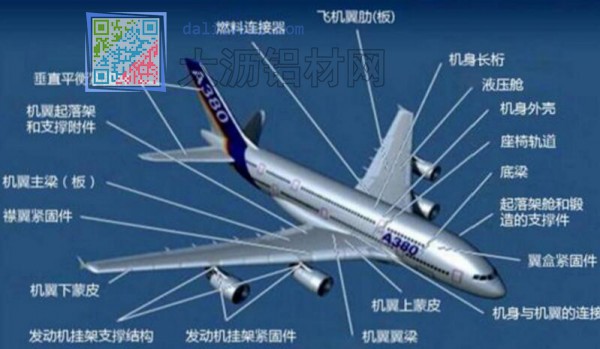
铝加工是指:用塑性加工方法将铝坯锭加工成材,主要方法有轧制、挤压、拉伸和锻造等。铝加工在20世纪初开始以工业方式进行生产,30年代以前,基本上沿用铜加工的生产设备,产品主要用于飞机制造。60年代后,铝材生产发展很快,每年大约增长4~8%,产品广泛应用于航空、建筑、运输、电气、化工、包装和日用品工业等部门。产量仅次于钢铁,居金属材料第二位。中国于50年代中期建成较大型的铝加工厂,形成了生产体系,产品已系列化,品种有七个合金系,可生产板材、带材、箔材、管材、棒材、型材、线材和锻件(自由锻件、模锻件)八类产品。
航空铝材开辟应用新蓝海
铝材在航空工业领域一直是关键性的结构材料,但近年来,随着技术的发展,铝材业也面临着来自其他材料的竞争,在民用飞机等用材中占的比例有下降的趋势。中国航空工业发展研究中心高级工程师胡燕萍在出席“铝材深加工论坛”时介绍,A380客机的结构材料中,铝合金占61%,B787客机铝合金用量则降到了20%。与此同时,复合材料的用量却直线上升。
尽管面临着其他材料的挑战,但胡燕萍指出,铝合金领域也在不断发展,在飞机发动机上也在寻找新的应用突破,如美铝公司与PW公司研制出了用铝合金材料制成发动机风扇叶片。此外,在新的飞机设计上,也逐渐显露了铝合金等金属材料回归的信号。B787的机翼承包商三菱重工把MRJ支线飞机的机翼材料设计由复合材料改回铝合金;A350XWB不是全用复合材料而是用先进金属材料与复合材料的混合结构。
根据波音公司对未来全球客机需求的预测,到2020年,飞机数量将达到33000架,相比目前24891架,增长33%左右;到2036年,全球飞机需求量将达到46950架,加上报废替换的,共计需要新增41030架飞机。
客机需求的增长将带来对材料的需求。安泰科预计,2017~2036年,民用飞机将累计需要用铝263万吨,其中铝材需要224万吨。
从国内来看,C919等国产飞机的研制成功也带动了对航空铝材及其零部件的强劲需求。随着我国航空工业进入高速发展时代,航空铝材市场需求将迎来大幅扩容。
但航空航天工业所用的高端铝材也是我国铝工业的短板,多年来一直维持净进口的局面。据悉,C919的铝材总质量占飞机总净质量的65%,但铝材主要以国外进口为主,C919上国产材料使用的比例也不大。
未来,中国C919干线客机、ARJ21及新系列支线客机等航空器项目,预计将把80%的航空铝板采购机会给中国本土企业。工信部《有色金属工业发展规划(2016-2020年)》中也明确表示将力推航空铝材国产化,将重点牌号铝材研制和应用列为2017年重点工作方案,力争突破技术壁垒,达到铝材全部国产化的目的。
这无疑为我国国产航空铝材的发展提供了良好的契机,我国航空用高端铝材存在巨大的进口替代和发展空间,但同时也增强了中国铝加工企业研发和生产航空民机铝合金的紧迫感。高端航空铝材仍是一片广阔的应用新“蓝海”,正等着中国铝加工企业“掘金”,而国产航空铝材的迫切需求也亟待中国铝加工企业加紧研发高端航空用铝材产品,提高产品质量,增强配套生产能力。
机壳铝合金化应用趋势明显
近年来,消费市场发展迅猛,铝合金由于具有高颜值、轻巧、高强度、高耐腐蚀性等特性,且更符合年轻人潮流时尚的消费观念,在3C电子中的应用不断增多。随着铝加工企业加工工艺与技术的不断成熟,铝合金成本日益下降,产品也更轻便、环保、美观,促使各类消费电子产品的外包装也在逐渐向铝合金材质转换。
数据显示,2016年手机铝合金机壳渗透率达到38%左右,平板电脑的渗透率达到50%左右,笔记本电脑的渗透率达到30%左右。
随着消费电子市场规模进入了平稳发展阶段,消费者及消费电子企业越来越重视产品的外观设计、材料工艺。
“创新是消费电子领域亘古不变的主题。”昆山千寻金属制品有限公司副总经理赵永军在“铝材深加工论坛”上表示,从目前消费电子的发展趋势上看,机壳的金属化已经成为外观创新的一大重要方向,并逐渐形成规模应用之势。他预计,2017年国内手机、平板电脑、移动电源、电视机四个消费电子领域对铝材的需求约为12万吨,2018年有望增至近20万吨。
但赵永军也指出,电子产品外壳金属化的首要因素是技术瓶颈的突破,从目前国内相关生产厂商来看,拥有外观整体解决方案能力的厂商极少,在冲压、压铸、全CNC等单一工艺方面具有优势的厂商也为数不多,市场需求得不到满足,产能倒挂严重。
他认为,应关注铝材料的新性能、新技术、新趋势及新应用,扩大铝材市场,进一步打通技术企业与品牌生产商之间的通道,是目前业内需要解决的问题。
建筑、交通、电子等下游行业的快速发展,不仅带动了铝需求的上升,也对铝材的精密加工成型技术与创新能力提出了更高的要求,铝材深加工具有广阔的市场前景。对于铝加工企业来说,在同质化竞争日益激烈的今天,顺应市场需求,大力开发精深加工铝材产品也将有助于其在竞争中脱颖而出,实现可持续发展。
引申阅读:铝加工材生产过程
管材、棒材、型材的生产 通常的工序是:先采用热挤压制成坯料,再经轧制(或拉伸)、精整和热处理制成成品。也可用热挤压法直接制成成品,现已由短锭发展为长锭挤压,按挤压机的挤压力用统一直径的铸锭,由分流组合模和舌形模挤制各种型材、管材,制品长度可达60米以上,经拉伸矫直后,切成所要求的长度。用于铝材生产的最大挤压机为20000吨。可挤成直径为800毫米的带肋管。建筑型材是60年代发展起来的挤压制品,已占挤压制品总量35%以上,其中80%用做门窗框。建筑型材几乎全部采用铝镁硅系合金(LD30和LD31)。这种制品经阳极氧化和着色处理,表面形成各种颜色氧化膜,具有良好耐蚀性,制成门窗美观耐用,密封性好。除热挤压外,还发展出冷挤压,等温挤压、无残料挤压和静液挤压等方法(见铝的氧化着色)。
铝和铝合金的挤压采用正向挤压法和反向挤压法。应依据不同合金选择适宜的挤压速度。为获得组织和性能良好的铝合金挤压制品,一次挤压成品时,型材,棒材的挤压系数(λ)大于8~12,供锻造用坯料的λ大于5。挤压模对挤压产品质量影响很大。挤压棒材、型材常用平模,管材则常用锥形模。挤压形状复杂的空心型材和管材,则广泛使用分流组合模和舌形模。有的采用液氮冷却挤压模,延长模子寿命和保证制品精度,一个模子可挤压30吨铝材。某些铝合金的挤压制品易出现“粗晶环”,即制品经热处理后,周边出现一层粗大晶粒区。高温挤压可以减轻这种现象。一些热处理可强化的铝合金挤压制品经固溶时效处理后,强度提高而塑性下降。
管材拉伸采用多条快速和盘筒拉伸,游动芯头盘管拉伸机卷筒直径达 630~2900毫米,拉伸管坯直径可达40~50毫米。拉管拉伸力为 16~18吨,拉伸速度为 24米/分,道次加工率一般为25~40%,此种工艺生产管材长度可达6000米。