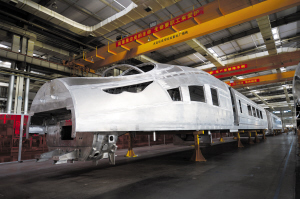
铝车体二车间里停放的动车车头
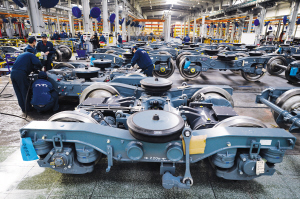
铝合金高速动车组制造中心
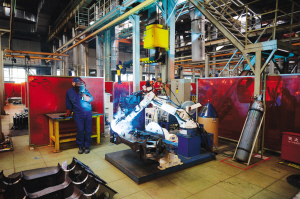
高寒动车的重要部件铝合金转向架
26日,本报记者赴长春独家探访了长客股份公司高速列车生产基地,了解哈大高铁列车“出生”和“长大”的全过程。
“机器人”焊接确保车体“天衣无缝”
哈大高铁使用的CRH380B型动车组列车从一个个零件和一片片建材,组建成一个成车是经过了多次组装和焊接而成的。
在转向架制造中心焊接场地内记者看见,在3.6万平方米的大型焊接厂房中,拥有6条焊接生产线。车间内大多数工人就是操作仪器完成大部分焊接工作。
长客股份公司焊接场地负责人表示:场地内配备的6条焊接生产线上拥有44台套的世界顶级品牌的机械手,这些机械手就像“机器人”的手臂一样,工作人员就需要提前将焊接的程序录入进系统中,这样机械手就能自如地焊接车体。这样的焊接能够实现焊接过后“天衣无缝”,即使是再小的部件也能够实现无缝焊接。
高铁列车“骨骼”铝合金防止热胀冷缩
哈大高铁CRH380B动车组列车主要由两大部分构成,一部分为车下的转向架,另一部分是车体部分。当你乘坐哈大高铁时,最直观感受到的就是车体部分。
据研发技术人员表示:“列车车厢的组装就像是我们日常盖房子一样,车体就像是我们房子中的龙骨一样,就是我们乘坐高铁列车的‘壳子’。车体内的结构材料都是采用特殊的铝合金材料制成的,这样可以保证列车的外部形状,还可以减轻列车的体重。”
哈大高铁全线需要运行在高寒地区,冬夏两季温差大,而铝合金制成的车体可以保证热胀冷缩范围幅度最小。
哈大高铁“娇气”厂房要求恒温恒湿
哈大高铁列车的生产基地对于环境的要求非常严格,置身于大型的厂房内记者没有感受到室外的寒风和一丝凉意。
哈大高铁列车外形庞大,但是对环境要求非常高,必须达到恒温恒湿的高标准。
高铁列车出产前需要在调试整备车间内进行最后的总装和调试工作,该车间也是整个哈大高铁建设过程中最大的一个车间厂房,厂房的长度达到了450米。这样哈大高铁列车就实现了贯连成一列车。
出厂前先模拟淋雨实验查看漏点
哈大高铁列车出厂前会在调试车间进行列车调试。哈大高铁列车在调试厂房内的列车整备线上可以进行整列模拟淋雨实验,查看车厢内是否出现漏点,确保列车防雨密封。
此外,在高速制造基地与长春小合隆站之间,长客公司研发生产部门还建有一条12公里长、最高试验时速达160公里的动车组动态试验线,出厂前列车都将在这里经过一系列的考验,合格后才能出厂交付使用。
全程2298公里的京广高速铁路为世界上运营线路最长的高速铁路,它的成功贯通,使广州到北京的行程缩短至8小时左右,最快仅需7小时59分。据技术负责人介绍说,高铁巨大的牵引力对车体材料的强度、降低风阻、抗腐蚀等方面提出了极为苛刻的要求,两年来,丛林集团在成功研发380公里、500公里动车组型材的基础之上,专注于京广线路车体型材的开发工作,依靠多年的核心技术和生产实践,先后解决了应力腐蚀、剥落腐蚀、疲劳腐蚀等技术难关,在熔炼铸造、模具设计制造、试验检测、后部处理等环节攻克高铁车体型材所要求的技术标准,并掌握了大部件焊接加工的要求,从而保证了车体的整体强度。