Since july 2007 Pezzorgna Armando s.r.l(PA),located near Mantua in ltaly, has been working on a contract from one of its best ltalian customers to plan, deliver and install its first fully automatic storage system for extrusion dies. The ‘Die-O-Matic-3000’ die storage system developed by PA is a classical, high-rise rack storage system with a rack-serving unit for 3,000 extrusion dies ,which can even be extended later on with modules, using the same recovery unit,for up to 6,500 storage places for extrusion dies. The storage system was delivered in May.
Pezzorgna Armando s.r.l,简称PA公司,位于意大利风景秀丽的曼托瓦。2007年为第一个意大利客户设计、制造和安装了第一套挤压模具系统。“O-MATIC-3000”是由PA公司开发的典型的高架挤压模具存储系统,可存放3000套挤压模具,并可扩展到6500套。此系统已于2007年5月发货。
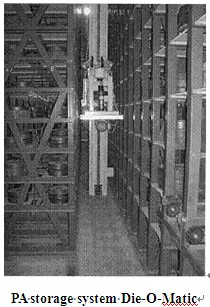
“O-MATIC” 模具存储系统
The currently available 3,000 dies are used on two extrusion presses (16 MN and 27 MN ). The dies are automatically stored in and recovered from the high-rise rack store, using a chaotic store-placement system computer controlled to optimize available storage space. With a height of 9 m , a width of 4.60 m and a length of 15 m, the high-rise store is comparatively compact for its size. The dies, stored in flat layers,have maximum diameter 300 mm, maximum depth 200 mm and maximum individual weight 220 kg.
现有的3000套模具系统用于有两个挤压机(16 MN and 27 MN)的工厂。采用随机存放-位移系统,计算机优化存储空间,实现模具于高架仓库中的自动存入和取出。仓库高9米,宽4.6米, 长15米,非常节省空间。模具存放于一个矩形的空间,可存放直径最大为300mm,厚度为200mm的模具,最大模具重量为220公斤。
The PA system can also be designed at any time for larger and heavier dies, and is moreover suitable for much larger item numbers. At present another automatic storage system for up to 20,000 dies is PA’s order books for delivery in May 2008.
PA公司也可设计、制造数量更多、重量更重的模具仓库:2008年设计、制造了一个20,000套模具的存储系统。
The cycle time for the recovery (or placement in store)of an extrusion die by the recovery unit is less than one minute. This ensures high plant availability, with around 60 double working operations per hour and short store placement and recovery times, achieved by travel speeds up to 40 m/min along the Y-axis,30m/minalong the X-axis and, with combined travel of the rack-serving unit, up to 20m/min.All drives are frequency-regulated and the entire plant is equipped with highquality components and controlled by a Siemens Simatic S7 SPS system.
模具的拾取时间(或在仓库内的位移时间)小于一分钟。为保证仓库的运行性能, Y轴运行速度40米/分,X轴运行速度30米/分,和上/下的运行速度20米/分,实现一个小时内的60个双运行和短程移动和拾取。所有的驱动由变频器调节,采用西门子的S7 SPS 系统控制。
The delivery by PA includes not only the frame and support structure of the high-rise rack store, the rack serving unit and the recovery/placement device, but also the full range of software and programming for all the plant’s cycles and automatic operations.
由PA生产的不光生产仓库框架,模具存储单元存取装置、拾取/位移装置,也同时提供整套的模具自动仓库的自动运行和管理软件。
The control system enables the storage and recall of the following individual cycles and parameters:
控制系统可按下述参数和状态对模具进行存入和拾取:
● individual die number for esch extrusion die, with all its historical data,
模具编号,以及所有历史数据
● classification category (flat,chamber,etc,) of each extrusion die,
模具分类(实心,空腔数等)
● brief designation of the die and its use,
模具的摘要和它的用途
● die status: ready for use, being etched, in use on a press, before or after nitriding, due for correction,etc.,
模具状态:可使用,待碱蚀,正在使用,氮化前或后,待修等。
● customer article number (for the associated section),
客户编码(与具体型材型号相关联)
● name of the customer for whom the die was designed,
客户名(模具为此客户而做)
● date when the die was last used, and tonnage extruded.
最后一次的使用日期,和已挤压的吨数
● date when the die was made,
模具制造日期
● press allocation for each die (including multiple fitting),
模具所配的挤压机(包括多重配置)
● linear section weight and number of apertures,
型材的线重量和孔径
● diameter and thickness of the die,
模具的直径和厚度
● die weight ,
模具重量
● supplier of the extrusion die in each case.
模具供应商
Further data, which may be important and appropriate depending on the customer’s needs, can also be recorded. The databank-based analysis and evaluation of the statistical data, times of use, number of times used,etc.,can be displayed at any moment. The die databank can also be linked to DXF-or DWG-data from Autocad or other CAD/CAM systems.
根据每个客户的具体需求,可以增加更多的数据。模具数据库分析、统计数据评估、使用时间的长短,、使用次数等数据,可随时显示出来。模具数据库可以与DXF,DWG, CAD/CAM系统相连,与可与AUTOCAD 系统相连。
The main advantages of automated die storage systems are:
模具仓库的自动化有以下优点:
● Improved storage conditions the dies are stored cleanly and in clearly assigned positions, which improves availability by eliminating search times.
改善存储条件下- 模具干净存放,并配有清楚的位置, 减少了寻找时间。
● Greater die availability compared with manual storage systems; no maintenance of floor-level trans porters is needed, and personnel costs are saved.
比人工存储极大提高了效率,地面的传送系统无需维护,减少了仓管人员。
● Back-tracing of the die’s use, since all its historical movement data are on record; this makes the life cycle of each die trnsparent.
所有历史数据都有记录,故可回朔模具的使用情况,在报废前对模具的使用情况一目了然。
● Compared with conventional storage system with manual placement or recovery, less space is occupied.
与传统的人工模具存储系统相比,节约空间。
● Substantially reduced risk of accidents, due to the elimination of manual die handling, especially in the case of heavy dies.
大量减少了事故的发生,由其是在人工搬运重模具时对重量估计不足发生的事故。
● Substantial rationalisation effect thanks to automated sequences, leading to a saving of personnel costs.
由于自动排序,更加合理化;也减少了人员费用。
At present the die article number is still recorded manually but PA is already working on a barcode- based automatic system. The use of corresponding scanners is reliable and speeds up the recording when the dies are put into store or recovered, so eliminating the risk of erroneous recording or erroneous registration in the database.
迄今为止,模具编号都是由人工记录的。PA公司已经着手开发模具用的条码系统。模具存储时使用扫描器更可靠,速度更快,消除了大量的人工记录错误。
The automatic extrusion die storage system can be set up either indoors, or in the open (isolated). With its own servicing and customer care facilities, PA also ensure that in Germany too, customers benefit from comprehensive availability and support for such highly complex systems, and therefore maximum utility of the automatic die storage system.
挤压模具自动仓储系统可以建于室内,也可设于敞开的空间(独立的)。由客户建立自已的设施,PA公司同样可以提供高效的存储系统,实现模具的自动存储,使客户获益。(如德国客户的例子)。