳极、阳极框架和阳极程式降机构组成。整个阳极的餐部安放在阳极框架中的铝板铆制成的箱内。在烧结成阳极锥体前钉入阳极棒,与水平面成20°角,共有四排,上面两排待烧结,下面两排工作,与阳极小母线连接导电。在电解过程中铝箱和阳极锥体一同消耗,阳极不断焦化,保持锥体稳定。阳极框架由槽钢和钢板焊成,框在铝箱外围。它的下部有U形吊环套住阳极棒头使阳极能够随它一起升降。阳极框架有滑轮组,通过钢丝绳悬挂在阳极升降机上。它除能升降阳极外,还能使之经得住液体炭糊的膨胀作用,保护铝箱不变形。阳极升降机构由电机、减速器、滑轮组构成,它在必要时升降阳极。
侧插自焙槽虽有省去了阳极炭块的低烧工序,没有残极处理,简化了工艺流程,使后产成本大大降低,投资小、见效快的特点,但它有烟气收集困难,环境污染问题不易解决,受阳极尺寸的限制,不能大型化,直流电耗较高,不易实现生产过程自动化等问题。最近,我国政府已明令限制自焙槽的发展。
(四)上插自焙电解槽
上插自焙电解槽由炭阳极、阳极框套、集气罩、阳极气体燃烧器和阳极升降机构组成。炭阳极也是由阳极糊连续自焙而成,阳极棒垂直插入到阳极锥体内,拔棒时留下的棒孔要由上层液体糊填补,形成二次阳极,阳极糊的流动性稍大。阳极棒是通过爆炸焊接在导电铝杆上的钢棒,钢棒插入炭阳极,插入深度按四个水平面配置。铝导电杆用夹具和阳极母线大梁紧接。在烧结成阳极锥体前钉入阳极棒待烧结成后才能使用。阳极棒既导电,又承担整个阳极的重量。炭阳极的我围为阳极框套,用10mm钢板焊成并用型钢加固。框套下四周装有集气罩,延伸到面壳上的氧化铝层,将壳上部空间密闭起来。阳极气体汇集于集气罩内,至燃烧器燃烧,送去净化。阳极升降机构用来升降阳极框套。
现代铝工业采用180kA、200kA、300kA系列的大型预焙阳极电解槽,采用两端进电或四端进电方式。进入21世纪后,法国彼施涅(Pechiney)公司开发成功500kA特大型电解槽,各项指标大幅提高,标志着世界铝工业进入了一个新的发展时期。
二、电解电解铝生产的正常生产
铝电解槽在焙烧、启动后转入正常生产,即在额定的电流强度下进行稳定生产;所有各项技术参数也都达到设计要求,并获良好的技术经济指标-主要包括电流耗、效率及原铝的质量等。
处于正常生产状态的电解槽的外观特征有:(1)火焰从火眼强劲有力地喷出,火焰的颜色为浅紫色或稍微带黄色;(2)槽电压稳定,或在一个很窄的范围内波动;(3)阳极四周电解质“沸腾”均匀;(4)炭渣分离良好,电解质清澈透亮;(5)槽面上有完整的结壳,且疏松好打。
正常生产的电解槽具有“规整的槽膛”。电解槽内在侧部炭块旁边沉积有一圈由电解质熔体凝固的结壳(又称为槽帮和伸腿),它周围在阳极四周形成一个近似椭圆形的槽膛。这层结壳能够有效地阻止电和热通过侧壁损失,保护侧壁和槽底四周的内衬不受熔体的侵蚀,并且使铝镜面(即阴极表面)收缩以提高电流效率。在电解过程中尽量努力维持槽膛的规整。在生产时槽底应该是干净的,无氧化铝沉淀,或只有少量氧化铝沉淀。
正常生产是铝电解槽高产、优质、低消耗的保证,而维持正常生产则取决于合理的技术条件及与之相适应的操作制度。否则生产就不能维持正常,出现病槽和事故,使各项技术指标下降。
(一)电解铝生产的工艺条件
正常生产的技术条件主要包括:系列电流强度、槽电压、槽电压、电解温度、极距、电解质组成、电解质水平(即结壳下熔体层高度)、铝水平(即槽内铝液高度)、槽底电压降以及阳极效应系数等。这些因素(或技术操作参数)都是相互影响、相互关联的。在一定时期内应尽可能保持相对稳定,一旦因某种原因需要变动时,就必须相应地调整其他参数与之协调。
正常生产的技术条件根据铝电解原理和具体情况而制定。表1列举了一些电解槽的技术条件。
表1 工业电解槽技术条件举例
技术条件
|
预 焙 槽
|
连续预焙槽
|
||||
电流强度/kA
阳极电流密度/A·cm-2
电解温度/℃
电解质摩尔比
w(CaF2)/%
w(MgF2)/%
槽电压/V
极距/cm
电解质水平/cm
铝水平/cm
槽底电压降/mV
阳极效应系数/次·(槽·d)-1
电流效率/%
直流电耗/kW·h·t-1
|
130
0.72
960
2.7
2~3
-
3.9
4.2
16
26
340
0.9
88
13700
|
160
0.75
950
2.5
2~8
4~5
4.0
4.1
16
25
320
0.3
90.5
13500
|
186
0.8
960
2.6
2~6
4~5
4.0
4.2
16
26
320
0.4
92.0
13500
|
300
950~960
2.2
94
13400
|
500
940~950
2.2
0.04~0.05
94
13200
|
110
0.82~0.85
960
2.75
4~6
-
4.1
4~4.5
22
26
-
1.0
87
15500
|
(二)电解铝生产的常规作业
无论是自焙槽还是预焙槽,铝电解槽的常规作业的主要内容包括:加料(称为加工)、出铝和阳极工作三个部分,具体的内容依槽的不同而有所不同。
1、加料。铝电解的加料作业就是定时地向电解槽中补加氧化铝,新型电解槽采用所谓连续或点式下料,就是每次下料之间的时间有严格规定,连续下料的时间间隙为20s,点式下料为每几分钟加一次。
下料的目的在于保持电解质中Al2O3浓度稳定。电解质溶体中Al2O3含量一般为58%。大型预焙槽采用连续下料或点式下料后,Al2O3的浓度差只有2%~3%。因为保持低的Al2O3浓度电流效率可达94%。也使加入的Al2O3迅速溶解,保持槽底无沉淀,对提高电流效率是有好处的。大型电解槽的下料大都是借助于电子计算机自动控制,下料部位可以在边部,也可在炭块中间。后者更为优越,无须打开槽罩,为现代大型电解槽所采用。间断加料作业过程是由天
车联合机组或地面龙门式联合机组来完成的。中小型电解槽用地爬式打壳机作业。
铝电解的加工作业程序是先扒开在面上预热的氧化铝料层,再打开壳面,将氧化铝推入熔体,然后往新凝固的结壳在上添加一批氧化铝,不许将冷料氧化铝直接加入电解质中。我国铝电解生产中总结了“勤加工、少下料”的操作方法,对中型槽实现稳定高产行之有效。铝电解的作业除补充氧化铝外,通常要随时调整电解质组成,补充挥发掉的氟盐和添加剂,调整电解质的摩尔比。每天需取样分析电解质的成分,决定补加的量。添加的氟盐要和氧化铝混合均匀,铺到壳上预热,上面加氧化铝覆盖,加料时加入。
2、出铝。电解产出的铝液要定期、定量从槽中取出。每两次出铝之间的时间称为铝周期。中型槽一两天出一次,大型槽每天出一次,每次出铝量大约等于在此周期内的铝产量。出铝用真空抬包来完成。抽出的铝液运往铸造部门。铝经过溶液净化、质量调配、扒渣澄清等处理后,铸成各种形状的铝锭。工业电解槽取出的铝液含金属杂质(Si、Fe、Ti、V等)、非金属杂质(Al2O3、炭和碳化物),还含气体。必须除去这些杂质,达到用户的要求。铝液净化的方法有静置法和连续溶剂净化法。静置法就是在尽可能低的温度下长时间静置,让铝液中的氢随温度的降低而溶解度降低,排出铝液。非金属杂质在这个过程中也浮出铝液而除去。
3、阳极作业。阳极是电解槽的核心,它的管理工作十分重要。自焙阳极在电解过程中是借助于电解高温把阳极糊焙烧成阳极的。它在电解过程中参与反应而不断消耗,阳极工作的主要任务是补充阳极糊和转接阳极母线(上插槽无此工作)。先拔出快要接触电解质熔体的阳极棒,将小母线转接到已经进入阳极锥体的阳极棒上,然后将阳极棒钉入快要焙烧成锥体的阳极糊中(称为钉棒)。这样当糊体焙烧成锥体时,钉入的棒便可与之保持最好的接触,保证导电均匀。阳极工作应保持阳极均匀地焙烧。阳极工作完毕后,要保持阳极不倾斜、在电解过程中不氧化、不掉块、无断层和裂缝现象。预焙阳极的作业是:定期按照一定顺序更换阳极块,以保持新旧阳极能均匀的分担电流,保证阳极大梁不倾斜;阳极更换后必须用氧化铝覆盖好;随着电解的进行,阳极要不断放低,当达到不能再放低时就要抬起阳极母线大梁。
(三)铝厂烟气净化
铝电解过程中放出的烟气有气态物和固态物。正常电解放出的气体是CO和CO2混合气体及少量的氟化物气体,阳极效应时产生CF4。自焙槽在烧结时产生沥青烟挥发分,气体污染物占90%,预焙槽气体污染物占50%,见表2。污染物主要是H2F2含氟气体。铝电解时产生阳极气体,它含H2F2、SiF4、CF4、CO2等,还有沥青挥分及各种粉尘,使电解厂周围环境受到危害,威胁操作人员的健康。因此铝厂烟气应得到合理的处理。烟气净化有干法和湿法两种。
表2 铝电解槽的污染物散发量 [kg/t(Al)]
槽 型
|
气态氟化物
|
固态氟化物
|
固、气氟总量
|
粉尘总量
|
上插槽
侧插槽
预焙槽
|
15.45
14.64
8.33
|
4.05
-
8.43
|
19.5
17.8
16.8
|
24.0
49.7
44.1
|
湿法净化是用水或碱溶液作为H2F2和粉尘的吸收剂来净化烟气。通常用5%的碳酸钠溶液来洗涤含氟气体,即发生反应:
2Na2CO3+H2F2→2NaF+2NaHCO3
当溶液中的NaF含量达到25~30g/L后,就可以用来合成冰晶石:
6NaF+4NaHCO3+NaAlO2→Na3AlF6↓+4Na2CO3+2H2O
冰晶石经分离、干燥后返回电解槽使用。滤液返回吸收塔吸收含氟气体,整个过程物料可以循环使用。流程如图2所示。

图2 铝电解槽烟气湿法净化工艺流程图
对于自焙槽的烟气,因含有沥青烟,净化困难,多数厂家仅作收尘和除焦油处理。湿法净化在20世纪70年代是净化铝厂烟气的主要方法。这一方法虽然净化了烟气,却又产生了废水,还需净化,投资大、运行费用高,现已为干法净化所代替。
干法净化就是用铝电解槽的原料氧化铝作为吸收剂,吸附烟气中的HF气,并截留烟气中的粉尘,吸收了氟化氢的氧化铝作为原料加到电解槽中。
我国贵州铝厂采用干法净化,进入净化装置前含气态氟化物5.7mg/m3,固态氟化物为7.3mg/m3,经过净化后烟气中的氟化物分别为0.12mg/m3和0.08mg/m3,净化率达98%。
干式净化法具有流程短,设备简单,净化效率高,截留下来的氟又返回电解槽,节约一氟盐,为大型预焙电解槽普遍采用。干法净化的主要缺点是烟气中的杂质又返回电解槽,影响电铝的质量和影响电流效率。