摘 要 综述了铸造铝合金熔体洁净度-疏松-力学性能三者之间的关系。指出溶解的氢和非金属夹杂通过与疏松的交互作用,对铸件的力学性能和可靠性产生极大损害。因此提高熔体洁净度水平已成为生产高质量铝铸件的关键。目前熔体洁净度-性能关系的研究以及与相应的熔体洁净度在线评定标准还有待深入探讨。
关键词:铝合金 熔体洁净度 疏松 力学性能
Melt Purity-Property Relationships in Casting Aluminum Alloys
Shu Da Sun Baode Wang Jun Li Tianxiao Xu Zhenming Zhou Yaohe
(Shanghai Jiaotong University)
ABSTRACT:Melt Purity-porosity-mechanical properties relationships in casting aluminum alloys have been reviewed in this paper.Interacting with porosity,dissolved hydrogen and non-metallic inclusions greatly impair both mechanical properties and reliability of castings.Accordingly,improving melt purified level is essential to produce high quality products.At present,melt purity-property relationships as well as on-line evaluation standards of melt purity still need further study.
Key Words:Aluminum Alloys,Melt Parity,Porosity,Mechanical Properties
近年来铝合金铸造有较大的发展,主要由于它的两个大市场——汽车制造业和航空航天工业的需要。扩大铝铸件在汽车,尤其是航空结构上应用的障碍是它的“不可靠性”[1]。同一个零件,不同的厂或同一个厂的不同炉次,甚至同一个厂同一个炉次浇出的铸件在性能上都存在较大差异。造成铝铸件不可靠性的主要根源在于目前绝大多数铸件都易于产生疏松(Porosity)这一影响微结构完整性的缺陷[2]。
洁净的液态金属是获得优质铸件的保证和前提。污染铝合金的杂质主要有三类:溶解的氢,非金属夹杂和不需要的碱或碱土金属。近年来的研究表明,氢与夹杂和疏松之间存在极强的交互作用,并对铸件的力学性能和可靠性产生较大损害。虽然人们早就意识到其重要性,但熔体洁净度到底对性能有多大影响,亦即洁净度-性能关系往往不甚明确。本文的目的即是就洁净度-疏松-性能关系作一综述。需要指出的是,本文所引绝大部分文献均以Al-Si合金(如356,318)为研究对象,这类合金因其良好的铸造性能、力学性能和抗腐蚀性能已成为铸造铝合金中应用最广的一类。
1 铸造铝合金的洁净度
铝合金的洁净度主要由溶解的氢和非金属夹杂决定。氢是唯一大量溶于铝熔体中的气体[3]。氢几乎不溶于固态铝,而在液态铝中的溶解度很大,并随温度的升高而增长。氢在固相线上下的溶解度分别为每100 g铝液氢含量0.65 mL和0.034 mL(H2在0.1 MPa的条件下),而每100 g溶融铝中正常的氢含量约为0.10~0.40 mL。
夹杂一般是指存在于液相线温度以上的任何固相或液相的外生杂质[4,5]。铝合金中常见的非金属夹杂有氧化物、碳化物、氮化物、硼化物等,大都以颗粒状或膜状存在,典型的颗粒尺寸在1~30 μm范围内[6]。此外,在高合金熔体中还会出现一些不希望有的初生金属间化合物,如Al3Zr,Al3Ti等[7]。含Fe的铝合金可能会形成多种富Fe的金属间化合物,如α-Al15Fe3Si2,β-Al5FeSi,δ-Al4FeSi2,π-Al8Mg3FeSi6等[8]。
虽然一般铝合金熔体中夹杂的浓度相对较低,在未处理的熔体中体积分数约为0.005%~0.020%,但夹杂的数量却是一个不小的数字。假如夹杂的平均尺寸为40 μm,那么即使是1×10-4%的夹杂浓度也意味着每1 kg熔体中包含有约1.1万个颗粒[9]。
2 洁净度-疏松关系
铝合金铸件中的疏松可以分为两种:宏观疏松和显微疏松。合适的冒口设计可以避免宏观疏松,但对于发生在枝晶间区域内的显微疏松却不是很有效。一般认为,疏松的形成是凝固收缩和氢的析出共同作用的结果[10,11]。影响疏松的因素很多,如图1所示。但很多研究者认为,氢含量是所有相关因素中最具决定性的一个[12~15]。
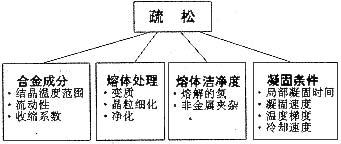
图1 影响疏松的因素
Fig 1 Factor related to porosity
Zhou等[16]的研究结果表明,孔隙度与冷却速度成反比,而与初始的氢含量成正比,如图2所示。当冷却速度大于5 ℃/s时,则主要由氢的浓度所决定。
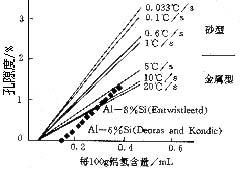
图2 孔隙度与氢含量和冷却速度的关系
(图中列出了其它作者的试验结果以示比较)[16]
Fig.2 Porosity as a function of hydrogen content and
cooling rate(Experimental data of others are shown for comparison)
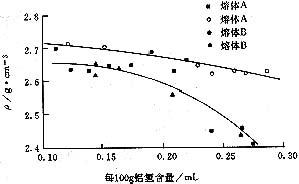
图3 氧化物夹杂对疏松的影响(Na变质319合金)
氧浓度:熔体A(7~19)×10-4%;熔体B(50~180)×10-4)%[19]
Fig.3 Efects of oxides on porosity (Na-modified 319 alloy)
Oxygen analysis:Metal A(7~19)×10-4)%;Metal B(50~180)×10-4%
Kao等[17]也认为,当G0.38/Vs1.62>0.6K0.4s1.6/mm2时,疏松量仅取决于氢的含量而与温度指标无关,其中G为温度梯度,Vs为凝固速度。
Fang等[18]指出,对应一定的冷却速度存在一个临界的氢含量,在此浓度时形成一定残余体积分数的气孔,且临界氢含量随冷却速度的提高而增大。但文献[16]指出,当每100 g铝熔体中氢含量小于0.05 mL时,冷却速度快慢对氢含量没有影响,此时基本上可以避免疏松的形成。
然而氢并不是一个独立存在的因素。文献[12]指出,当氢作为一个交互因素时,其对疏松的影响强烈依赖于其他因素。夹杂(尤其是氧化物夹杂)就是一个十分典型的例子。即使是少量夹杂的存在,也能显著降低形成气孔的临界浓度值[12]。另一方面,在“无夹杂”(或夹杂含量极低)的情况下,形成气孔的临界氢浓度值可以高达每100 g铝含氢0.3 mL[3]。Laslaz等[19]的研究表明,在相同的氢含量下,当熔体通过搅拌或加入废屑加剧氧化时,孔隙度显著增加(图2)。夹杂的存在不仅增多气孔的数量,而且还增大气孔的尺寸。Tynelius等[12]的统计分析表明,最大气孔尺寸可以增大3倍。
Sr作为变质剂由于有效作用时间长、提高铸件性能明显而优于Na。但Sr变质铸件产生疏松的倾向极大[20]。尽管这一现象的机制仍在研究之中,但有不少研究者认为熔体中的氧化物夹杂应是主要因素[21,22]。
夹杂对疏松的影响可由气孔的异质形核机制来解释。Campbell的计算表明,气孔在液态金属中的均质形核需要约3 080 MPa的气体分压。而Chen等[23]利用减压试验测得的数据表明,形成第一个气泡只需要很小的过饱和压力,通常为0.1 kPa左右(减压室真空度为1~20 kPa)。这证实了实际铝合金中的气孔成核均是异质形核。大量实践证实,夹杂尤其是氧化物夹杂可以作为气孔形核的有效基底。这是因为氧化物夹杂与铝熔体的润湿性较差(随温度不同,润湿角为115°~167°[23]),另外氧化物含有大量微孔和裂纹,这对气孔形核非常有利。Roy等[24]的观察表明,针状的β-Al5FeSi是非常活跃的气孔形核基底;晶粒细化剂颗粒也是气孔形核的合适基底,其结果是产生分布均匀的微小气孔。
目前关于夹杂在气孔异质形核中的作用机制问题仍在研究之中。Mohanty等[25,26]认为,只有那些为移动的液/固界面所推移的夹杂才可以成为气孔的异质形核基底,而那些被液/固界面捕获的夹杂则对气孔形成没有影响。夹杂成为异质核心的热力学可能性由夹杂、固相和液相之间的净界面能Δσ0=σps-σpl(σps,σp1分别为夹杂与固相、液相之间的界面能)所决定,并与夹杂的形状、大小、密度、热导率以及凝固条件有关。相同的夹杂在不同条件下可以表现出完全不同的行为,如Al2O3,SiC在亚共晶Al-Si合金中可以作为气孔核心,而在过共晶Al-Si合金中则对气孔形成不起作用。由此可见,夹杂在疏松形成中的行为表现出很大的“不确定性”。正由于此,使得铸件中的气孔密度(单位面积上的气孔数目)很难预测[12]。
尽管目前已出现一些定量检测铝熔体中夹杂的方法,如Alcan公司开发的LiMCA和PoDFA等,但由于存在取样代表性的问题,并有可能在检测过程中引入新的氧化物夹杂[27],因此检测结果未必能忠实地反映熔体中夹杂的分布与浓度。另外,由于准确控制熔体中所有夹杂的含量、性质和尺寸十分困难,因此通过试验定量研究夹杂与疏松的关系仍是一个难题[19]。
3 疏松-力学性能关系
力学性能主要由合金成分以及热处理工艺所决定,但铸件结构的完整性也有较大影响。疏松对力学性能的损害是公认的事实。Lee等[28]在研究A206-T6合金(Al-4.5Cu-0.35Mn-0.25Mg)板铸件的补缩特性和力学性能时,通过回归得出抗拉强度与微结构的关系可以表示为
σb=282.03(P)-0.14(D)-0.055 (4)
式中 σb——抗拉强度,MPa
P——孔隙度,%
D——代表枝晶单元尺寸,mm
上式中孔隙度的指数约是枝晶单元尺寸指数的3倍,表明疏松对抗拉强度的影响大于晶粒尺寸。
Eady和Smith[29]研究了Al-7Si(CP601-T6)合金疏松对拉伸性能的影响。总的来看,抗拉强度、屈服强度和伸长率都随疏松的增加而降低,但疏松对屈服强度的影响不很明显(图4),而对塑性的损害则极大。关于气孔形状,他们得出的结论是:气孔形状(球形或狭长形)对拉伸性能没有明显影响。
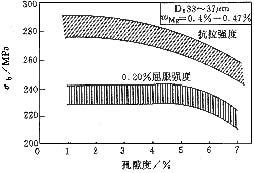
图4 CP601型合金疏松与应力的关系[29]
Fig.4 Relationship between porosity and tensile strength for CP601-type alloys
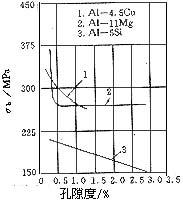
图5 三种铝合金砂型试样的抗拉强度与疏松的关系[4]
Fig.5 Ultimate tensile strength versus porosity for sand-cast bars of three aluminum alloys
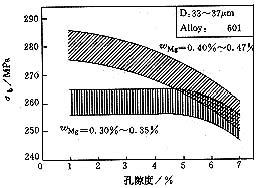
图6 CP160合金Mg含量对疏松-抗拉强度关系的影响[29]
Fig.6 Influence of Mg content on the relationship between percent porosity and tensile strength for CP601-type alloys
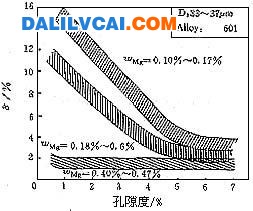
图7 CP601合金Mg含量对疏松-伸长率关系的影响[29]
Fig.7 Influence of Mg Content on the relationship between
porosity and elongation for CP601 alloys
疲劳性能对于汽车和航空结构件十分重要。Stucky等[31]认为微结构对疲劳极限影响不大,而疏松则是重要的变化因素。Verdu等[32]的研究指出,Al-Si合金的疲劳失效过程可以划分为三个阶段,即(1)在靠近表面的孔隙 处产生裂纹,(2)裂纹在枝晶间缓慢生长,(3)裂纹穿过共晶的快速生长。显然,疏松作为裂纹源对疲劳极限具有重要影响。而Major[33]则指出最大气孔尺寸是其中最重要的参数。
LaOrchan等[20]研究了A356合金的抗冲击性能,指出冲击功主要受Si形态的影响,而受疏松的影响不大,给出的相应关系式为:
E=-2.2×V 12.8 (Sr变质) (4)
E=-1.4×V 7.3 (无Sr变质) (5)
式中 E——冲击功,J
V——气孔体积分数,%
4 熔体洁净度-性能关系
由前所述,熔体中的氢和夹杂与疏松之间存在极强的交互作用,并对铸件的力学性能和可靠性产生损害。由于氢的含量是形成疏松的决定性因素,因此除气是熔体处理中的一项重要任务。Sigworth等[34]根据实践经验提出,高质量金属型汽车铸件要求100 g铝中氢的浓度在0.07~0.10 mL之间,航空件或熔模型铸件要求更高(每100 g铝中低于0.06 mL)。
非金属夹杂不仅促进疏松的形成,还起应力集中作用,引起零件早期失效,而且其本身也会造成铸件塑性和韧性的下降,典型的如针状β-Al5FeSi相。金属间化合物相的出现导致加工性能和表面光洁度的恶化,也是一个较突出的问题。
由于氢和夹杂物的存在给铸件的性能带来直接和间接的损害,因此,提高熔体洁净度水平已成为生产高质量铝铸件的关键。这就大大促进了近年来铝熔体净化技术的不断发展,如旋转叶轮法、喷射熔剂法、电磁分离非金属夹杂等。
目前,尚没有将熔体洁净度水平(氢与夹杂)与力学性能直接联系起来的研究报道。但美国正在开展这方面的工作。定量研究熔体洁净度-性能关系的目的是试图建立一种在线检测的标准,使得操作者能根据得到的熔体洁净度的信息,在浇铸之前调整对熔体处理的措施,以保证获得预计的性能和可靠性水平。但到目前为止,还没有一个严密的熔体洁净度的定义和可行的熔体洁净度评定方法[35],以控制疏松为目的进行的熔体氧化物或非金属夹杂水平检测的标准也未建立[3]。现有的评定方法存在以下一些主要缺点:
(1) 没有建立试样孔隙度与夹杂水平的对应关系:
(2) 没有建立试样孔隙度与熔体洁净度(含氢量与夹杂水平)的关系;
(3) 没有建立上述两项的关系对试样参数所作的规定。
5 结 论
(1) 氢是导致疏松形成的最主要因素;
(2) 非金属夹杂可以成为气孔的异质心核,促进疏松的形成,由于其行为的“不确定性”是导致疏松变化较大的重要因素,严重损害铸件的可靠性;
(3) 氢和夹杂通过与疏松的交互作用对铸件的力学性能产生极大损害,提高熔体洁净度水平已成为生产高质量铝铸件的关键;
(4) 目前熔体洁净度-性能关系的研究以及与之相应的熔体洁净度在线评定标准还有待深入探讨。
* 国家自然科学基金资助项目,批准号:59871029
作者简介:疏达,男,1973年出生,研究生,上海交通大学材料学院,上海华山路1954号(200030)
作者单位:上海交通大学