1、概述
随着铝型材行业的快速发展,特别是隔热断桥型材的节能环保等特点越发被广大用户追捧,普遍用在建筑门窗上,这些好的特性已经得到了证明。现在对隔热型材的要求已经不仅仅是使用在建筑门窗上了,对它的应用范围得到了进一步扩大。
最近我国轨道客车行业的蓬勃发展以及对节能环保的迫切要求,逐渐认识到隔热型材的诸多特点更符合这样的要求。现在的轨道客车上已经开始普遍采用,这给隔热型材的需求又开阔了一片新的应用领域。我们主要探讨一下我公司生产用于轨道客车的隔热型材的一些经验。对于轨道客车上用的隔热型材国家没有规定专门的标准,我们只能够采用用于建筑铝型材标准中的GB 5237.6-2004这个标准作为参考依据。标准规定抗剪性能是建筑铝合金隔热型材重要的性能之一。我国发布的GB 5237.6-2004《铝合金建筑型材第6部分:隔热型材》,本标准参照欧洲prEN14024:2000《隔热金属型材性能要求和测试试验》的要求规定隔热型材纵向抗剪特征值应≥24N/mm。
铝型材时效是指:时效,指在一定时期内能够发生的效用;铝合金在一定温度下(分为自然时效和人工时效),保持一段时间,由于过饱和固溶体脱溶和晶格沉淀而使强度逐渐升高的现象。
2、试验条件与目的
交通运输行业的客户委托我们公司研究生产用于轨道交通车辆上的先由我公司将穿条复合后的型材交给客户,客户再加工成半成品后进行人工时效的特殊工艺生产的隔热铝型材。要求的材料是6063铝型材的性能满足GB 5237.1-2008的性能指标,穿条复合型材交货时不时效,由客户要把型材加工成所需要的半成品后自己进时效炉进行时效。隔热条在时效时不能有变形、气泡等现象,时效后的型材必须满足GB 5237.6-2004的要求。所以对型材的隔热条的耐热性能和复合后的抗剪切特征值是一个新的挑战。
因为我们平时生产的隔热型材都是采用先时效后复合的工艺,这种状态下其内部组织基本稳定,复合后型材与隔热条的啮合力不再发生大的变化。而客户这种工艺要求我们在以前没有生产过,要保证型材既满足客户的这种工艺要求又要使型材达到国标要求,必须经过一系列的实验数据来证明其可行性。刚开始我们也走了些弯路不过也从中找到了用这种工艺生产隔热型材的经验,最终以较高的客户满意度完成了这次订单的生产任务,与这种工艺要求的客户建立了长期的战略合作关系。
为验证隔热铝型材性能,是否满足客户的这种特殊加工工艺要求,我们进行了以下试验。
3、试验过程与分析
本次试验分析我们首先采用了专门定制的耐高温I型隔热条。用未时效的型材,先使用耐高温I型隔热条将型材复合,截取成3段长度为2 m的型材,将其中1段进行未时效前的抗剪实验,另一段使用我们常用的200℃±5℃保温2小时的时效工艺,剩余的一段按180℃±5℃、保温4小时的时效制度进行时效处理。
对三段型材分别采用头尾各截掉200mm,然后按两头分别取样3个,中间取样4个,每个试样100mm,在剪切力试验机上进行试验抗剪特征值的实验,对实验后的数据进行分析,具体数据结果见表相应的表格(表1、表2、表3)。
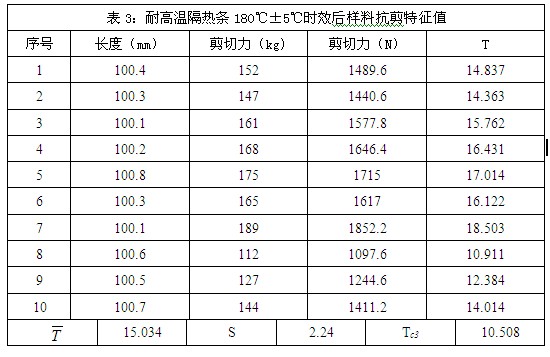
针对以上数据按GB5237.6-2004要求进行纵向抗剪特征值的计算方法如下:
按公式(1)计算各试样单位长度上所能承受的最大剪切力,再按公式(2)计算试样纵向抗剪特征值。
T=Fmax/L……………………………(1)
式中:
T------试样单位长度上所能承受的最大剪切力,单位为牛顿每毫米(N/mm)
L------试样长度,单位为毫米(mm);
Fmax------最大剪切力,单位为牛顿(N)
Tc=T—2.02*s…………………………..(2)
式中:
Tc--------纵向抗剪特征值,单位为牛顿每毫米(N/mm)
--------10个试样单位长度上所能承受最大剪切力的平均值,单位为牛顿每毫米(N/mm)。
s--------相应样本估算的标准差,单位为牛顿每毫米(N/mm)。
通过以上公式求得三次实验数据的标准差分别为s1=1.474、s2=2.483、s3=2.24
由标准差求的特征值分别为Tc1=45.118、Tc2=10.145、Tc3=10.508
通过以上数据可以发现,经过200℃±5℃、保温2小时和180℃±5℃、保温4小时的时效制度时效处理后,型材的抗剪特征值分别下降了77.5%和76.7%,且Tc2 、Tc3都小于GB5237.6-2004要求的纵向抗剪切特征值大于等于24N/mm的规定,时效后的型材都属于不合格品。
经过相关技术人员研究探讨与技术革新,我们对隔热条与型材的啮合过程及原理进行了分析,虽然在辊压后隔热型材有较高的纵向剪切力,在经过时效处理后,在约180℃-200℃的高温作用下,铝型材槽口的外夹头会因热胀冷缩的影响,而产生松动,不能紧密咬合隔热条(如图1所示),从而使得隔热型材的纵向剪切力大幅下降。
现在需要解决的一个技术难题就是在时效时设法增加隔热条与铝型材之间的啮合力,时效过后依然持续这种性能不发生改变,作为提高隔热铝型材剪切性能的有效途径。
经过多次讨论论证,我们发现一种新型的带热熔胶线隔热条可以弥补这一不足,常规耐高温隔热条头部如图2所示,带热熔胶线隔热条头部如图3所示。
热熔胶线在常温下是固体,卡在隔热条上;在时效过程中,当温度达到100℃左右时,热熔胶线开始熔化,熔融的热熔胶线填充满隔热条底部与铝型材间的间隙;当时效完后,温度开始下降,熔融的热熔胶便开始固化,并因其有较强的黏结性能,使得隔热条与铝型材黏结在一起,从而弥补因外夹头松动带来的剪切力损失。
采用带热熔胶线隔热条,我们又进行了以下试验,实验方法和取样方法与上次完全相同。具体数据结果见(表4、表5、表6)。
根据抗剪特征值计算公式,求得三次试验的的特征值分别为Tc4=51.959、Tc5=19.075、Tc6=48.837。
从试验数据分析可以发现:使用带热熔胶线隔热条的复合型材在时效前比普通耐高温隔热条特征值要高,在经200℃±5℃时效处理后,特征值下降了62.35%,不符合GB5237.6的要求,经180℃±5℃时效处理后,特征值下降了5.72%,依然满足GB5237.6-2004的要求,将以上数据结合试验现象进行分析发现,在200℃±5℃条件下进行时效,因温度较高,热熔胶融化溢出,不能起到其应有的黏合作用,而在180℃±5℃条件下时效,时效过程中,热熔胶在熔融状态下填充隔热条底部与铝型材间的间隙;当时效后,温度开始下降,熔融的热熔胶便开始固化,并因其有较强的黏结性能,使得隔热条与铝型材黏结在一起,从而有效弥补了因外夹头松动带来的剪切力损失。
4、试验结果与结论
本文通过对穿条式隔热型材经不同的热处理工艺前后的特征值变化进行对比分析,从而对“先穿条后时效”生产工艺在实际生产中的可行性进行了探讨。
①使用普通耐高温隔热条复合的隔热型材,先穿条后时效后,抗剪特征值下降76%以上,不能满足GB 5237.6-2004的要求;
②使用带热熔胶线隔热条复合的隔热型材,采用200℃±5℃,保温2小时时效后,抗剪特征值比时效前下降了62.35%,不能满足GB 5237.6-2004的要求
②使用带热熔胶线隔热条复合的隔热型材,采用180℃±5℃,保温4小时时效后,抗剪特征值比时效前下降了5.72%,依然能够满足GB5237.6-2004的要求;
④带热熔胶线隔热条在时效过程中,热熔胶在熔融状态下填充隔热条底部与铝型材间的间隙;当时效完后,熔融的热熔胶随温度下降逐渐固化,因其有较强的黏结性能,使得隔热条与铝型材黏结在一起,从而有效弥补了因外夹头松动带来的剪切力损失,从而实现“先穿条后时效”的生产工艺。