众所周知,铝材挤压模具最关键的部位是模孔的工作带。其中工作带的长度,角度,形状和表面粗糙度是影响铝型材成形和表面质量的关键因素。国内的挤压厂目前都是依靠人工打磨抛光,借助于角规,刀口尺和千分尺来对工作带的长度和表面进行检测和修正,其精度往往难于保证,另外作业人员的技能水平差距也直接影响到作业后的效果,引入三坐标测量机后,如何提高修模作业者的水平,如何进行型材问题的模具分析是本文要向大家介绍的。
1 三坐标测量机的系统构成,测量原理和测量模型
1.1 硬件构成
三坐标测量机硬件系统由三坐标测量机,人工操作平台,电脑控制系统和打印机组成。如图1所示,探测臂上的探测头可以在xyz三维空间移动和测量,电脑用于运行自动控制软件和进行数据处理,打印机用于输出测量结果。
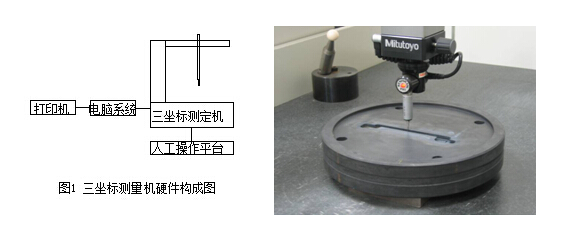
1.2软件系统的测量原理和二次开发的测量模型
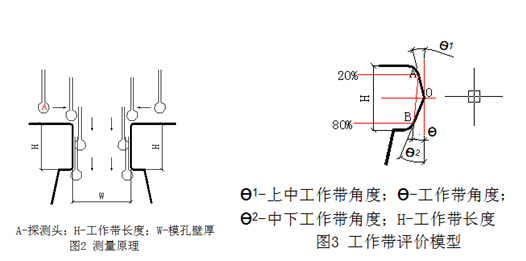
测量原理见图2,先在模具表面建立测量基准平面,然后将探头置于工作带边缘,启动相应的探测程序,探测头A沿着工作带表面进行点扫描,记录下每个点的坐标数据,测量终了后探测头归位,测量过程结束。
1.3工作带评价的理论模型
根据实际使用中工作带可能存在的形式,建立了一种评价理论模型,如图3所示,为了表述工作带轮廓形状的好坏程度(平面度),我们将工作带分为上中和中下两部分进行评价,引入了角差概念,为减少测量误差,计算时取工作带长度的20%-80%范围进行评估。
1.4 测量结果的表达和输出
测量的坐标数据经电脑系统处理后生成直观的文字和图形的表达形式,由打印机进行输出,易于对结果进行客观分析,标准输出结果如图4所示:
输出结果的信息包含:测量日期,模具型号,壁厚尺寸,工作带长度,工作带角度,上中工作带角度,中下工作带角度,角差,轮廓形状图。
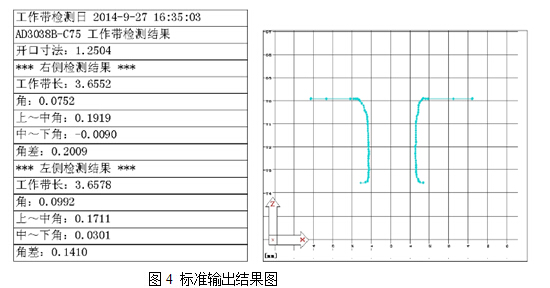
1.5 对测量结果的评价标准
基于我厂对修模作业的要求,设定工作带角度的作业标准为±0.05°管理范围为±0.1°
角差管理范围为±0.1°。超出此范围的皆为不达标。
2 利用三坐标测量机帮助修模者提高作业水平
2.1 首先我们建立了一个作业测量记录表,如图5所示,图中横轴代表着检测的工作带角度误差值,纵轴代表着表征工作带平面度的角差值,图中不同颜色的点代表着不同作业者抛光作业后的检测结果。
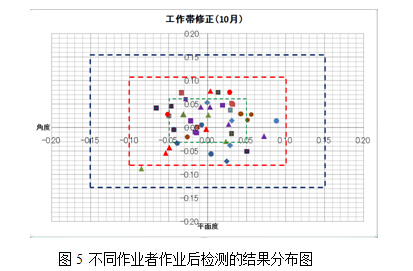
2.2建立作业检测结果的评估等级,如图6所示,A级,代表角度和角差均在±0.05°范围内,B级,代表角度和角差均在±0.1°范围内,C级,代表角度和角差均在±0.15°,对每位修模作业者要求每月自检2-3套模具,空闲时可以自行进行练习。
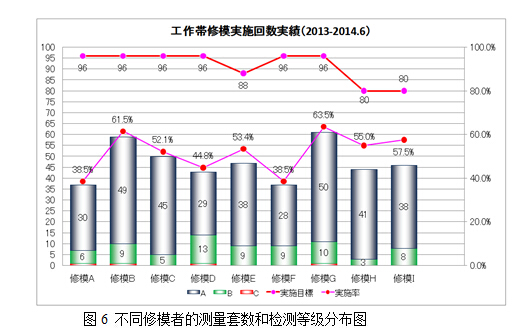
2.3上述模式在实施一年后所取得的效果,各位修模作业者技能水平都有了相当程度的提高,检测结果A级达标率达到80%以上,更重要的收获是挤压模具上机中止率由原来33%降到了现在的15%左右。
3 三坐标测量机用于分析铝材缺陷的模具问题的应用案例
挤压模具在使用一段时间后,或者经多次抛光作业后工作带都会出现不同程度的变形,如果能够定期将使用中模具用三坐标机进行检测,就能够预早的发现问题,并进行修正,杜绝不良的型材问题发生。下面是集中常见的缺陷问题分析。
3.1铝型材表面条纹增多,并伴有流点产生,将缺陷面模具工作带用三坐标机进行检测后发现工作带塌边较为严重,检测结果如图7所示,修正方法就是将工作带打磨抛光还原到最初状态。
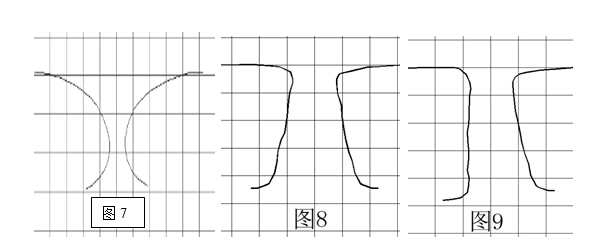
3.2多孔模具在使用一段时间以后出现了流速差,在排除了挤压机对中问题后,用三坐标机对模具进行检测,发现流速快的一孔工作带下塌比较多,形成了明显的负角度,如图8所示,修正方法就是将负工作带找正为90度,速差消除。
3.3 铝型材出料平面波浪,平面凸,用三坐标机对模具进行检测,发现波浪一侧的工作带产生了塌边,如图9所示,修正方法,将塌边一侧的工作带修正为+0.2-+0.4度的正角度。
4 结束语
介绍三坐标测量机在挤压修模中的应用方法,三坐标测量机可以在x,y,z三轴坐标空间进行任意点的坐标测定,测量精度可以达到1um,其应用软件也功能强大,还可以方便的进行二次开发,应用于不同的场合,国内许多行业都用三坐标测量机作为产品终检仪器。但在挤压修模上的应用,本公司走在国内同行业的前面,对提高修模者作业水平和进行型材缺陷的模具分析提供了可靠地方法和手段。三坐标测量机在修模间实际使用中起到了相当大的作用,帮助修模者提高了自己的技能水平,并帮助修模者分析生产中的模具问题,为修模者提供可靠了分析数据,修模者还用来对日常使用的角规进行定期校正。除此以外,我公司还用于对新模具进行终检质量验收,向模具制造车间和模具设计者反馈倾向和规律性数据用于改善相关工序。